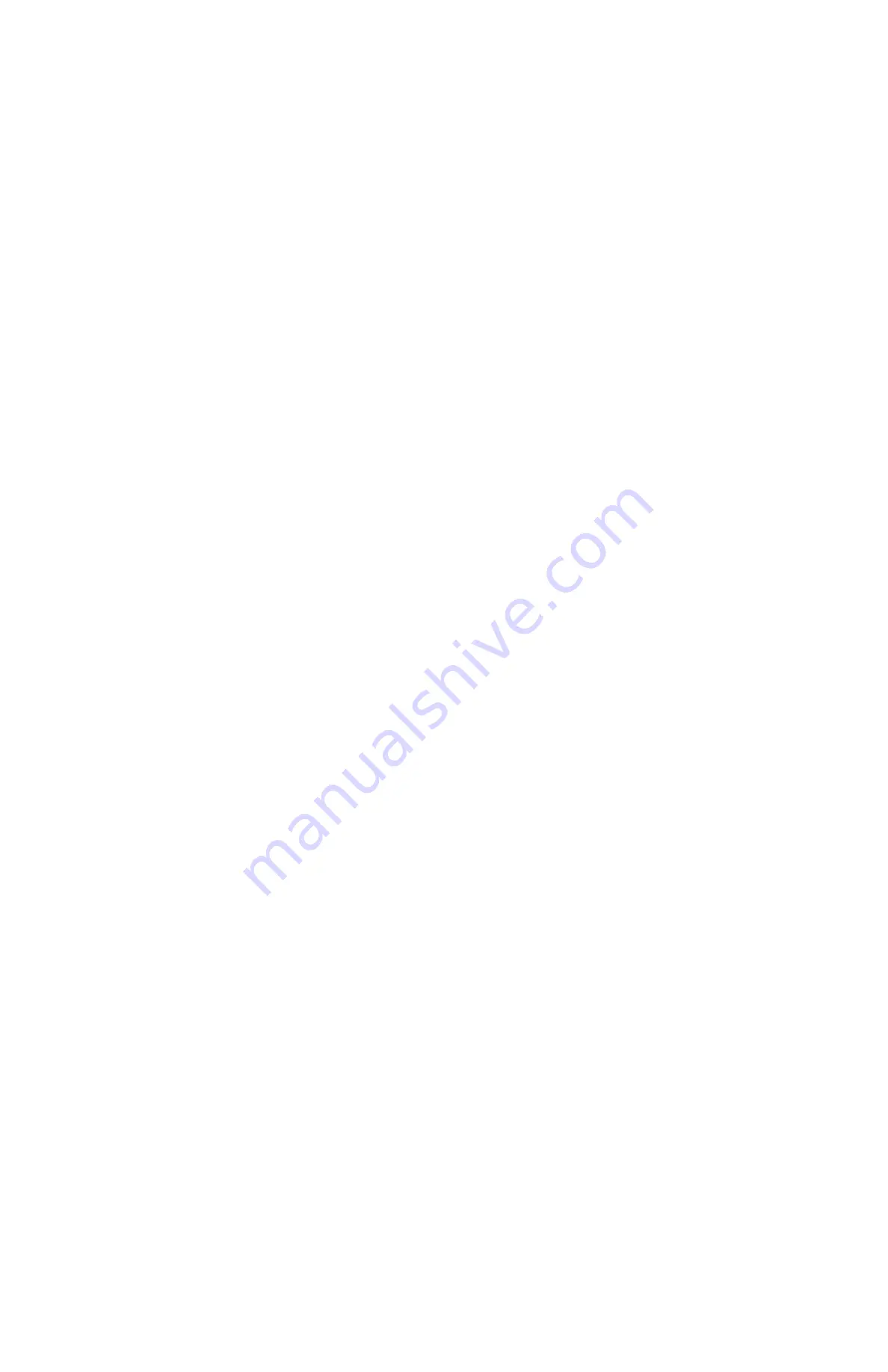
573
SECTION 10
Program Example
The section provides a programming example to demonstrate how the CJ1W-MCH71 and CS1W-MCH71 Motion Control
Units can be used.
