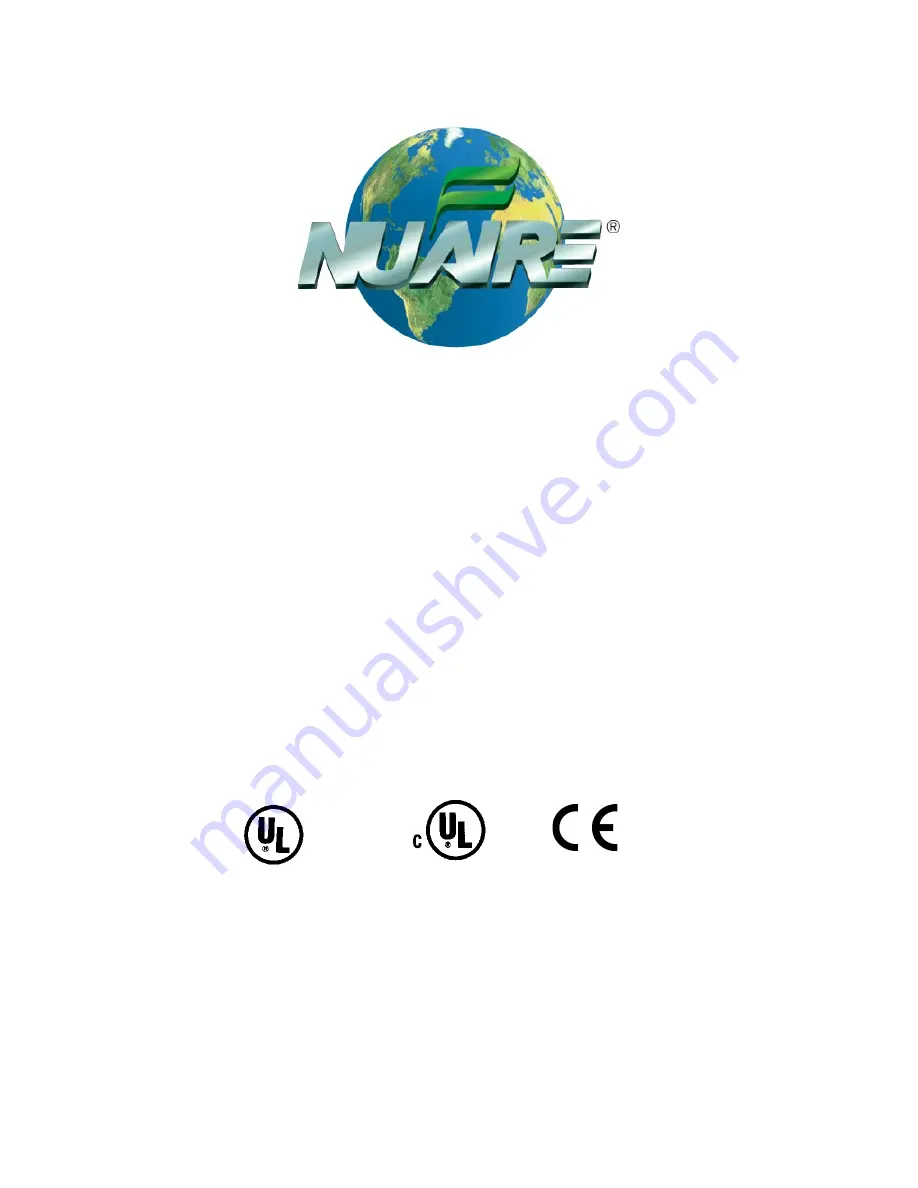
OM0246
Page 1 of 64
Rev 5 June/2020
Air-Jacketed Automatic CO
2
Incubator
Models
NU-5810, NU-5820, NU-5831, NU-5841
NU-5810E NU-5820E, NU-5831E, NU-5841E
Operation and Maintenance Manual
June 2020
Revision 5
Series 12
For 115 Vac, 50/60 Hz Only
Manufactured By:
NuAire, Inc.
2100 Fernbrook Lane
Plymouth, MN 55447
Toll-Free: 1-800-328-3352
In Minnesota: (763)-553-1270
Fax: (763)-553-0459
Содержание NU-5810
Страница 9: ...OM0246 Page 9 of 64 Rev 5 June 2020 ...
Страница 13: ...OM0246 Page 13 of 64 Rev 5 June 2020 ...
Страница 26: ...OM0246 Page 26 of 64 Rev 5 June 2020 8 7 Run Mode Operator Interactions ...
Страница 58: ...OM0246 Page 58 of 64 Rev 5 June 2020 ...
Страница 59: ...OM0246 Page 59 of 64 Rev 5 June 2020 ...
Страница 60: ...OM0246 Page 60 of 64 Rev 5 June 2020 ...
Страница 61: ...OM0246 Page 61 of 64 Rev 5 June 2020 ...
Страница 62: ...OM0246 Page 62 of 64 Rev 5 June 2020 ...
Страница 63: ...OM0246 Page 63 of 64 Rev 5 June 2020 ...
Страница 64: ...OM0246 Page 64 of 64 Rev 5 June 2020 ...