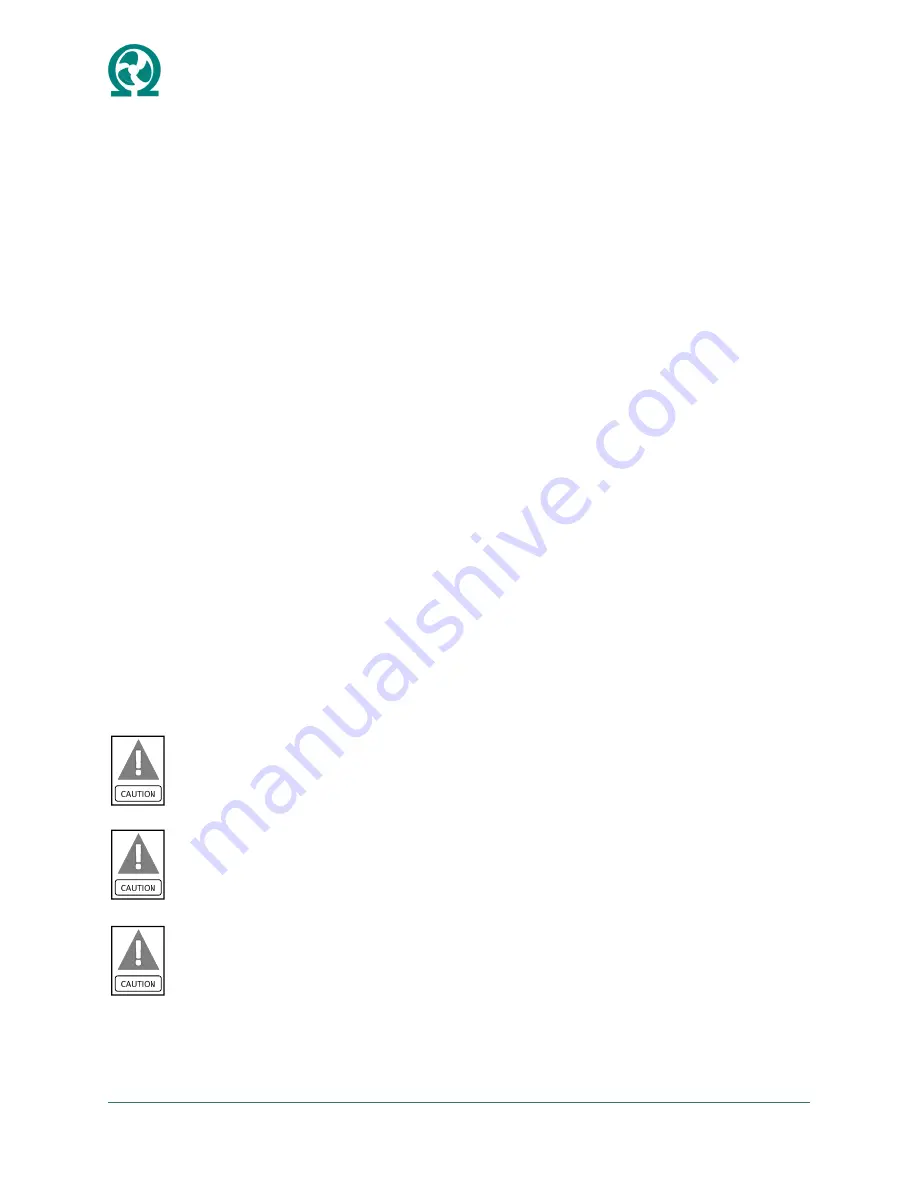
OMEGA | WATER SOURCE HEAT PUMPS
OMEGA-VSHP.G-IOM-2103
7
opening. Align the risers to the matching swaged section
of the riser on the floor below.
4) Swaged sections are approximately 3 inches deep.
Risers should be inserted at a depth of approximately 2
inches into the 3 inch deep swage. Confirm risers pene-
trate at a minimum of 1 inch into the swage. Do not allow
the riser tailpiece to bottom out fully into the 3 inch deep
swage. This will allow for floor to floor variations, other-
wise riser overlap may not be sufficient on upper floors.
See Figure 6.
5) Align and center riser positions in the pipe chase and
level cabinet as necessary.
6) Secure the cabinet to the floor. Cabinet base comes
with factory mounted neoprene pads.
7) Center the riser stub-outs in the cabinet openings to
allow for riser expansion and prevent contact with cabi-
net sheet metal. Prevent riser stub-outs from contacting
sheet metal pass through otherwise damage to stub-
outs may occur, resulting in serious water damage. See
Figures 7 & 8.
8) Secure risers to building structure as per engineering
design specifications. Do not allow the risers to be sup-
ported by the cabinets. Field supplied riser compensa-
tors are required if the temperature range of the system
exceeds the expansion and contraction limit.
9) Using industry accepted soldering and brazing stand-
ards and materials to solder or braze the riser joints.
10) Connect supply ducts and discharge grilles.
11) Connect to optional Fresh Outside Air Duct (Snorkel)
when connecting to remote ERV.
RISER LOOP
Do not connect chassis to the water circulat-
ing system when flushing is being conducted
to prevent debris and fouling of the water side
components of the chassis (i.e. auto balanc-
ing valve, auto shut-off valve, coaxial coil).
Do not flush and clean riser system with chas-
sis units connected. Do not allow the flushing
and cleansing solutions to flow in the chassis
water coil. Damage to water components
may occur.
Do not let untreated, standing and/or stag-
nant water sit inside chassis. Connect
chassis water connections by opening
isolation valves only when riser system is
treated and flowing.
Servicing
To enable system flushing, servicing and balancing of
supply and return risers the following field supplied com-
ponents are required: shut-off valves, drain tees and
drain valves, and flow measuring devices. Refer to the
job site engineering design specifications and building
drawings for more detailed information.
Flushing & Cleaning
Once the riser system is complete the riser system must
be cleaned and flushed, refilled and chemically treated
with industry accepted inhibitors. Untreated riser loop
water will result in premature wear and potential failure
of system components due to water coil leaks inside
chassis. Filters must be installed in riser loop system
and checked, cleaned as per regular maintenance
schedule.
Supply and return pipes must be interconnected, at a
minimum in the top and bottom units of each riser, with
factory supplied hoses to properly flush system and en-
sure adequate elimination of foreign material and clean-
ing of riser system.
1) Use only clean water to fill water circulation system.
Fill the water circulating system at the municipal water
makeup connection with all air vents opened.
2) After air vents have been sequentially closed and
riser system is primed begin water circulation of the sys-
tem to purge remaining trapped air bubbles.
3) Shut off the circulating pump and open all the drains
and vents to completely drain the system.
4) The riser system should be cleaned after the initial
flush and flushed a second time to adequately rinse the
riser system of cleaning solution.
5) Riser system is then re-filled with clean city water and
chemically treated to inhibit corrosion, oxidization and
fouling of the riser loop system. Do not use untreated
water to run heat pump chassis units.
Chassis installation is permitted once the riser sys-
tem is thoroughly flushed, cleaned, and commis-
sioned by the riser treatment company and contrac-
tor.
RISER SYSTEM LOOP TEMPERATURE
Correct riser system loop temperature settings are im-
portant for optimal unit operation. Temperatures outside
of the recommended range will affect overall unit operat-
ing performance (capacity and efficiency), long term
reliability and sound performance.
Cooling Season
In cooling mode recommended riser loop temperatures
should be maintained between 85
o
F to 90
o
F. Higher riser
loop temperatures reduce unit cooling capacity and effi-
ciency and may increase sound levels. Lower riser loop