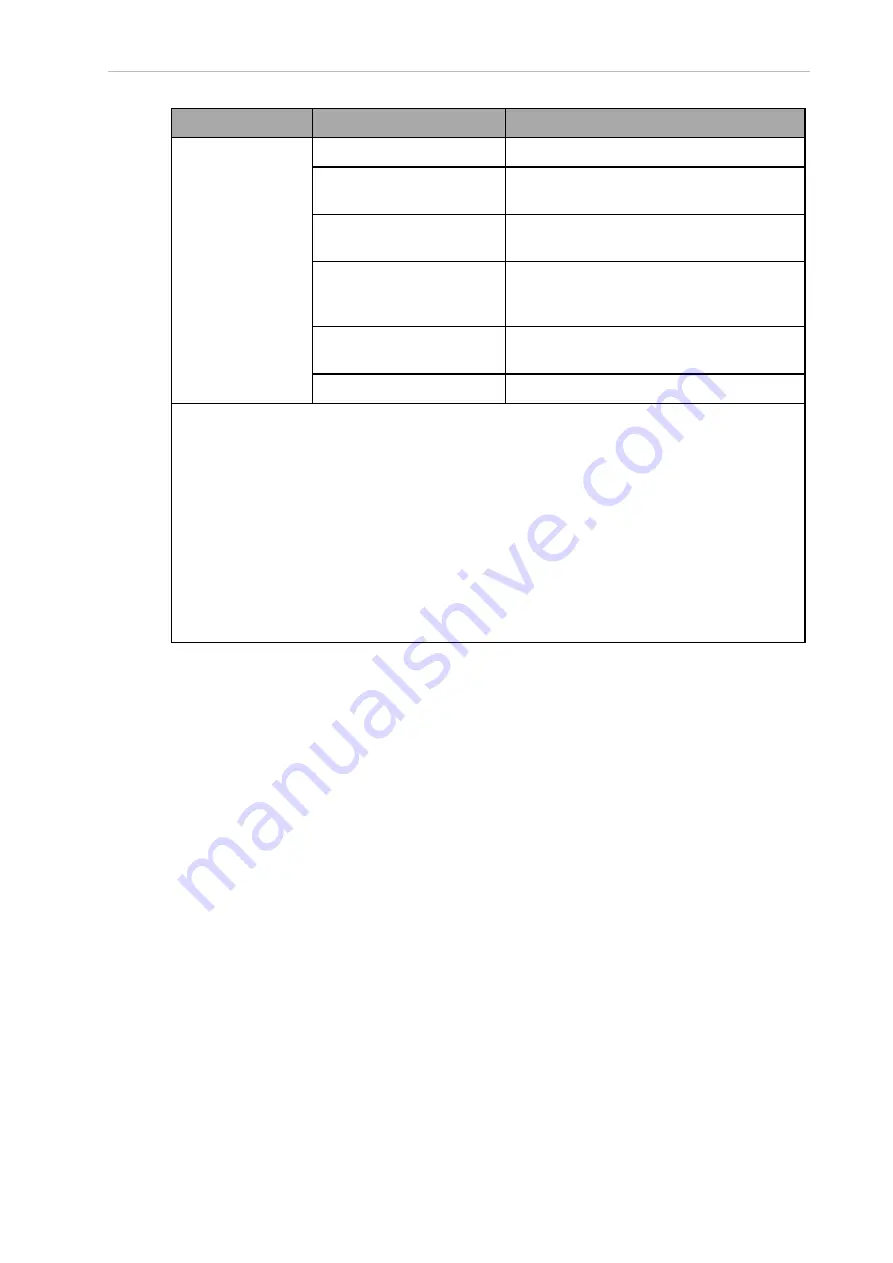
Chapter 8: Technical Specifications
Item
Specification
Details
current
ON response time
125 μsec max., 80 μsec typical (hardware
only)
OFF response time
60 μsec max., 28 μsec typical (hardware
only)
Output voltage at inductive
load turnoff (I
out
= 0.5A,
Load = 1 mH)
(+V - 65) ≤ V
demag
≤ (+V - 45)
DC short circuit current
limit
0.7A ≤ I
LIM
≤ 2.5 A
Peak short circuit current
I
ovpk
≤ 4 A
NOTE
1
: User-supplied 24 VDC power supply must incorporate overload protection to limit
peak power to less than 300 W or 8 A in-line circuit protection must be added to the 24 VDC
power source. For multiple robots on a common 24 VDC supply, protect each unit indi-
vidually.
Make sure you select a 24 VDC power supply that meets the specifications provided. Using
an under-rated supply can cause system problems and prevent your equipment from oper-
ating correctly.
NOTE
2
: Specifications established at nominal line voltage. Low line voltage can affect robot
performance.
NOTE
3
: If multiple robots are sharing a 24 VDC power supply, increase the supply capacity
by 3 A for each additional robot.
Facility Overvoltages Protection
You must protect the robot and eCS-ECAT from excessive overvoltages and voltage spikes. If
your country requires a CE-certified installation or compliance with
IEC
61131-2,
IEC
61131-2
requires that the installation must ensure that Category II overvoltages (i.e., line spikes not dir-
ectly due to lightning strikes) are not exceeded.
Transient overvoltages at the point of connection to the power source shall be controlled not to
exceed overvoltages Category II, i.e., not higher than the impulse voltage corresponding to the
rated voltage for the basic insulation. Your equipment or transient suppressor must be capable
of absorbing the energy in the transient.
In the industrial environment, nonperiodic overvoltage peaks may appear on mains power
supply lines. These can come from power interruptions to high-energy equipment (such as a
blown fuse on one branch in a 3-phase system), which will cause high current pulses at rel-
atively low voltage levels. You must take the necessary steps to prevent damage to the robot
system (such as by interposing a transformer). See
IEC
61131-4 for additional information.
8.5 Environment and Facility Specifications
The robot installation must meet the following operating environment specifications.
21861-000 Rev A
Viper 650 and 850 Robot with EtherCAT
123