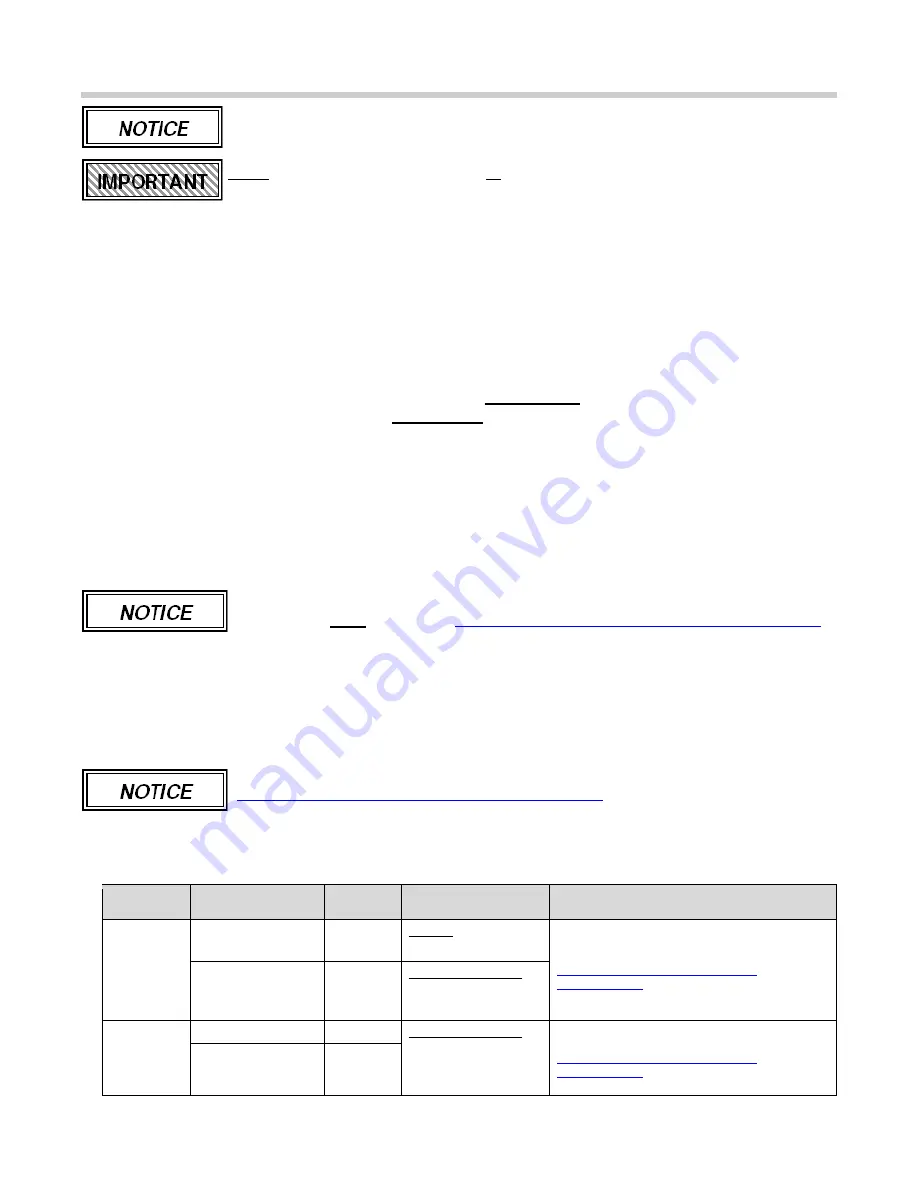
11.0
WARRANTY
A licensed and trained Heating Technician must install this appliance, otherwise the
Warranty is VOID.
FREE extended coverage option only IF you register your boiler and installation with NY
Thermal Inc. within 6 months of installation.
What Is Covered
We, the manufacturer, warrant that any parts or components of each new Boiler or Water Heater, will be supplied
free of defects in material or workmanship. This warranty replaces any other warranty implied or expressed. All
the durations, terms and conditions mentioned hereafter are for manufacturer defects due to material or
workmanship only, and do not include misuse or normal wear of the equipment. Equipment returned for
warranty consideration, will be evaluated upon the condition of the part when examined by NY Thermal Inc. or
an authorized service representative. Improper handling and/or installation practices may VOID the warranty.
See silver rating plate label on unit exterior for appliance type, model number, and serial number information.
To qualify for ANY warranty coverage, the installation
must comply
with the installation and operating
instructions provided with the appliance, and
must comply
with the “Terms and Conditions” of this warranty.
Labor is not covered by this warranty. All warranty coverage is offered to the original owner and location only,
and is not transferable
BASIC COVERAGE:
We will repair or replace any defective component supplied or manufactured by NTI for a period of one year (5
years for the pressure vessel), beginning from the date of installation without, however, covering the installation
itself.
Basic Coverage warranty period will commence from the date of manufacture, if the
installation is
NOT
www.ntiboilers.com/products/product-registration.html
within 6 months of installation.
EXTENDED COVERAGE:
We will repair or replace a defective pressure vessel for a period of eleven (11) years, at 100% coverage,
beginning from the date of installation without, however, covering the installation itself. After the 11
th
year, the
pressure vessel warranty coverage is prorated from 90% coverage in year 12, to 10% coverage in year 20.
To qualify for Extended Coverage, the installation must be registered at
www.ntiboilers.com/products/product-registration.html
within 6 months of installation.
By registering your installation, you authorize NTI to contact you directly in the event of
any product advisories associated with your NTI boiler or water heater.
COVERAGE SUMMARY:
Coverage
Coverage Period
Coverage
Rate
Components Covered
Additional Terms and Conditions
BASIC
Year 1
100%
All parts (including
Pressure Vessel)
Coverage Period commences on the date of
installation when the boiler installation is
registered at
www.ntiboilers.com/products/product-
registration.html
within six months of installation,
otherwise the Coverage Period commences from
the date of manufacture.
Years 2 through 5
100%
Pressure Vessel only
EXTENDED
Years 6 through 11
100%
Pressure Vessel only
Not applicable to Tankless Coil.
Installation must be registered at
www.ntiboilers.com/products/product-
registration.html
within six months of installation
to qualify for Extended Coverage.
Years 12 through 20
100-10%