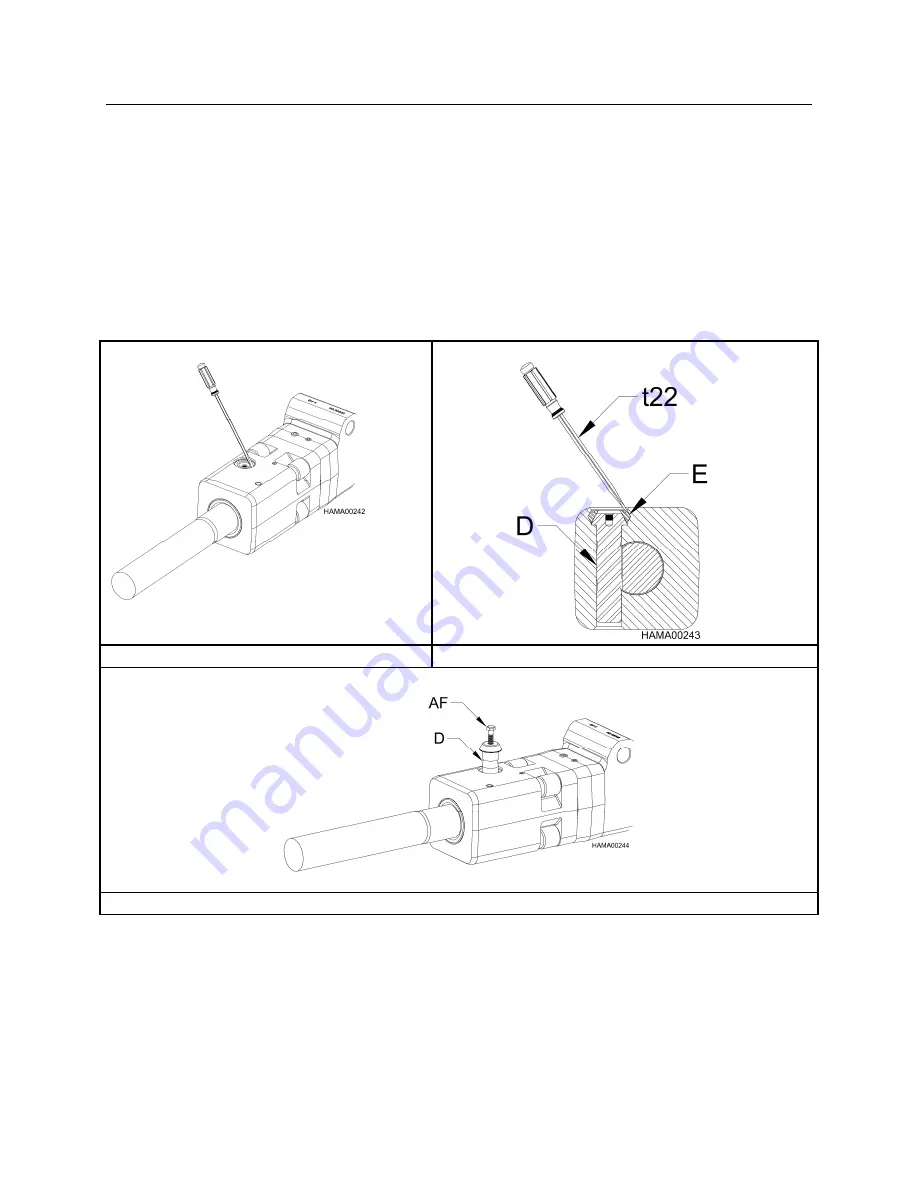
-
20
-
CHANGING THE TOOL
REMOVAL
1. Remove the retaining pin ring (E) by using a screwdriver (t22), see Figures 1 and
2. It will easily come out if pulled at an angle as shown in Figure 2.
2. Screw an M12 bolt (AF) or cap screw into the retaining pin (D), as shown in Figure 3.
1. Pull out retaining pin (D). If the retaining pin (D) is jammed, use a hammer
and drift from the opposite side.
Figure 1
Figure 2
Figure 3