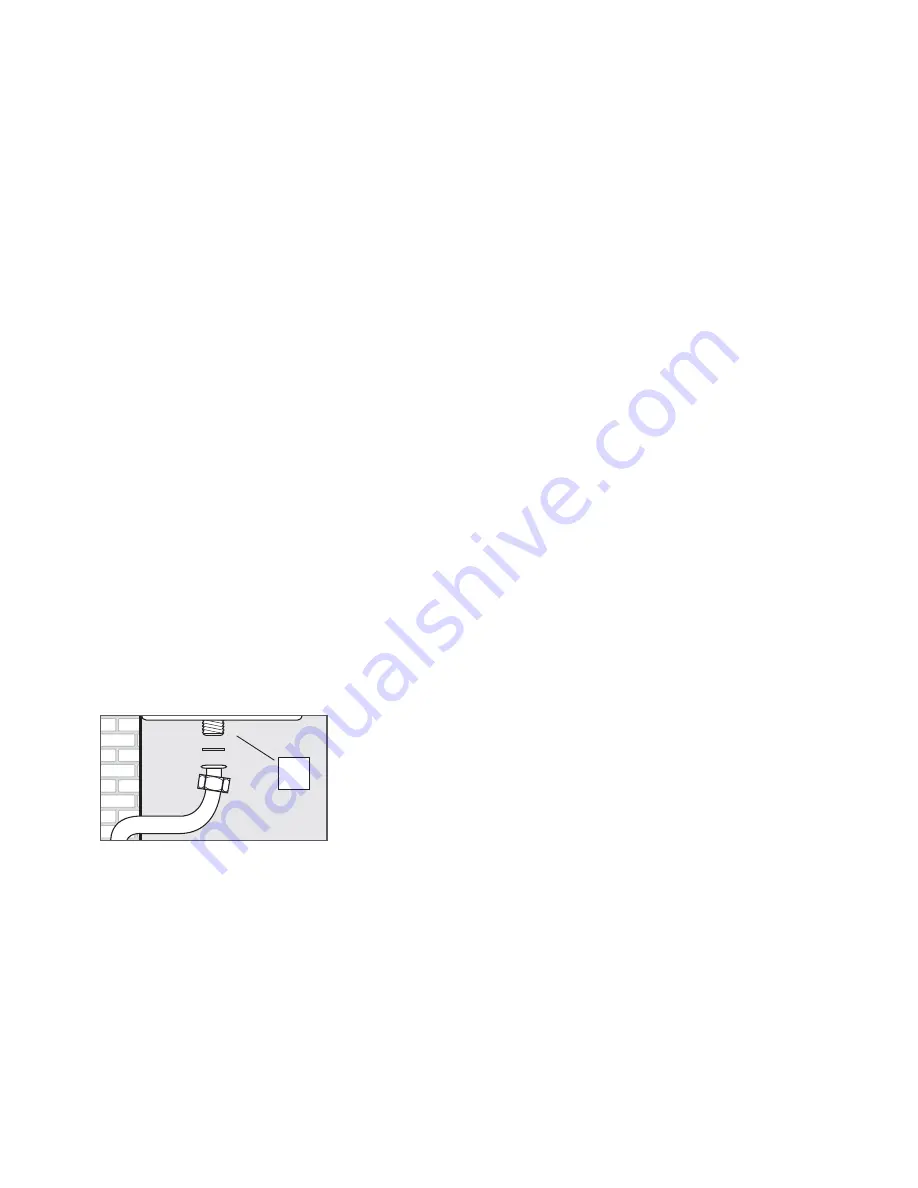
24
3.2.11 Gas mains connection
Gas supply pipe cross-section
must be equal or greater than boiler
gas pipe. Cross-section gas pipe
size calculation depends on len-
gth, layout pattern, gas flow rate.
Gas pipe size is to be dimensioned
accordingly.
Comply with installation standards
enforced in the installation country.
They are considered as an integral
part of this booklet.
Remember that before operating an
internal gas distribution system and
before connecting it to a metre, it
must be checked for leaks.
If any part of the gas system is inac-
cessible, leak test must be carried
out before pipes are covered.
