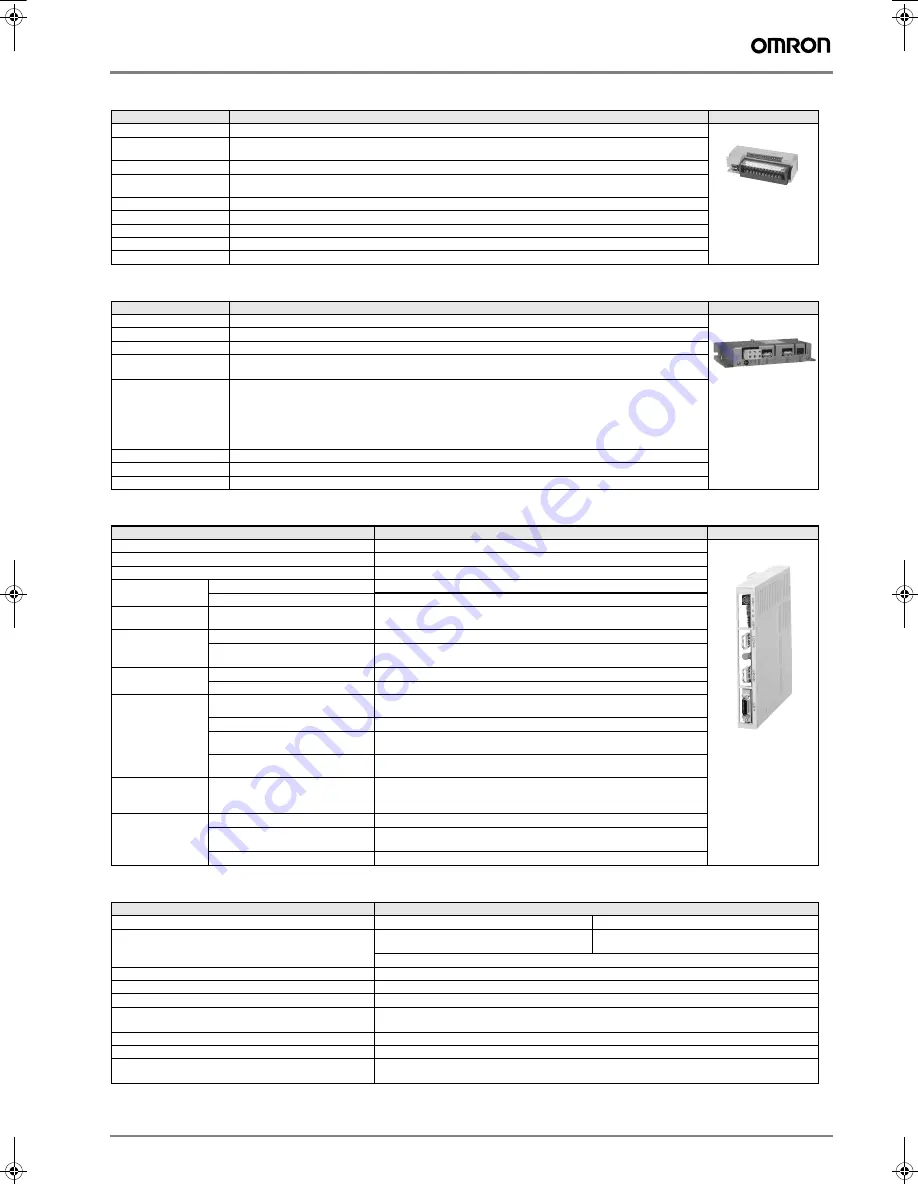
Motion controller
73
MECHATROLINK-II, analog output module (AN2910)
MECHATROLINK-II, repeater
MECHATROLINK-II, servo drive interface unit
MECHATROLINK-II, frequency inverter interface units
Items
Specifications
Appearance
Model
JEPMC-AN2910
Number of output
channels
2
Output voltage range
-10 V to +10 V
Max. allowable
load current
± 5 mA (2 k
Ω
)
Data format
Binary, -32000 to +32000
Output delay time
1 ms
Error
± 0.2% F.S. (at 25 °C), ± 0.5% F.S. (at 0 °C to 60 °C)
