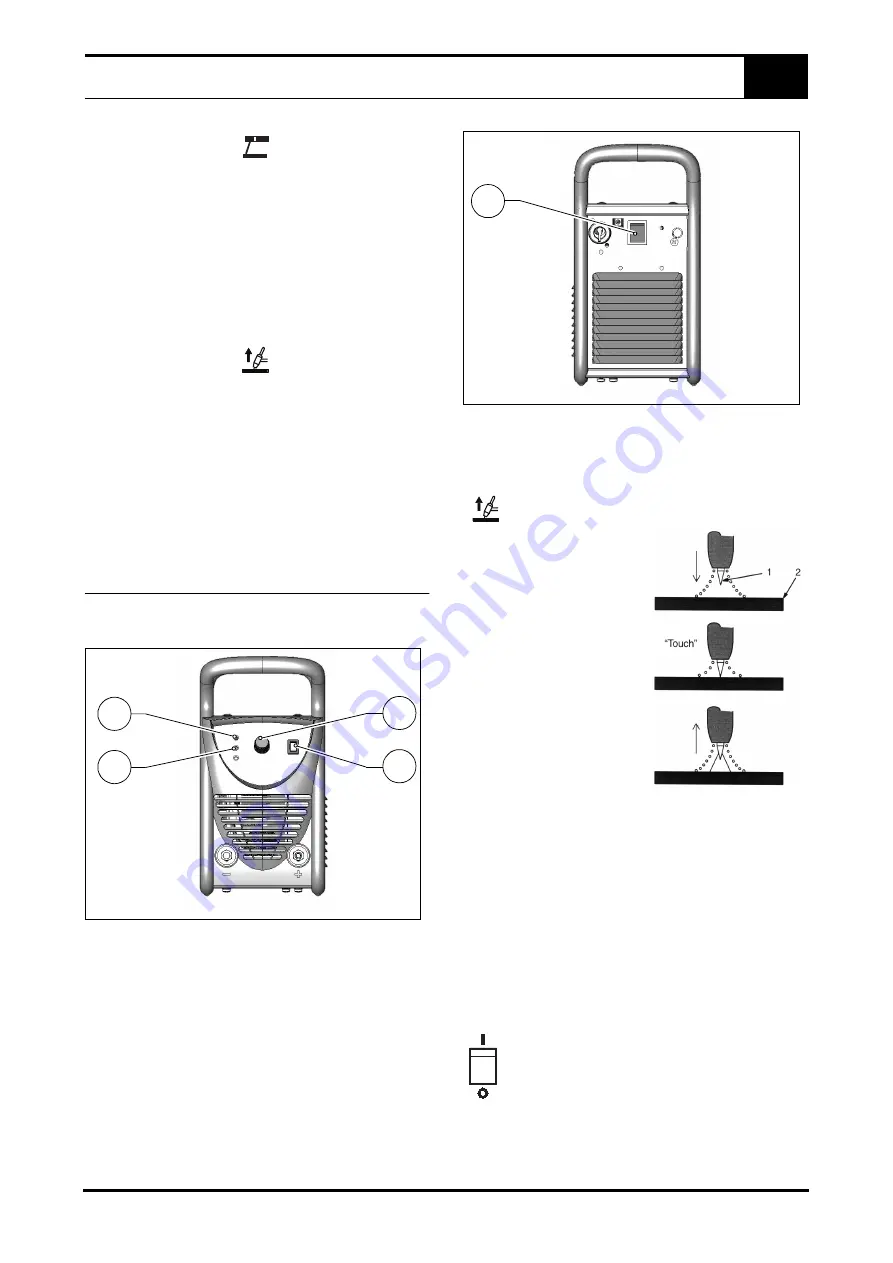
4 EN
CONTROLS
EN
5.
On the unit preset for coated electrode welding
(Rif.1 - Pic. 1 page 4.).
6.
Adjust welding current with ampere selector (Rif.3 - Pic. 1
page 4.).
7.
Turn on the power source
2.4
CONNECTION AND PREPARATION OF EQUIPMENT
FOR GAS TUNGSTEN ARC WELDING (TIG) LIFT.
• TURN OFF WELDER BEFORE MAKING CONNECTIONS.
Connect all welding accessories securely to prevent power
loss. Carefully follow safety precautions described.
1.
On the unit preset Lift TIG welding (Rif.1 - Pic. 1 page 4.).
2.
Fit the required electrode and nozzle to the electrode holder
(Check the protrusion and state of the electrode tip).
3.
Connect the ground cable quick connection to the positive (+)
receptacle and the clamp near the welding zone.
4.
Connect the torch power cable connector to the negative re-
ceptacle. (-).
5.
Connect the gas hose to the regulator located on the gas cyl-
inder.
6.
Adjust welding current with ampere selector (Rif.3 - Pic. 1
page 4.).
7.
Open the gas valve on the torch.
8.
Turn ON the power source.
3.0
CONTROLS
3.1
FRONT PANEL - REAR PANEL
Picture 1.
Picture 2.
1 - PROCESS SELECTOR
(Rif.1 - Pic. 1 page 4.) : In this position
welding can be used with rutile, basic electrodes, and specially
coated electrodes.
LIFT TIG PROCEDURE
In this position the TIG
welding process with lift mode
ignition can be selected, as de-
scribed previously.
TO IGNITE THE ARC
, when
TIG welding,proceed as fo lows:
Touch the welding piece with the
electrode; this will cause a short-
circuit between the piece (2) and
the electrode (1). Lift off the
electrode; the arc will ignite. The
integrity of the electrode tip is
guaranteed by the low ignition
current during short-circuiting
between the welding piece and
the electrode ignition is guaran-
teed even at minimum welding
current settings; the operator
can therefore work without con-
taminating the ambient with
electromagnetic disturbance,
normally caused by high frequency discharges.
The advantages can be this summarised:
a. l no need for high-frequency startups;
b. l no damage to the electrode tip during start-ups, regard-
less of ampere setting, thereby avoiding the presence of
tungsten in the welding piece, common during scratch
starting.
2 - FAULT LED (Yellow)
(Rif.2 - Pic. 1 page 4. ) : When the fault
led lights on, the overheating occurs inside the unit due to the ex-
ceeding the rated duty cycle. Happening that the welding opera-
tions have to be stopped, the welding power source has to be kept
on until the led lights off so the unit is ready to weld again.
3 - CURRENT REGULATION
(Rif.3 - Pic. 1 page 4.) : this poten-
tiometer adjust the welding current range.
4 - ON - OFF SWITCH:
This switch (Rif. 4 - Pic. 2 page
4.) has two positions:
ON= I
and
OFF = O
5 - ARC LED ILLUMINATED (Green)
(Rif.5 - Pic. 1 page 4.) : this
led lights when the machine is turn on.
5
2
3
1
4