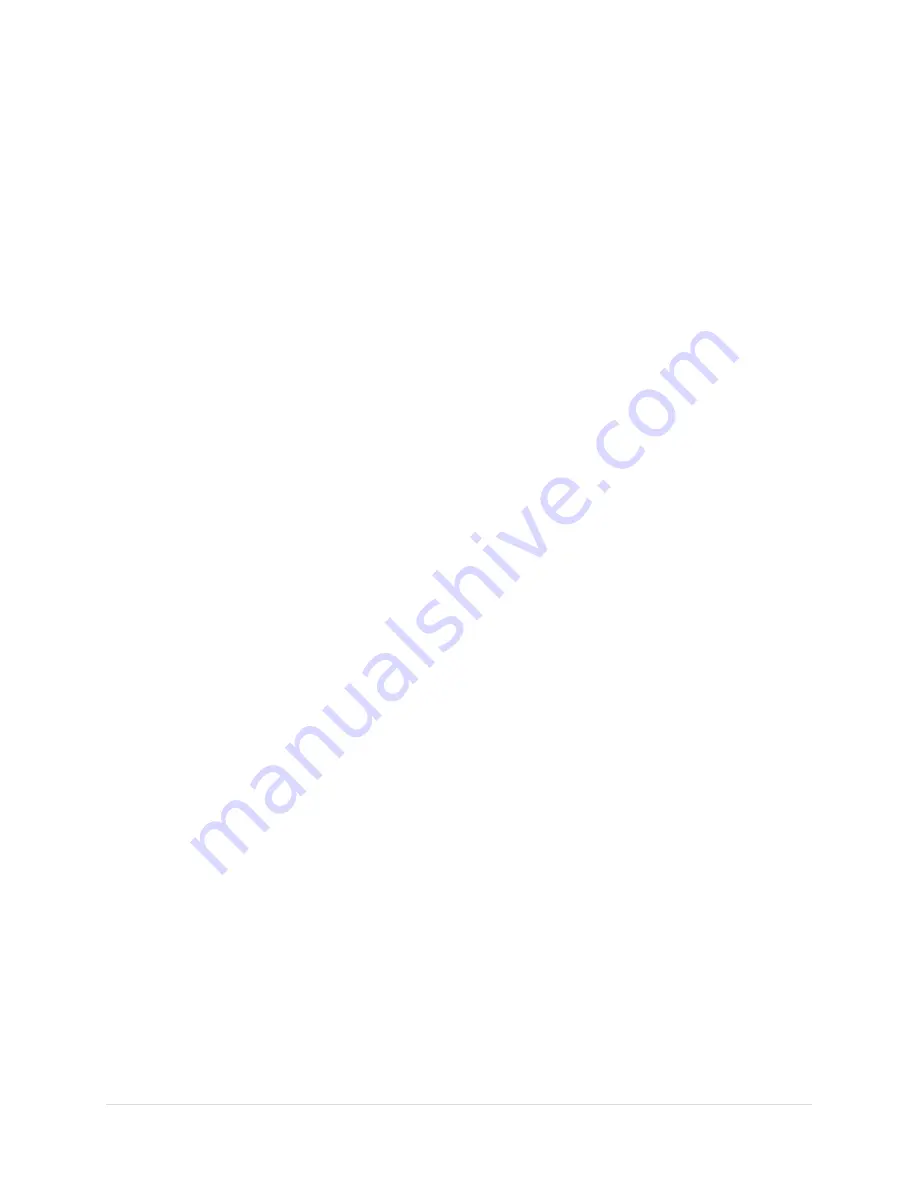
Table of Contents
Introduction············································· 5
Specifications ·········································· 6
Identification ··········································· 9
Safety ·····················································11
General Safety Guidelines ························· 11
Safety Guidelines Specific to Jointer ·········· 12
Electricals ···············································14
Minimum Circuit Size Required for Model
4235 Jointer ············································· 14
Grounding ················································ 14
Electrical Wiring ······································· 14
Setup ······················································16
Shop Preparation······································ 16
Space Requirement ········································· 16
Load Limits ······················································ 16
Electricals ························································ 16
Lighting ···························································· 16
Safety Labels ··················································· 16
Dust Collection ················································ 16
Receiving ·················································· 17
Cleaning ··················································· 19
Assembly ················································· 20
Dust Collection ········································· 22
Controls and Components ·······················23
Powerswitch ············································ 23
Infeed Table Adjustment ·························· 23
Infeed Table Depth Stop Knob ·················· 23
Outfeed Table Height Adjustment ············· 24
Fence ······················································· 25
Test Run ··················································· 26
Operation ···············································27
Preparation ·············································· 27
Inspect Wood Grain ·································· 28
Squaring Stock ·········································· 28
Surface Planing ········································· 29
Edge Jointing ············································ 31
Beveling ··················································· 31
Rabbet Cutting ········································· 32
Common Cutting Problems ······················· 33
Snipe ································································ 33
Chipping ·························································· 33
Fuzzy Grain ······················································ 33
Accessories ············································ 34
Maintenance ········································· 35
Maintenance Schedule ····························· 35
Inspect / Adjust Jointer Tables ·················· 36
Inspect Outfeed Table Height ························· 36
Adjust Outfeed Table Height ··························· 36
Inspect Outfeed Table Parallelism ·················· 37
Inspect Infeed Table ········································ 37
Adjust Table Parallelism/Coplanarity ·············· 38
Infeed Table Adjustments ······························· 40
Infeed Table Depth Stop Adjustments ············ 41
Rotate / Replace Cutter Inserts ················· 42
Adjust Fence Positive Stops ······················ 43
Adjust Belt Tension ··································· 45
Align Belt Pulleys ······································ 46
Troubleshooting ····································· 47
Mechanical / Electrical Issues ···················· 47
Operation / Quality-Related Issues ··········· 48
Wiring Diagram ····································· 50
Parts List ················································ 51
Maintenance Record ······························ 60
Notes ····················································· 61
Warranty and Service····························· 62
Appendix ··············································· 63
Metric Conversion Chart ····· 63
Содержание 4235
Страница 2: ......
Страница 9: ...4235 Jointer OLIVERMACHINERY NET 9 Page Identification ...
Страница 10: ...10 Page Oliver Machinery 4235 Jointer ...
Страница 50: ...50 Page Oliver Machinery 4235 Jointer Wiring Diagram ...
Страница 51: ...4235 Jointer OLIVERMACHINERY NET 51 Page Parts List Fence Assembly ...
Страница 52: ...52 Page Oliver Machinery 4235 Jointer Table and Cutterhead Assembly ...
Страница 53: ...4235 Jointer OLIVERMACHINERY NET 53 Page Motor and Cabinet ...
Страница 54: ...54 Page Oliver Machinery 4235 Jointer Base Assembly ...
Страница 60: ...60 Page Oliver Machinery 4235 Jointer Maintenance Record Date Task Operator ...
Страница 61: ...4235 Jointer OLIVERMACHINERY NET 61 Page Notes ...