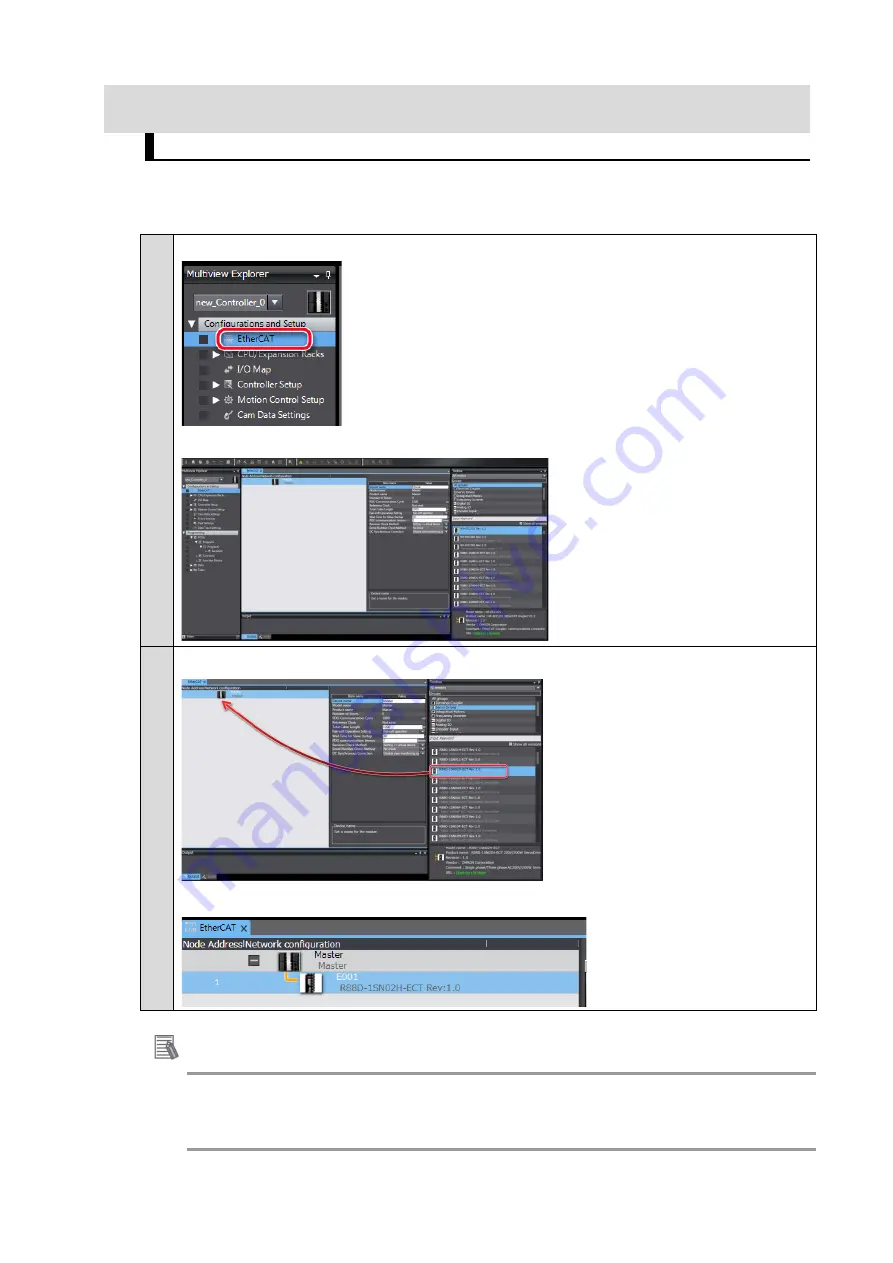
42
ANNEX
Add a drive and axis OFFLINE
■ Creating the EtherCAT Network Configuration
1.
Double-click EtherCAT under Configurations and Setups in the Multiview Explorer.
The EtherCAT Tab Page is displayed in the Edit Pane.
2.
Drag the Drive from the Toolbox to the master on the EtherCAT Tab Page
The Servo Drive is added under the master with a node address of 1.
Additional Information
If the physical EtherCAT network configuration is already connected, you can automatically create
the virtual network configuration in the Sysmac Studio based on the physical network configuration.
Refer to the Sysmac Studio Version 1 Operation Manual (Cat. No. W504) for specific procedures.
Содержание R88D-1SNx-ECT Series
Страница 1: ...Servo System 1S series Startup Guide R88M 1L 1M AC Servomotors R88D 1SN ECT AC Servo Drives I823 E1 01...
Страница 17: ...17 2 Approach the drive from top to down 3 Tight the upper part 4 Tight the down part...
Страница 38: ...38 6 Add the Emergency stop button 7 Add the Reset button 8 Edit I O Map variables...
Страница 58: ...58 11 Results Wizard step 5 Save to EEPROM Finish...
Страница 59: ...2016 0616 0616 I823 E1 01 Note Do not use this document to operate the Unit...