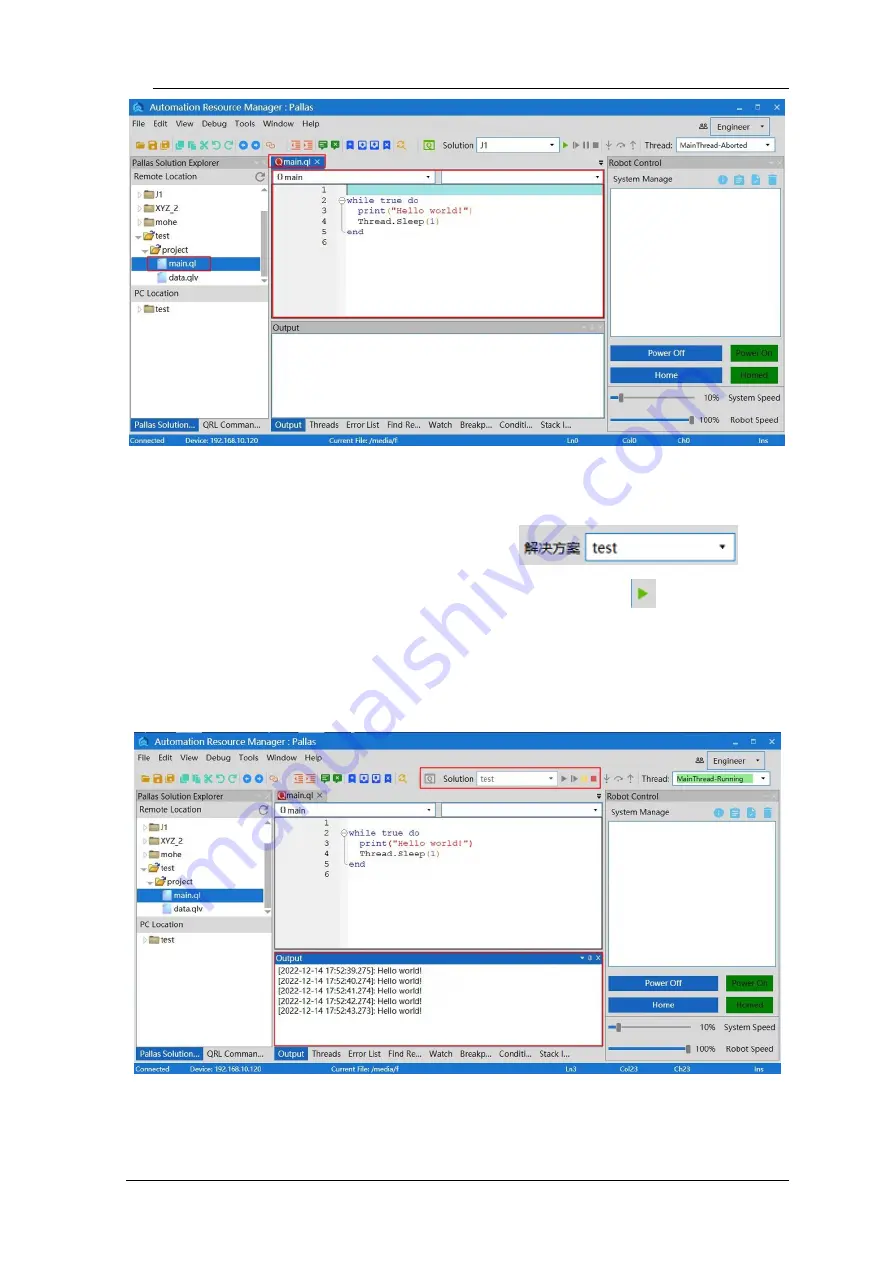
Chapter 6 Robot Operation
Document Version V1.2.0 (01/06/2023)
99
Figure 6-30 "main.ql " interface
Run the "test" solution; Select "test" in
at the
top of the ARM debugging interface and click the button
to run it. At this
point, the program will output "Hello world!" below in a circular way, as shown
in Figure 6-31.
Figure 6-31 Run the solution
Содержание AH6
Страница 1: ......
Страница 26: ......
Страница 44: ...AH6 Robot User Manual 18 Document Version V1 2 0 01 06 2023 bottom of the spline shaft...
Страница 75: ...Chapter 4 Introduction to Electrical Interfaces Document Version V1 2 0 01 06 2023 49 14 15 16 17 18 19 25 Idle...
Страница 94: ...AH6 Robot User Manual 68 Document Version V1 2 0 01 06 2023 fogging before turning on the power...
Страница 135: ...Chapter 6 Robot Operation Document Version V1 2 0 01 06 2023 109 Figure 6 46 Jog teach Figure 6 47 Teach interface...
Страница 150: ...46 Document Version V1 2 0 01 06 2023...