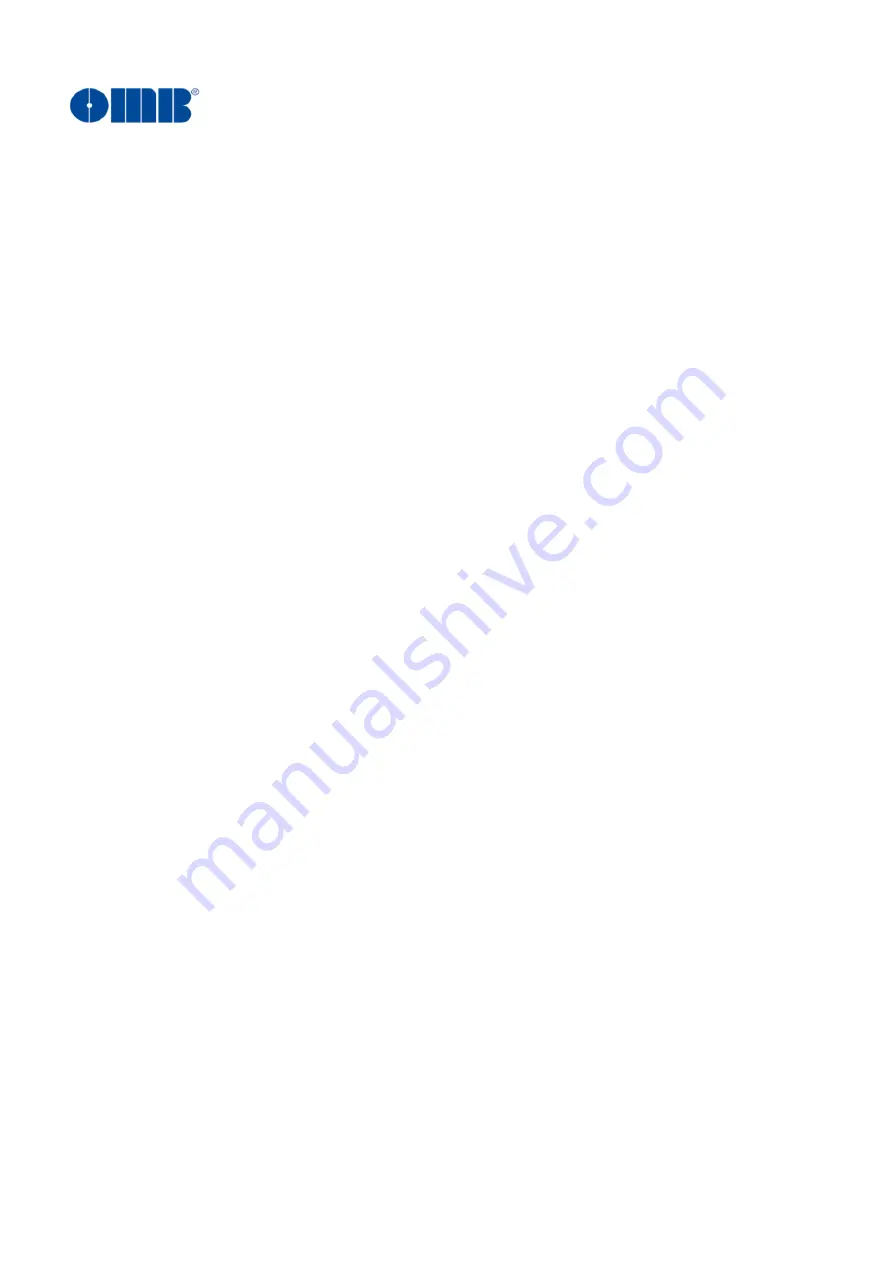
OMB Valves S.p.A
. Forged steel GATE, GLOBE & CHECK Valves Installation, Operation and Maintenance Manual Rev.5- 2016
Via Europa,7 Cenate Sotto 24069 (BG) Italy
Tel: +39 035 4256711
Fax: +39 035 942638
www.ombvalves.com
18
7. ASSEMBLY AND DISASSEMBLY
THREADED END VALVES:
•
Threaded end valves are disassembled by loosening the thread bolt. (If permitted apply few drop of oil to
thread helps loosen the bolt).
•
For Threaded End Valves, it is important to ensure about tight sealing.
•
Thread connection on valve and pipe must be checked to be correct, clean and without any imperfection.
•
Internal length of the thread in the valve end and its distance with the seat and plug must be considered
to avoid any possible damage could cause by pipe end to seat or wedge/disc whilst assembling.
•
If no requirement for dry seal threading specified, using appropriate thread sealant tape or pipe dope or
compound is recommended.
•
Thread must be accurately aligned at the point of assembly.
FLANGED JOINT VALVES:
•
For Flanged Joint Valves, safe sealing depends on the tension created in fasteners which clamp the joint
components together , applied force must be great enough to resist failure of the seal but do not damage
the fasteners , joint components and gasket.
•
Flange facing must be check to assure they are clean and free from radial groove cut or dent across the
face.
•
Bolting size, length and material must be check.
•
Gasket material must be checked, also ensure that they are free from any imperfection or damage.
•
Flange to be assembled must be aligned correctly. It must be considered accurately parallel whilst the valve
is assembling into the system.
•
Torque wrench shall be used for final tightening of flange bolting.
•
Using torque wrenches is highly recommended to ensure the correct bolt tightening and loading.
WELDED END VALVES:
•
All types of valves supplied by OMB and manufactured with Screwed Ends, Socket Weld Ends (S.W.E.), and
Butt Weld Ends (B.W.E.) have good welding properties
.
•
Welding end surface must be inspected before welding to be clean and have correct dimension.
•
Socket weld and butt weld end valves shall be temporarily fitted in line, and the ends tack-welded to the
piping for alignment and adjustment of pipe and valve end.
•
Socket weld valve should be lightly closed prior to welding. Welding should be done in horizontal or flat
position. If required vertical welding, upward progress should carry out.
•
Carefully lift out the center section, making sure that the seats and body seals are held in position. Place
the center section in a clean area where it will not be damaged, and complete the welding of the end caps
to the piping.
•
Weld thickness of Butt weld valves must be approximately equal to that of the pipe.
•
Finished weld must be inspect and properly clean.