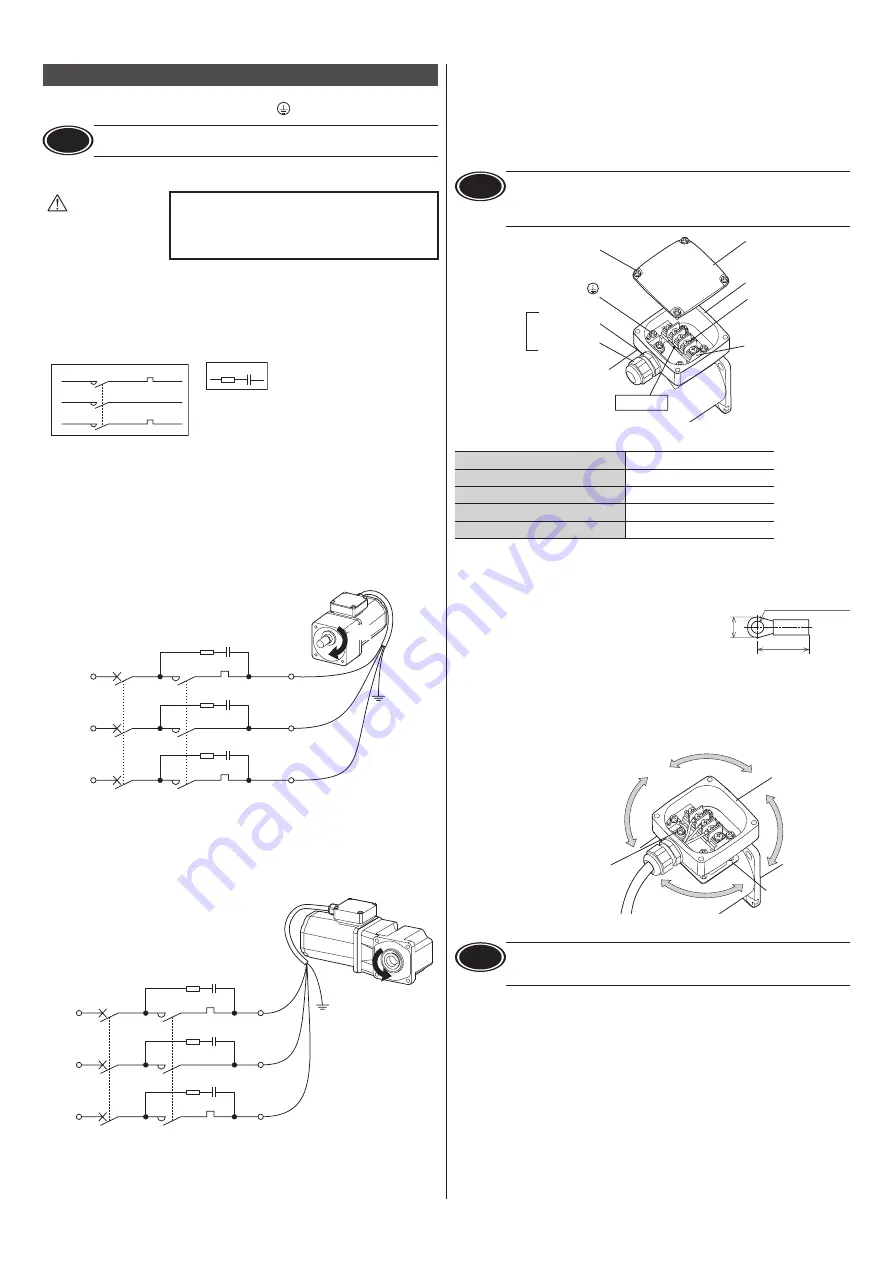
4
Connection
Insulate the connection part of the power supply.
Be sure to ground using the Protective Earth Terminal
inside the terminal box.
Note
Be sure to use the screw for protective earth terminal attached on the
product.
Connection diagram
CAUTION
The motor does not have a built-in overheat protection
device.
Use an electromagnetic switch to prevent the motor from
burning when an overload is applied or the output shaft is
locked. (Refer to p.5 for details.)
The figure shows a connection diagram when the motor is directly connected to a power
supply.
