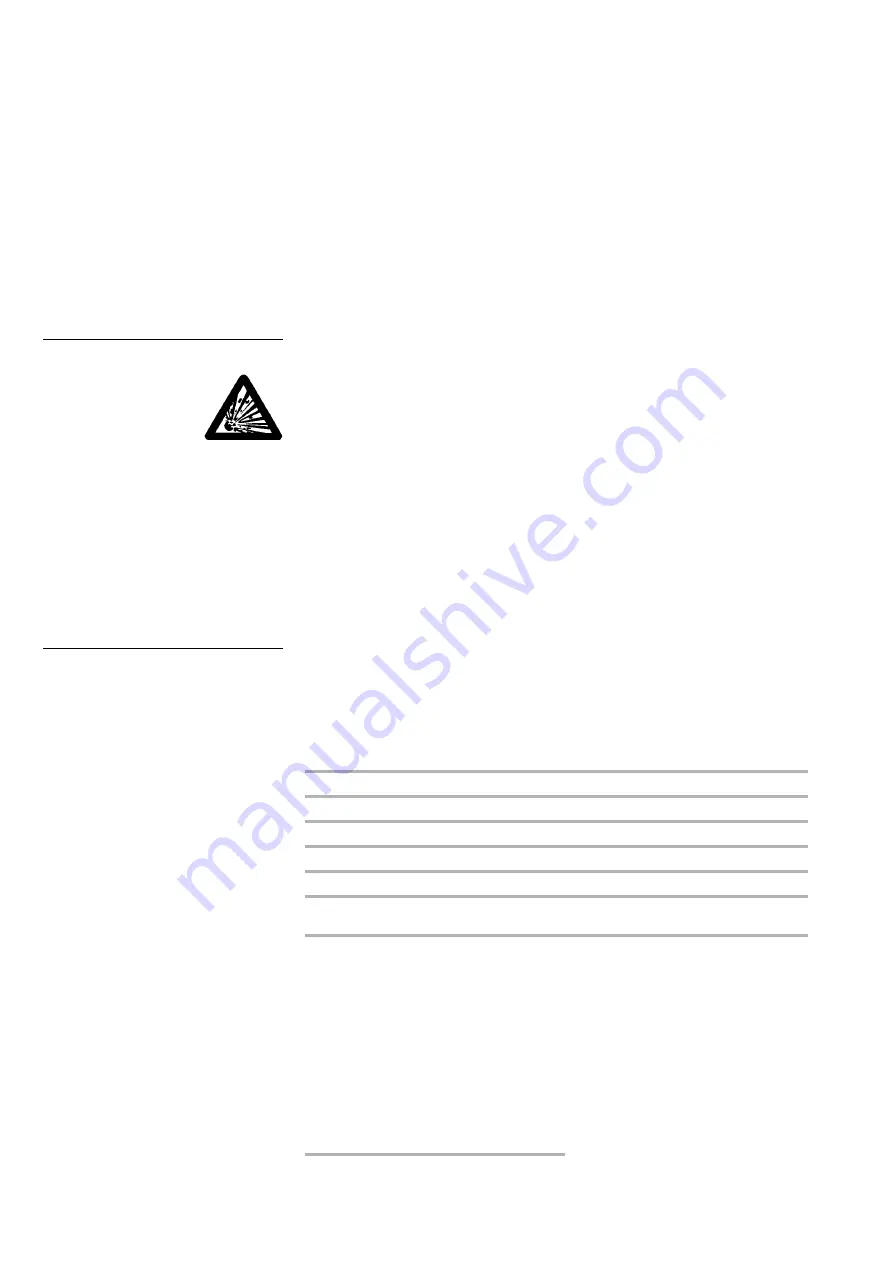
3.3
Connecting the pump to the vacuum chamber
Remove the covers and the blank flanges at the turbomolecular pump only
just before installing, to ensure that the
TURBOVAC
is installed under the clea-
nest possible conditions.
Do not stand below the
TURBOVAC
pump while it is being connected to or
detached from the system.
Turbopumps as described in the following operation manual contains a
high portion of kinetic energy due to their high rotational speed in combi-
nation with the specific rotor mass. In case of a malfunction of the system
for example rotor/stator contact or even a rotor crash the rotational ener-
gy is released.
To avoid the destruction of the equipment and to prevent injuries of the
operating staff the leading European manufacturers of vacuum pumps
strictly recommend to follow the installation instructions as given in this
manual!
The high-vacuum flange must be securely attached to the vacuum cham-
ber. If the pump were to become blocked, insufficient attachment could
cause the pump to break away from its mount or allow internal pump
parts to be discharged. Never operate the pump (in bench tests, for
instance) without its being flanged to the vacuum chamber.
If the pump should suddenly seize, the ensuing deceleration torque will have
to be absorbed by the system. To accomplish this, the following are required
when securing an ISO-K type high-vacuum flange:
Braking
Clamping
TURBOVAC
torque [Nm]
bolts
35 LS / LS2
150
4
50
63
4
151/151 C
283
4
361/361 C
580
6
600 C
1486
10
1000 C
DN 160
1500
16
DN 250
1500
10
Clamping bolts made of steel must be torqued down to 35 Nm, those of
quality 12.9 to 50 Nm.
When installing CF flanges, use only the bolts specified (tightening torque is
15 Nm for DN 40 CF, 30 Nm for DN 63 CF and larger).
You will find the order numbers for the (clamping) bolts in the Oerlikon
Oerlikon Leybold Vacuum Catalog.
The clamping bolts are
not
included as standard equipment with the pump.
Nm
15
30
35
50
ft-lb
11
22
26
37
Installation
16
GA05118_1502 - 12/2006 - © Oerlikon Leybold Vacuum
Warning