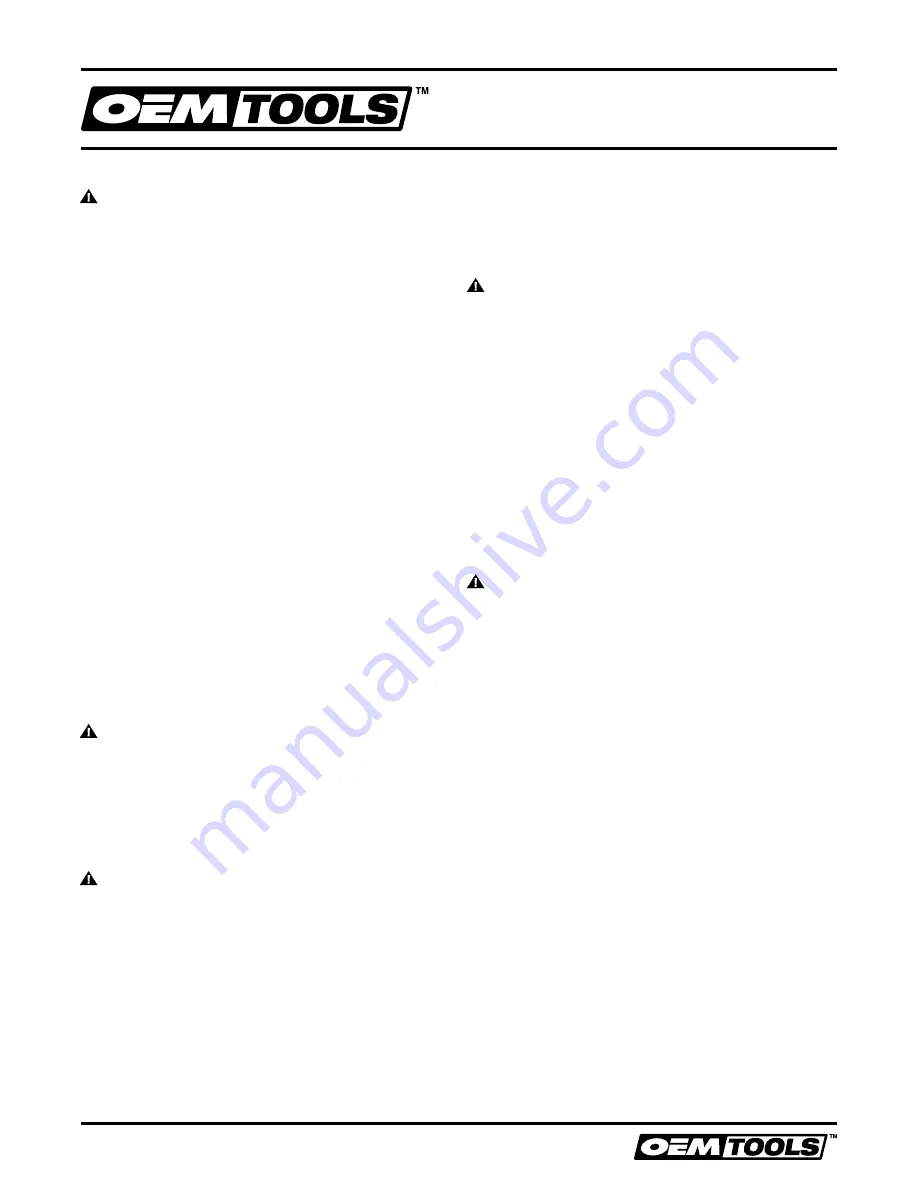
5
Operating Instructions and Parts Manual
24817
1/18
2018 OEMTOOLS
™
FLUX CORE
WELDER 110V 70A
FLUX CORE WIRE INSTALLATION INSTRUCTIONS
WARNING
:
Turn the Welder OFF and unplug prior to
installing flux core wire.
NOTE:
Designed for use with 4-inch wire spools of 0.03"
or 0.035" diameter flux core wire. Other wire spools and
wire diameters are not supported, and may cause product
malfunction or failure.
1. Open the Top Compartment of the Welding Machine.
2. Remove the Wing Nut and Spacer.
3. Slide the 4-inch Wire Spool onto the Wire Spindle and
re-install the Spacer and Wing Nut.
