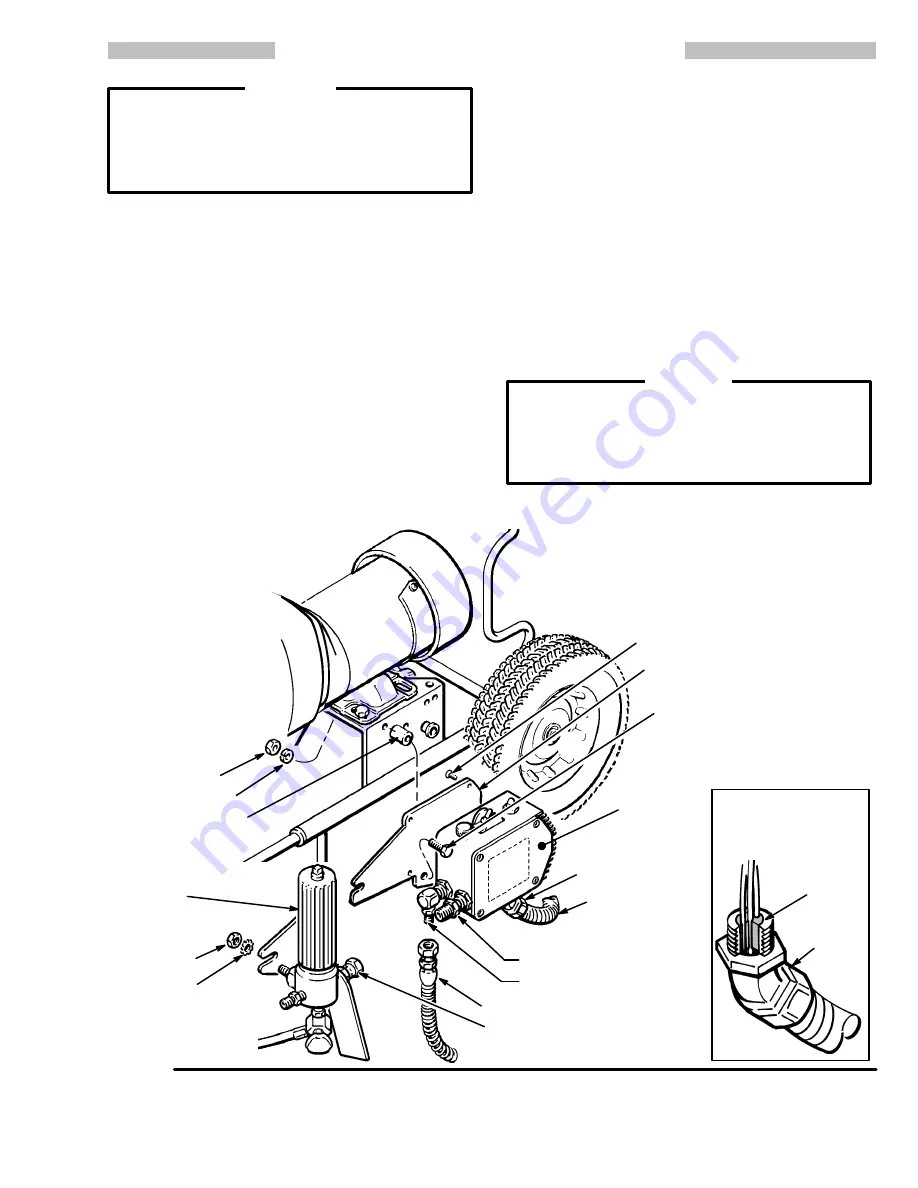
27
PRESSURE CONTROL REPLACEMENT
Before doing this procedure, follow the
Pressure
Relief Procedure Warning
on page 22 to reduce
the risk of a fluid injection injury , splashing in the
eyes or on the skin, injury from moving parts, or
electric shock.
Unplug the sprayer!
WARNING
Refer to Fig 27–1 except where noted.
1. Disconnect the main fluid hose and the secondary
fluid hose, if used. Disconnect the fluid hose (26) at
the displacement pump nipple and the pressure con-
trol nipple (344).
2. Loosen the filter bracket nut (22).
3. Hold the hex of the pressure control adapter (341)
firmly with a 3/4” open end wrench. Use an adjustable
wrench to unscrew the swivel union (30), and then re-
move the fluid filter (62).
4. Remove the pressure control cover (17). Disconnect
the four motor leads. Refer to Fig 26–2.
5. Remove the circuit board and retain it. Refer to page
26.
6. Remove the conduit (13f).
7. Remove the three screws (28) and lockwashers (39)
and nuts (40) located below the pressure control. Re-
move the pressure control.
8. Remove the screws (16) holding the back mounting
bracket (70) to the pressure control.
9. Install the new pressure control assembly in the re-
verse order of disassembly. Reinstall the conduit seal
(21) around the wires in the conduit connector (345)
to prevent motor contamination from entering the
control. See the DETAIL below.
10. Perform the
PRESSURE CONTROL ADJUST-
MENT,
page 28, before regular operation of the
sprayer.
CAUTION
Do not allow the adapter (341) to turn while installing
the new pressure control assembly . Turning it can
damage the sensitive bourdon tube. Hold the
adapter firmly with a 3/4” open end wrench while
screwing in the swivel union (30).
341
Fig 27–1
26
22
6
40
344
345
CAUTION
Do not allow the adapter
(341) to turn at any time.
DETAIL
Shows position of conduit
seal (21) in conduit con-
nector (345)
21
345
11
39
16
70
28
30
17
13f
62