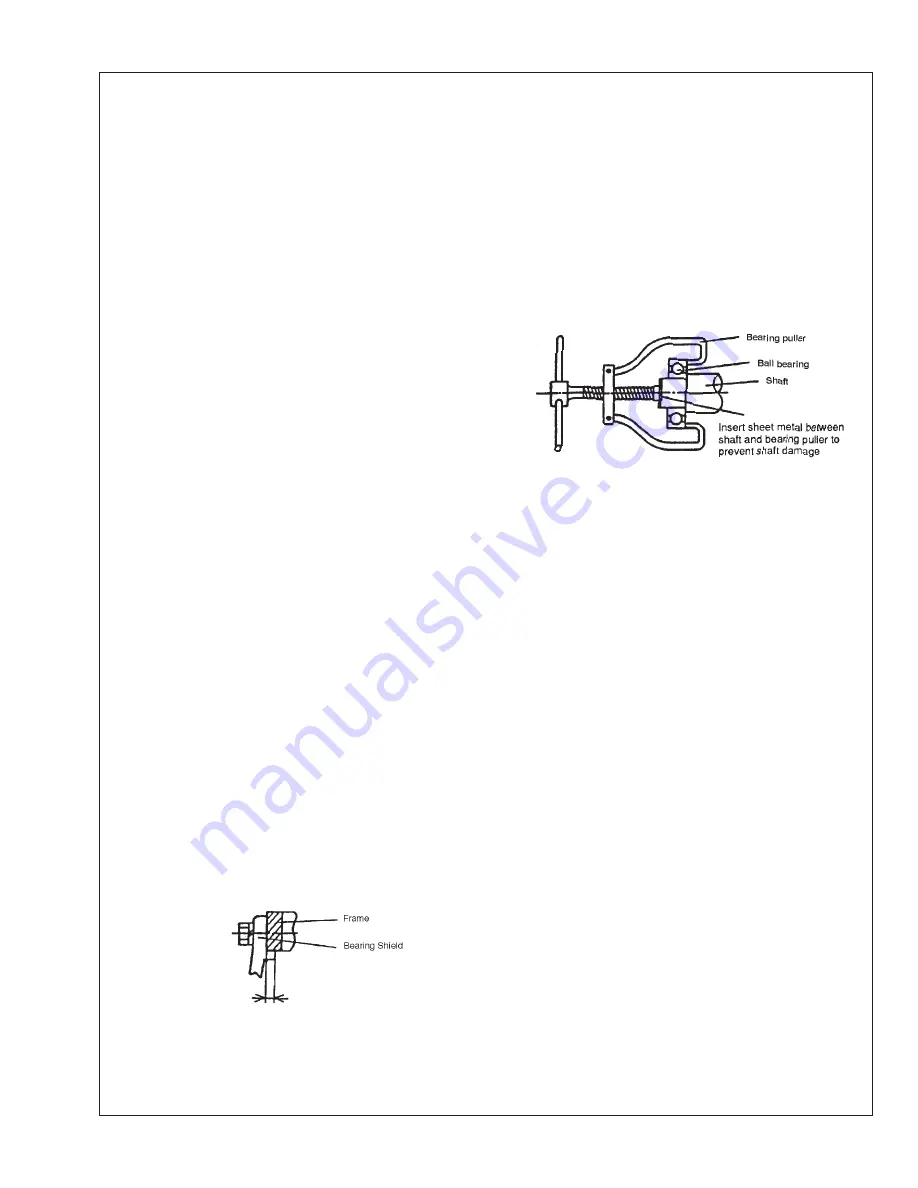
OPX300K2 05/12
11
Maintenance
BEARING INSPECTION
For bearing inspection, make sure that there is no
abnormal sound during normal running and no over-
heating. Greasing is not necessary for generators using the
double seal type ball bearings, but these will need to be
replaced after every 10,000 hours of operation (see
PARTS
REPLACEMENT METHOD
).
INSULATION RESISTANCE MEASUREMENT
If the generator has not been used for a long time, check
the insulation resistance of each lead wire at 500V with a
megger.
It is usually enough to check only the stator winding. In
order to prevent damage to the AVR, disconnect it. If the
measured insulation resis tance value is above 2 M ohms,
there is no problem, but if it is lower than that, check to
see if the inside of the generator is wet or dirty. If dust has
accumulated, blow it out with dry compressed air. Wipe
off oil stains with a cloth. If the generator is damp, dry it
and re-check.
ROTATING RECTIFIER ASSEMBLY
The rotating rectifi er assembly needs little attention.
Clean off dust and oil stains periodically. In the unlikely
event that it becomes necessary to replace the diode ele-
ments and surge absorber elements. Refer to
PARTS
REPLACEMENT METHOD
.
PARTS REPLACEMENT METHOD
1.
Bearing
Replacement:
a. In order to replace the bearing, fi rst remove the
bearing holder housing on the end of the
generator. Loosen and remove the four housing
bolts. Remove the bearing holder gently since
there is a risk that the rotor could fall and damage
the exciter rotor or the exciter stator.
Figure 6. Pilot Length
b. Using a bearing puller, extract bearing from
shaft.
c. When installing a new bearing, place a steel pipe
on the inner race surface, and fi t the bearing by
tapping it lightly with a hammer.
Figure 7. Bearing Puller
Note:
Absolutely do not apply pressure to outer race
of the bearing during insertion.