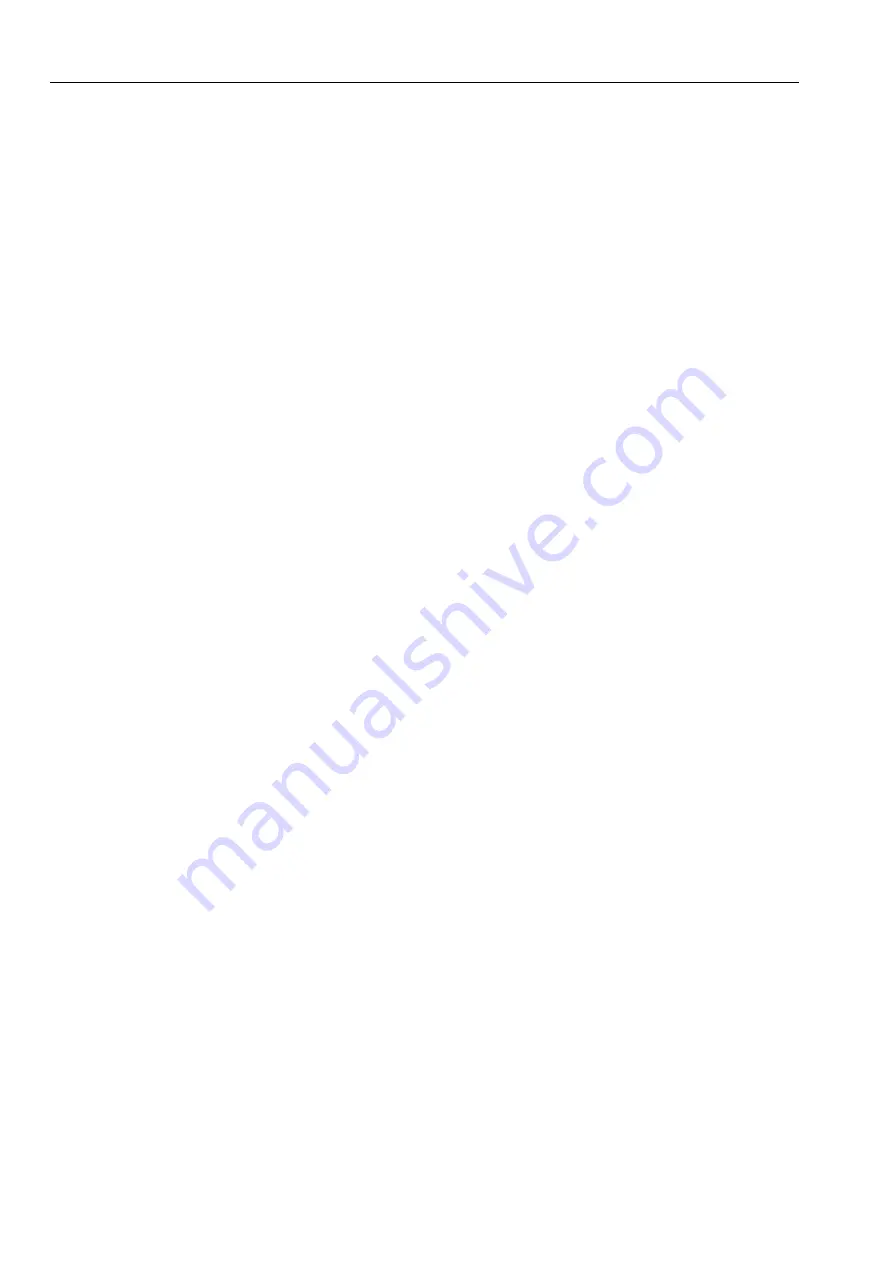
Routine Maintenance
Isolation
Before commencing, make sure that the Airmover and
speed control, if fitted, are externally isolated from the
electrical supply.