Positioning with PTP Control . . . . . . . . . . . . . . . . . . . . . . . . . . . . . .
Positioning with Linear Interpolation . . . . . . . . . . . . . . . . . . . . . . . .
Positioning with Linear and Circular Interpolation. . . . . . . . . . . . . .
Positioning with Position Data . . . . . . . . . . . . . . . . . . . . . . . . . . . . .
Positioning with Workpiece Coordinate System with Subprograms
Positioning with Changing Interpolation Acceleration Time Parameter
Positioning with Position Data Calculation . . . . . . . . . . . . . . . . . . .
Stopping a Program with General Input . . . . . . . . . . . . . . . . . . . . . .
10-1-10 Positioning of Turntable . . . . . . . . . . . . . . . . . . . . . . . . . . . . . . . . . .
10-1-12 Starting Peripherals during Axis Movement . . . . . . . . . . . . . . . . . . .
10-1-13 High-speed Positioning . . . . . . . . . . . . . . . . . . . . . . . . . . . . . . . . . . .
10-1-14 Interrupt Feeding (MOVEI) . . . . . . . . . . . . . . . . . . . . . . . . . . . . . . .
10-1-15 Time-specified Positioning (MOVET) . . . . . . . . . . . . . . . . . . . . . . .
10-1-16 Regular Winding to Rough Winding (MOVETRAV) . . . . . . . . . . . .
10-1-17 Electronic Cam, Single Axis (CAM) . . . . . . . . . . . . . . . . . . . . . . . .
10-1-18 Link Operation (MOVELINK) . . . . . . . . . . . . . . . . . . . . . . . . . . . . .
10-1-19 Electronic Cam, Synchronous (CAMBOX) . . . . . . . . . . . . . . . . . . .
10-1-20 Electronic Shaft (CONNECT) . . . . . . . . . . . . . . . . . . . . . . . . . . . . .
10-1-21 Trailing Synchronization/Synchronization Cancel (SYNC/SYNCR)
10-1-22 Travel Distance Superimpose/Travel Distance Superimpose Cancel
(ADDAX/ADDAXR) . . . . . . . . . . . . . . . . . . . . . . . . . . . . . . . . . . . .
10-1-23 Speed Control/Speed Control Cancel (SPEED/SPEEDR) . . . . . . . .
10-1-24 Torque Control/Torque Control Cancel (TORQUE/TORQUER) . . .
10-1-25 Target Position Change (MOVEMODI) . . . . . . . . . . . . . . . . . . . . . .
10-1-26 Present Position Latch (LATCH) . . . . . . . . . . . . . . . . . . . . . . . . . . .
10-1-27 Single Block Ignored (NSTOP) . . . . . . . . . . . . . . . . . . . . . . . . . . . .
10-1-28 Parallel Execution (PARALLEL, JOINT, JWAIT) . . . . . . . . . . . . . .
10-1-29 Selective Execution (SWITCH, CASE, BREAK, SEND) . . . . . . . .
Using 64-Point I/O Module. . . . . . . . . . . . . . . . . . . . . . . . . . . . . . . .
Using Counter Module . . . . . . . . . . . . . . . . . . . . . . . . . . . . . . . . . . .
Using Pulse Output Module . . . . . . . . . . . . . . . . . . . . . . . . . . . . . . .
Содержание CS1W-MCH71 -
Страница 2: ...CS1W MCH71 CJ1W MCH71 Motion Control Unit Operation Manual Revised June 2008 ...
Страница 3: ...iv ...
Страница 29: ...xxx ...
Страница 33: ...xxxiv ...
Страница 35: ...xxxvi ...
Страница 39: ...xl ...
Страница 69: ...24 Performance Section 1 7 ...
Страница 99: ...54 Connecting MECHATROLINK Devices Section 3 5 ...
Страница 283: ...238 Saving Data Section 5 4 ...
Страница 417: ...372 Command Details Section 6 3 ...