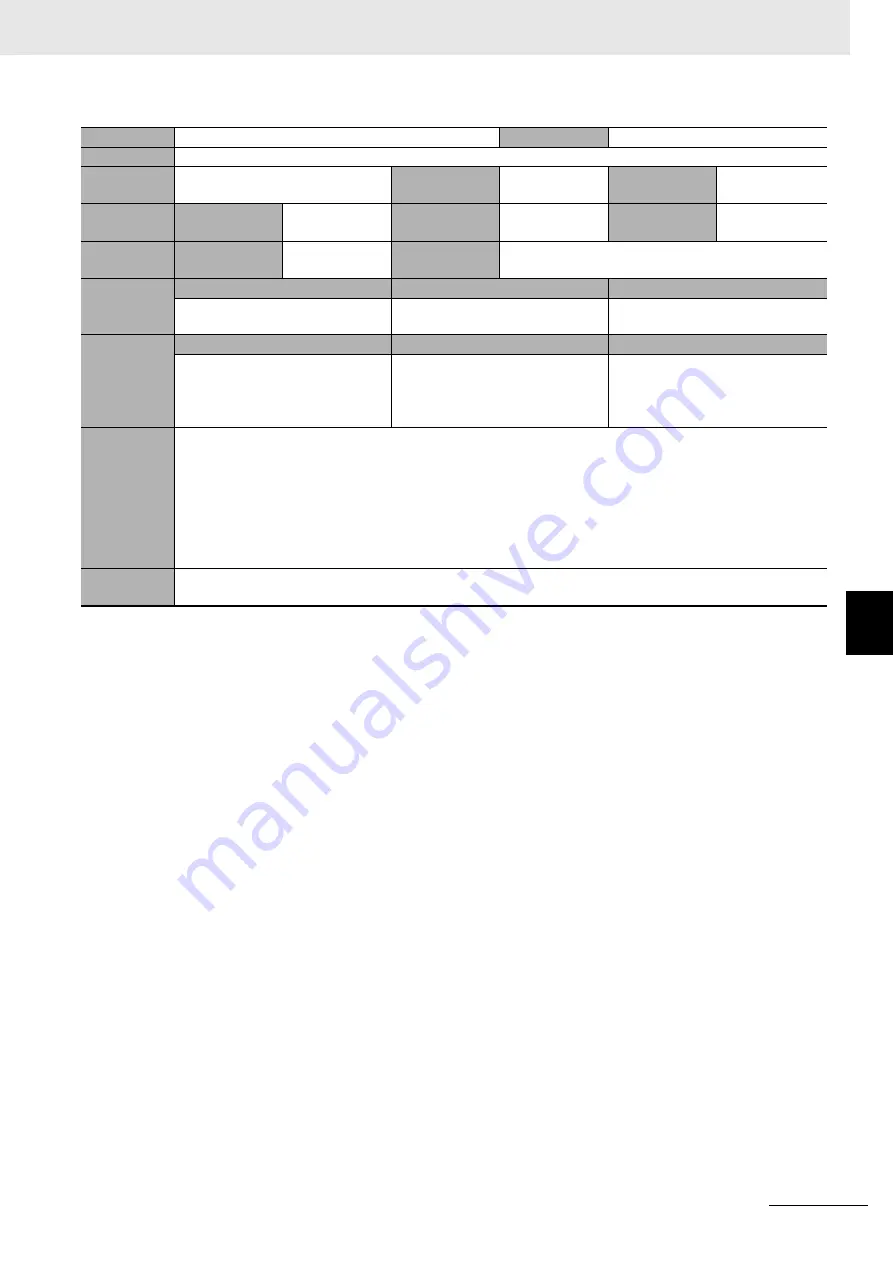
6 - 69
6 Troubleshooting
NJ-series NJ Robotics CPU Unit User’s Manual (W539)
6-2
Er
ro
r Descript
ion
6
6-
2-2 Err
or D
escriptions
Event name
Direction Selection Out of Range
Event code
5401542E hex
Meaning
The parameter specified for the
Direction
input variable to a motion control instruction is out of range.
Source
PLC Function Module
Source details
Instruction
Detection
timing
At instruction
execution
Error
attributes
Level
Observation
Recovery
---
Log category
System
Effects
User program
Continues
Operation
The relevant instruction will end according to specifi-
cations.
System-
defined
variables
Variable
Data type
Name
None
---
---
Cause and
correction
Assumed cause
Correction
Prevention
Instruction input parameter
exceeded the valid range of the
input variable.
Correct the parameter so that the
valid range of the input variable is
not exceeded for the relevant
instruction.
Set the input parameter to the
instruction so that the valid range
of the input variable is not
exceeded.
Attached
information
Attached Information 1: Error Location
Attached Information 2: Error Location Details (Rung Number). For a program section, the rung number from
the start of the section is given. For ST, the line number is given.
Attached Information 3: Names of the Instruction and Instruction Instance Where the Error Occurred. If there
is more than one possible instruction, information is given on all of them. Nothing is given if the instruction
cannot be identified.
Attached Information 4: Expansion Error Code (
ErrorIDEx
)
Precautions/
Remarks
If a program is changed after an error occurs, the attached information that is displayed may not be correct.
Содержание NJ501-4300
Страница 13: ...11 CONTENTS NJ series NJ Robotics CPU Unit User s Manual W539 ...
Страница 40: ...Revision History 38 NJ series NJ Robotics CPU Unit User s Manual W539 ...
Страница 90: ...2 Features of NJ Robotics CPU Unit 2 40 NJ series NJ Robotics CPU Unit User s Manual W539 ...
Страница 204: ...5 Vision Robot Integrated Simulation 5 6 NJ series NJ Robotics CPU Unit User s Manual W539 ...
Страница 308: ...6 Troubleshooting 6 104 NJ series NJ Robotics CPU Unit User s Manual W539 ...
Страница 333: ...I 1 I NJ series NJ Robotics CPU Unit User s Manual W539 Index ...
Страница 335: ......