External power supply
24 VDC (20.4 VDC to 26.4 VDC), 120 mA max.
Weight
300 g
Items
Specifications
Appearance
Model
JEPMC-REP2000
Communication type
MECHATROLINK-II
Cable length
Between controller and repeater: 50 m., after repeater: 50 m
Max. connected
stations
Total stations on both sides of repeater: 30
(limited to the max. number of connectable stations of the controller (e.g., 21 stations for the MP2300 series))
Restrictions
Between controller and repeater
- Total cable length
≤
30 m: 15 stations max. including I/O and servo, etc.
- 30 m < total cable length
≤
50 m: 14 stations max. including I/O and servo, etc.
After repeater:
- Total cable length
≤
30 m: 16 stations max. including I/O and servo, etc.
- 30 m < total cable length
≤
50 m: 15 stations max. including I/O and servo, etc.
Power supply
24 VDC, 100 mA
Weight
340 g
Dimensions (mm)
30x160x77 (HxWxD)
Item
Details
Type
JUSP-NS115
Applicable servo drive
SGDH-
@@@
E models (version 38 or later)
Installation method
Mounted on the SGDH servo drive side: CN10.
Basic
specifications
Power supply method
Supplied from the servo drive control power supply.
Power consumption
2 W
MECHATROLINK -II
communications
Baud rate/transmission cycle
10 Mbps / 1 ms or more. MECHATROLINK-II communications
Command format
Operation specification
Positioning using MECHATROLINK-I/II communications.
Reference input
MECHATROLINK-I/II communications
Commands: position, speed, torque, parameter read/write, monitor output
Position control
functions
Acceleration/deceleration method Linear first/second-step, asymmetric, exponential, S-curve
Fully closed control
Position control with fully closed feedback is possible.
Fully closed
system
specifications
Encoder pulse output in the
servo drive
5 V differential line-driver output (complies with EIA Standard RS-422A)
Fully closed encoder pulse signal A quad B line-driver
Maximum receivable frequency
for servo drive
1 Mpps
Power supply for fully closed
encoder
To be prepared by customer.
Input signals in the
servo drive
Signal allocation
changes possible
Forward/reverse run prohibited, zero point return deceleration LS
External latch signals 1, 2, 3
Forward/reverse torque control
Internal functions
Position data latch function
Position data latching is possible using phase C, and external signals 1, 2, 3
Protection
Parameters damage, parameter setting errors, communications errors,
WDT errors, fully closed encoder detecting disconnection
LED indicators
A: alarm, R: MECHATROLINK-I/II communicating
Item
Details
Type
SI-T/V7
SI-T
Applicable inverter
CIMR-V7 / 3G3-MV
(firmware 5740 or newer)
CIMR-G7 / CIMR-F7
(firmware 656x/for G7 / 4011 or newer for F7)
Contact your OMRON sales office for information about firmware compatibility
Installation method
Mounted on the inverter
Power supply
Supplied from the inverter
MECHATROLINK-II communications
10 MHz, 0.5 ms to 8 ms for MECHATROLINK-II
Operation
Read and write registers, read monitors, inverter operation, speed reference, torque reference
(G7/F7 only).
Inputs and outputs
The inputs and outputs in the inverter can be read and set by the MLII master
Connectors
ML-II bus connector. DPRAM connector for the inverter
Switches
Rotary switch for ML-II address (low byte)
Dip switch for: ML-II address (high bit). ML-II/ML-I selection. 17 byte/32 byte data length selection.
NS115
Y203-EN2-02-Katalog.book Seite 73 Mittwoch, 24. Mai 2006 2:22 14