4. Remove the Contact Tip and Nozzle from the end of the
Welding Gun.
5. Loosen Pressure Adjuster and lift to separate the
Rocker Arm from the Drive Roller. Make certain the
Drive Roller is set to the correct flux core wire diameter
(see Drive Roller Instructions to adjust).
6. Carefully pull out and straighten about 3" of flux core
wire.
NOTE:
Apply constant tension to the wire; without
tension, the wire will unravel from the spool.
7. Cut the small curved end from the wire. Thread the wire
through the Guide Tube, across the Drive Roller and into
the Gun Line.
8. Reposition the Rocker Arm and fasten the
Pressure Adjuster.
NOTE:
DO NOT overtighten the Pressure Adjuster; this will
impede wire feeding through to the Gun Line.
9. Plug the Welder into a grounded 110V outlet, and turn
the Welder ON. Set the wire speed to LOW.
10. Press the trigger and begin feeding wire.
WARNING
:
DO NOT point the gun at yourself or others.
NOTE:
Watch the Drive Roller. If the wire slips, turn the
machine OFF, unplug the machine and tighten the
Pressure Adjuster.
11. Wire will exit the end of the Gun. RELEASE THE
TRIGGER, AND TURN THE MACHINE OFF. Re-install the
Contact Tip and Nozzle. Cut the wire about 1/4" from
the end of the Contact Tip.
WARNING
:
DO NOT attempt to weld with the Top
Compartment open. After the wire has been installed, close
the Top Compartment.
WELDER OPERATING INSTRUCTIONS
NOTE:
These instructions describe very basic welding
processes as they apply to the operation of this Welder.
There are many different types of welding machines, welds
and welding procedures that cannot be described in detail
in this instruction manual. Welding proficiently requires
practice, education and testing. DO NOT attempt to weld a
final project with welding knowledge/information provided
by this manual alone. By using this product, the operator
understands that OEMTOOLS
™
cannot be held responsible
for property damage caused by operator negligence,
ignorance or general welding mistakes.
NOTE:
After reading through this manual, it is
recommended that the operator, despite welding experience
level, practice welding scrap metal with this Welder. Welding
operation and performance will vary by model.
WARNING
:
DO NOT attempt to change the welding
current setting while operating the Welder.
1. Thoroughly read and complete Welding Machine setup,
Drive Roller Installation and Flux Core Wire Installation.
2. Connect the Ground Clamp to a clean, bare metal
surface on the workpiece.
NOTE:
Thoroughly read warnings regarding electric shock
and fire hazards prior to this step.
3. Set wire speed to the desired setting for the material
thickness. SEE TROUBLESHOOTING AND HELPFUL
TIPS SECTION.
4. Plug the Welder into a grounded 110V outlet, and
turn ON.
5. Briefly press the Trigger and begin feeding wire. Wire
will exit the end of the Gun. RELEASE THE TRIGGER, AND
TURN THE MACHINE OFF.
WARNING
:
DO NOT point the gun at yourself or others.
6. Cut the wire about 1/4" from the end of the Contact Tip.
7. Turn Welder ON.
8. Lower your ANSI Approved Welding Helmet, and
position the Welding Gun Perpendicular to the base
metal and tilt the gun to a 15-20° angle (based on
application and operator preference).
9. Move the Contact Tip toward the workpiece to initiate
the arc, approximately 1/4"-3/8". Press the Trigger to
start feeding wire through the gun.
10. A molten “puddle” will begin to form, referred to as
the weld bead. This bead will follow the motion of the
Welding Gun. SEE TROUBLESHOOTING AND HELPFUL
TIPS SECTION.
11. Release the Trigger to stop the weld.
12. When finished, turn the Welder OFF and unplug.
DUTY CYCLE
To avoid damage and personal injury, DO NOT weld for
longer than the prescribed Duty Cycle Time. This Welder
has a 20% Duty Cycle Time at 70A based on a 10 second
time period. This indicates that this Welder can weld for
2 seconds out of every 10 second time period. Failure to
comply may lead to product failure.
HELPFUL TIPS
1. Thoroughly clean surfaces prior to welding. Brush or
sand off all paint, adhesive and oxidation.
2. Weld at a constant pace. Abrupt motions or speed
changes will change the weld quality and depth.