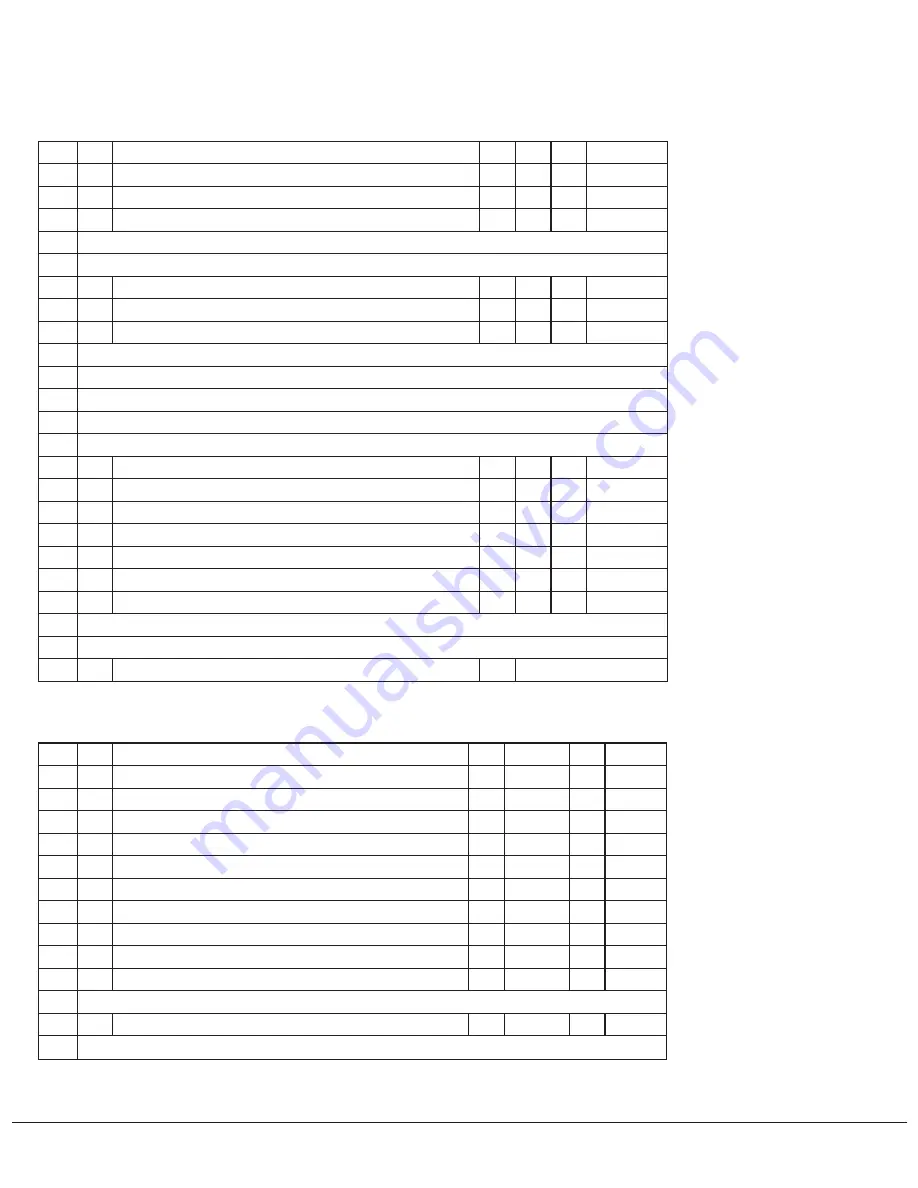
10.5 INPUTS AND OUTPUTS
10.5.1 IO block 1
Loc. ID
Description
Type Hi
Mid Low
X1.1 V02 Chamber open
DO
·1
·2
X1.2 V03 Chamber close
DO
·1
·2
X1.3 V04 Wrapper bypass off
DO
·1
·2
X1.4
---------- NOT IN USE ----------
X1.5
---------- NOT IN USE ----------
X1.6 V36 Elevator & door speed FB
FB
·2
X1.7 V36 Elevator & door speed
PWM ·1
X1.8 V40 Net brake release
DO
·1
·2
X1.9
---------- NOT IN USE ----------
X1.10
---------- NOT IN USE ----------
X1.11
---------- NOT IN USE ----------
X1.12
---------- NOT IN USE ----------
X1.13
---------- NOT IN USE ----------
X1.14 V08 Net knife cut
DO
·1
·2
X1.15 V17 Net feed rollers open
DO
·1
·2
X1.16 V18 Net feed rollers close
DO
·1
·2
X1.17 V19 Net feed motor
DO
·1
·2
X1.18 V35 Air cleaning, door (OPT)
DO
·1
·2
X1.19 S17 Chamber opened
DI
Bk
Bl
Br
X1.20 S18 Chamber closed
DI
Bk
Bl
Br
X1.21
---------- NOT IN USE ----------
X1.22
---------- NOT IN USE ----------
X1.23
Sensor supply
DO
X <----> X
10.5.2 IO block 2
Loc. ID
Description
Type Hi
Mid Low
X2.1 V01 Sub conveyor bypass
DO
·1
·2
X2.2 V37 S.conveyor & F.hopper speed
PWM ·1
X2.3 V37 S.conveyor & F.hopper speed FB
FB
·2
X2.4 V32 Chamber speed FB
FB
·2
X2.5 V32 Chamber speed
PWM ·1
X2.6 V25 Feed hopper on
DO
·1
·2
X2.7 V39 Elevator bypass
DO
·1
·2
X2.8 V24 Sub conveyor on
DO
·1
·2
X2.9 V51 Run Feed hopper
DO
·1
·2
X2.10 V52 Run flip
DO
·1
·2
X2.11