Maintenance periods
The first maintenance should be carried out three months
after the commissioning and thereafter at twelve monthly
intervals. These intervals may have to be shortened, how-
ever, if the unit is operating in adverse environmental
conditions or handling heavily polluted air.
General cleaning and inspection
Clean the exterior of the unit, silencers, flexible connec-
tors, resilient mountings, etc., as fitted. Inspect for
security and condition. Check tightness of fixing devices.
Remove the unit access panel. Inspect internal
components for security and condition. Check that the
impeller rotates freely. Clean components as necessary
(for cleaning the impeller see below).
Cleaning the Impeller
A build-up of dust may be removed by carefully brushing
with a stiff brush. Take care not to damage or distort
impeller blades nor to disturb balance weights. If the
impeller is too badly fouled to allow adequate cleaning in
situ, it should be removed via the access panel. (See p.7).
Alternatively, remove the complete unit/silencer combina-
tion from the installation. When removed, clean the
impeller as follows:
(a) If a silencer is fitted to the impeller side of the unit,
remove it. Alternatively remove the impeller from the
unit as described on this page .
b) Sponge the impeller with warm soapy water and leave
to soak. Do not use caustic fluids under any circum-
stances. When applying water, take care to prevent it
getting onto or into the electrical parts.
c) After soaking, rinse with fresh water and thoroughly
dry.
(d) If applicable, refit the silencer to the unit, with a gasket
sandwiched between the joint faces. Refit the unit or
unit/silencer combination back into the installation, again
sandwiching a gasket between joint faces.
(e) If the impeller has been removed it should be refitted
as described on page 10.
Lubrication
Most motors have sealed-for-life bearings and therefore
need no lubrication.
Testing
Refit the unit access panel. Test run the unit. Check that
the speed control, if fitted, regulates speed as required.
Replacement of Parts
Isolation
BEFORE COMMENCING, MAKE SURE THAT THE
AIRMOVER IS EXTERNALLY ISOLATED FROM
THE ELECTRICAL SUPPLY
Parts
For the ordering of spare and replacement parts see the
SCHEDULE OF PARTS on page 8. Before fitting,
remove any protective coating from replacement parts.
Isolator or Capacitor
Replacement is self evident after the removal of the unit
access panel. When disconnecting leads make a note of
connections. Make sure the new component is wired in
the same way.
Motor or Impeller
The access panel allows inspection of the motor and
impeller in the duct. If any components are to be replaced
or serviced the unit must be removed from the
installation using suitable hoists for the larger sizes.
To remove the motor proceed as follows:
Disconnect the unit electrically and remove it from the
duct before commencing work.
(a) Remove the access panel and locate the terminal box
fitted to the motor, remove its cover and disconnect the
leads. Disconnect the flexible conduit at the motor end
and move leads and conduit clear. Note: To facilitate
replacement note the position of all leads tag if necessary
(b) Size 315. Remove the access panel. Release the trans-
verse motor mounting plate by unscrewing from the case
side. Move back until the impeller clears the venturi.
Release the impeller from the motor shaft (see below) and
remove
(c) All other units. Remove the access panel, release the
motor/impeller assembly from the motor support. Move
the whole assembly back (away from the venturi) to allow
access to the front of the impeller.
To assist replacement, measure and note the
amount by which the end of the motor shaft either
protrudes from or is recessed into the bore of the
impeller.
Remove the impeller as detailed below.
Axial Flow Impellers
Impellers on these units are retained by a spigot type
fitting. To remove, unscrew the fixing bolt and withdraw
impeller from shaft. In stubborn cases place suitable levers
between the back of the spigot and the motor case. Lever
off the impeller using the minimum force necessary.
If, however, the motor is to be changed, first remove the
impeller as already described then remove the motor and
motor plate assembly through the access aperture. Note.
On unit size 315 it will be necessary to first remove the
motor from the plate.
Installation and Maintenance
AIRMOVER DSA AXIAL UNITS
8
Содержание AIRMOVER DSA Series
Страница 15: ...15...