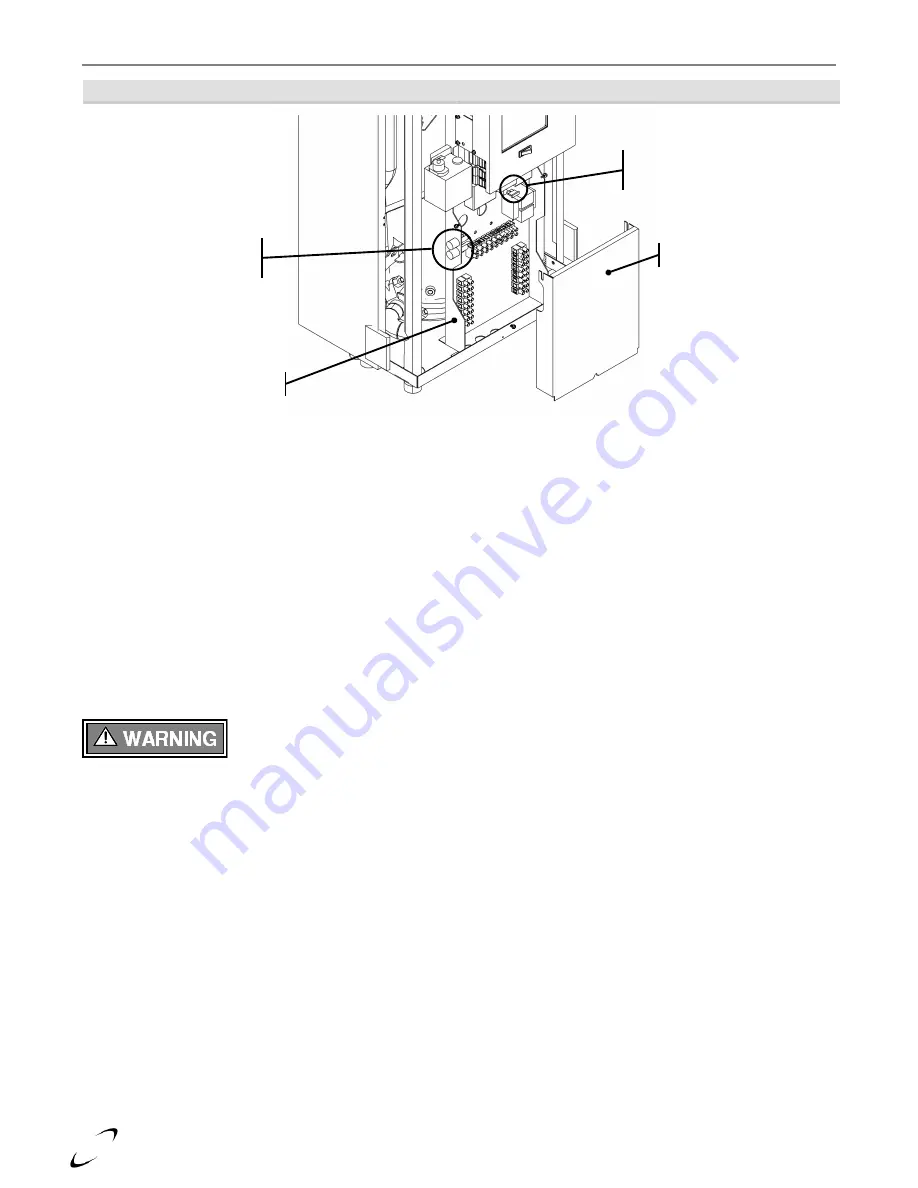
Trinity
│
Installation and Operation Instructions
Tft Series
64
Figure 16-1 Tft Control Panel
Figure 14-1 Tft Model
Fuses
The Trinity Tft is equipped with three (3) fuses. Check these fuses before replacing the controller or any other
electrical component; if the fuse is blown, it will prevent the protected device(s) from functioning.
To check, and if necessary replace, the fuses:
Remove all 120VAC power from the appliance. Be careful to check that the unit is not powered from more
than one source e.g. a UPS (uninterruptible power supply).
Remove the front cover.
Fuses "A" and "B" are accessible by removing the spring-loaded knurled knob of their respective holders.
Push the knob toward the panel, and twist approximately 1/4 turn counter-clockwise.
Fuse "C" is an auto blade type and is installed in an “inline” fuse holder; gain access by removing the
control panel cover.
After inspecting and if necessary replacing fuses, replace the panel cover and front cover. Restore power to the
appliance and confirm proper operation.
Only replace fuses with identical parts, see Figure 16-1. Failure to follow this warning
may result in component failure, fire, property damage, serious injury or death.
User Interface (Touch-screen Display)
A blank screen does not necessarily indicate a problem; the display may be configured to automatically blank the
screen after a pre-set interval. Simply touch the screen to activate it. Confirm that 120VAC is being supplied to
the appliance and that the service switch located below the display is turned ON (1). If the screen does not
become active, perform the following procedure:
Blank Screen
1.
Remove the front cover from the boiler.
2.
Remove the control panel cover and check Fuse “C” (Auto Blade Type); if faulty check for shorts in the
thermostat wiring, correct, then replace fuse (see Figure 16-1).
3.
Ensure the “2 by 2” Molex connector, located behind the display at the top, is connected and that the wires
are fully inserted (see Figures 16-2 and 16-3). Verify that 24VAC is present between the Blue and Red
wires; if not trace wiring back to 24VAC transformer; correct wiring and/or replace transformer (see Figure
13-1).
4.
Remove the display assembly from the control panel and check the 24VAC wiring connection on the back of
the display; Blue to terminal 7 [24VAC (COM)], Red to terminal 8 [24VAC] (see Figure 16-3).
Fuse “C” ATO 2A
32V Auto Blade Type
Fuses “A” and “B” 3AG
7A 250 Fast-Acting
Control Panel Cover
Control Panel