---------- NOT IN USE ----------
X2.12 S41 Elevator load (pressure)
AI
Wh
Br
X2.13
---------- NOT IN USE ----------
10 ELECTRICS
109
Содержание DENS-X
Страница 14: ...1 6 DECLARATION OF CONFORMITY 1 GENERAL 14 ...
Страница 98: ...8 6 4 Gearbox and gears for hydraulic motors Gear oil Renolin unisyn CLP 220N 8 LUBRICATION 98 ...
Страница 99: ...8 7 MANUAL LUBRICATION CHARTS 8 7 1 The compactor 8 LUBRICATION 99 ...
Страница 100: ...8 7 2 Feed hopper F10 8 LUBRICATION 100 ...
Страница 101: ...8 7 3 Telescopic drawbar 8 LUBRICATION 101 ...
Страница 105: ...10 1 MAIN POWER SUPPLY E STOP SWITCHES AND ELECTRICAL CABINET 10 ELECTRICS 105 ...
Страница 106: ...10 2 ELECTRICAL CABINET POWER SUPPLY RAIL 10 ELECTRICS 106 ...
Страница 107: ...10 3 SENSORS AND MANUAL CONTROLS 10 ELECTRICS 107 ...
Страница 108: ...10 4 VALVES FAN MOTORS AND PUMPS 10 ELECTRICS 108 ...
Страница 120: ...10 9 SENSOR OVERVIEW 10 ELECTRICS 120 ...
Страница 124: ...11 1 1 Complete diagram 11 HYDRAULICS 124 ...
Страница 125: ...11 1 2 Wrapping table chamber and elevator control 11 HYDRAULICS 125 ...
Страница 128: ...11 2 VALVE OVERVIEW 11 2 1 Valve chart for Hi X 11 HYDRAULICS 128 ...
Страница 132: ...12 6 3 Dimensional sketch F10 operating mode 12 SPECIFICATIONS 132 ...
Страница 133: ...12 6 4 Dimensional sketch F10 transport mode 12 SPECIFICATIONS 133 ...
Страница 137: ...M Maintenance 13 65 67 INDEX 137 ...