Leak test must not be carried out
using flammable gas. Use air or
nitrogen for this purpose.
When boiler supply gas is already
in the pipes, leak check by a naked
flame is forbidden. Use specific pro-
ducts available on the market.
IT IS MANDATORY
when connec-
ting boiler to gas supply network, to
use an appropriately sized and made
gasket (A).
The boiler gas inlet thread configura-
tion is not appropriate for hemp, pla-
stic tape or similarly made gaskets.
3.2.12 Power mains connection
The boiler is supplied with a three-
poled power cable, already con-
nected to the electronic board and
it is provided with an anti-rupture
firming clamp.
This boiler must be connected to a
230V-50Hz electrical power supply.
When connecting the boiler to
power mains, respect phase / neu-
tral polarity sequence.
Installation standards must be com-
plied with and are considered an
integral part of this manual.
An easy accessible two-poled switch
must be installed outside the boi-
ler. The switch minimum distance
between contacts is 3 mm. The switch
must allow power supply interruption
in order to safely perform maintenan-
ce and service.
Power supply to the boiler must be
fitted with a differential magnetic-
thermal automatic switch of appro-
priate shut-down capacity.
Electrical power supply must be
appropriately earthed.
The above mentioned safety measu-
re must be verified. If in doubt, ask
a qualified technician to thoroughly
check the power network.
MANUFACTURER shall not be held
responsible for any damage due to
failure in grounding the system.
Gas, hydraulic, or CH system pipes
are not suitable for grounding power
networks.
3.2.13 Room thermostat connec-
tion
The boiler can be connected to a
room thermostat.
Room thermostat contacts must
be properly sized in conside-
ration of a 5 mA load at 24 Vdc
load.
The room thermostat wiring must be
connected to M10 terminal shown
in pic. 21, after removing the jumper
supplied as a standard fitting to the
boiler.
The room thermostat wiring must
NOT be grouped together with
power mains supply cables.
3.2.14 External temperature probe
connection
The boiler can be connected to an
external temperature probe to adjust
CH temperature in relation to outside
temperature, thereby reducing boiler
consumption (see § 1.2.3).
External temperature probe (cha-
racteristics: 10 kOhm, B3977) con-
nection to the boiler must be perfor-
med by means of a double insulated
wire, its min. cross-section must be
0.35 sq.mm
External temperature probe wiring
must be connected to M9 terminal
shown in pic. 21.
External temperature probe wiring
must NOT be grouped together
with power mains supply cables.
External temperature probe must
be installed on north/north-east
building wall. Do not install in win-
dow area, next to ventilation ope-
ning. Install probe far from a heat
source.
Always install MANUFACTURER-
approved external probe for best
performace.
3.2.15 Plumbing connections
Prior to installing the boiler, the
hydraulic system has to be cleaned
in order to remove impurities; they
could be present in system compo-
nents and damage the pump and the
heat exchanger.
CENTRAL HEATING
CH flow and CH return pipes must be
connected to the relevant 3/4” cou-
pling on the boiler (see pic. 9).
When calculating CH system pipe
size, bear in mind load losses cau-
sed by radiators, thermostatic valves,
radiator gate valves, and the configu-
ration of the system itself.
It is advisable to convey the dischar-
ge flow of boiler safety valve to the
sewer system.
Should the above precaution not be
implemented and the safety valve be
activated, boiler room flooding may
occur.
The MANUFACTURER shall not be
held responsible for any damage
resulting from failure in observing the
above mentioned technical precau-
tion.
DOMESTIC HOT WATER
DHW flow and water mains inlet pipes
must be connected to the relevant
1/2” couplings on the boiler (see pic.
9).
Hardness of water supplied to the
boiler may increase heat exchanger
cleaning frequency.
WARNING
Depending on hardness level of the
water supplied, it might be neces-
sary installing a suitable water
treatment device for domestic use
and in compliance with applicable
laws and standards.
Water treatment is always advi-
sable when water supplied to the
boiler is more than 20°F hard.
WARNING
Water treated by commonly marke-
ted water softeners, due to pH level
induced in water, may not be com-
patible with some components in
system.
A