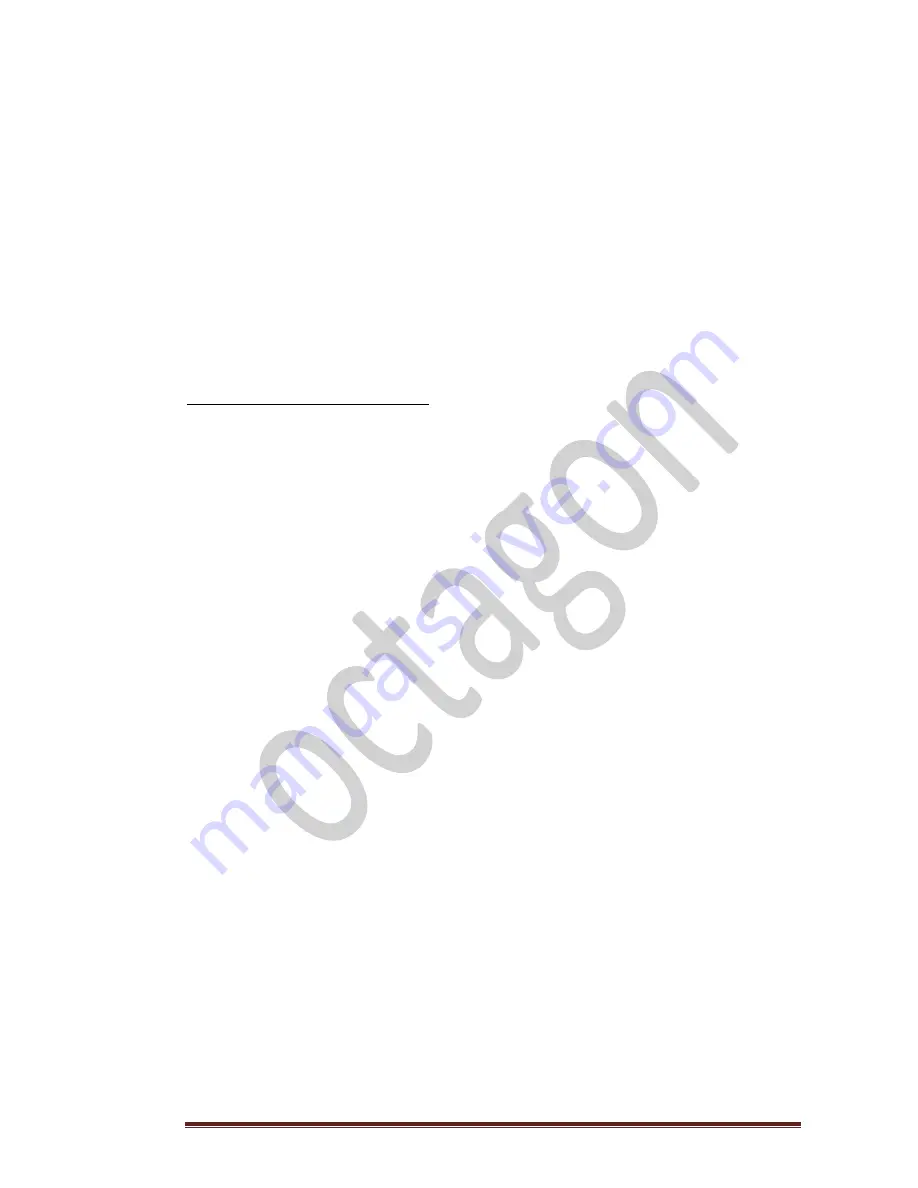
octagon v2.16
Page 8
The innovation of Octagon pellet burner bio lies with two crucial elements relating to
combustion:
a.
The operation of the burner is totally proportional, within the predefined parameters,
subject to automatic adjustment of the level of power (self adjustment). In this way the
pellet burner will provide always the power required by the system and will achieve the
maximum possible fuel economy
And,
b.
The pellet burner will control the burning process by the constant and excellent control
of the boiler’s backpressure and the chimney draft. The control of the fan ensures not
only the extraction of the exhaust gas but mainly minimizes the possibility of “backfire”
from the supply pipe.
Gradual reduction of combustion level
As soon as the burner achieves the predefined water temperature it will automatically reduce its
power so as to remain functional within the set temperature range and below the upper safety
limit. At this point the burner operates with the necessary, minimum power meeting the
required thermal need.
END OF BURNING
The smooth termination of burning is achieved by ensuring the complete burning of any
remaining fuel in the combustion chamber. This is achieved by continuous monitoring of the
flame through the flame sensor which drives the fan that will continue to work in order to burn
all residual pellets in the flame tube.
Thereafter, the fan continues at maximum speed for a period of time so as to clean the burning
chamber from the ashes and preparing it for the next fire up.
Содержание bio 3
Страница 1: ...octagon v2 16 Page 1 OCTAGON USER GUIDE Pellet Burner Series Octagon Model bio 3 Fbio 3 3 ...
Страница 2: ...octagon v2 16 Page 2 ...
Страница 4: ...octagon v2 16 Page 4 ...
Страница 40: ...octagon v2 16 Page 40 ...
Страница 42: ...octagon v2 16 Page 42 ...
Страница 43: ...octagon v2 16 Page 43 22 MAINTENANCE LOG SECTION DATE NAME OF TECHNICIAN REMARKS SIGNATURE 1st 2nd 3rd 4th 5th ...