The symbols U, V, and W represent the terminal symbols inside the terminal box.
[Electromagnetic switch]
MC: Electromagnetic contactor
THR: Thermal relay
MC
MC
MC
THR
THR
[Measures for surge voltage]
Connect the CR circuit for surge suppression to
protect contacts as shown in the figure.
R
0
C
0
•
When the motor rated voltage is 200 to 240 VAC
R
0
= 5 to 200
Ω
C
0
= 0.1 to 0.2 µF 250 VAC
This is provided as a peripheral equipment (sold
separately).
Model:
EPCR1201-2
•
When the motor rated voltage is 380 to 415 VAC
R
0
= 5 to 200
Ω
C
0
= 0.1 to 0.2 µF 450 VAC
z
Combination type-parallel shaft gearhead, round shaft type
The output shaft rotates in the following direction if connected as shown in the figure.
Gear ratio
5
,
10
,
15
,
20
,
100
, and round shaft type: CW (clockwise direction)
Gear ratio
30
and
50
: CCW (counterclockwise direction)
Check the motor model name and gear ratio before connecting.
To change the direction of rotation, change any two connections
between R, S and T.
CW
R
0
C
0
L2(S)
L3(T)
L1(R)
MC
MC
MC
THR
R
0
C
0
R
0
C
0
THR
Grounding
W
V
U
z
Combination type-right angle hollow shaft hypoid gear
GV
gearhead
The output shaft rotates in the counterclockwise direction (CCW) if connected as shown in
the figure.
To change the direction of rotation, change any two connections
between R, S and T.
CCW
R
0
C
0
L2(S)
L3(T)
L1(R)
MC
MC
MC
THR
R
0
C
0
R
0
C
0
THR
Grounding
W
V
U
Connecting to the terminal block
Remove the terminal box cover to connect a cable.
Cables for connection are available as peripheral equipments (sold separately).
•
If the O-ring having set on the matching surface of the terminal box cover was detached,
install it firmly in the groove of the terminal box cover.
•
After connecting the cable, securely tighten with the tightening torque shown in the
table below.
Note
•
To maintain the sealing performance of the terminal box, keep the
applicable cable diameter and the tightening torque for screws.
•
Secure the cable exposed to the outside of the motor so that no stress is
applied.
Terminal block
Terminal box cover mounting
screw (M4-4 pieces)
Terminal box cover
Mounting screw
for terminal (M4)
Terminal box
Nipple
Tightening nut
Protective Earth Terminal
Cable gland
U V W
Terminal codes:
Tightening torque
Terminal box cover mounting screw
1.0 to 1.5 N·m (8.8 to 13.2 lb-in)
Mounting screw for terminal
1.0 to 1.2 N·m (8.8 to 10.6 lb-in)
Tightening nut
2.0 to 2.5 N·m (17.7 to 22 lb-in)
Nipple
2.0 to 2.5 N·m (17.7 to 22 lb-in)
Protective Earth Terminal
1.0 to 1.5 N·m (8.8 to 13.2 lb-in)
•
Use the following cable and crimp terminal when connecting the cable on the terminal
block.
Applicable crimp terminal: Round crimp terminal with
insulation cover
Applicable cable diameter: Ø7 to Ø13 mm
(Ø0.28 to Ø0.51 in.)
*
Applicable lead wire: AWG18 (0.75 mm
2
) or thicker
*
Round shaft type: Ø8 to Ø13 mm (Ø0.31 to Ø0.51 in.)
Ø4.3 (0.17) or more
[Unit: mm (in.)]
18 (0.71) or less
8 (0.31) or less
z
Changing the cable outlet position
The cable outlet position can be changed to the left or right 90-degree direction or the
180-degree direction.
When changing the cable outlet position, loosen the terminal box cover mounting screw,
rotate the terminal box to change the mounting direction.
Terminal box mounting screw
(M4-4 pieces)
Tightening torque:
1.0 to 1.5 N·m (8.8 to 13.2 lb-in)
Terminal box
Motor case
Gasket
Note
•
Be sure to use the gasket attached.
•
Assemble so that foreign objects are not entered between the terminal box
and the motor case.