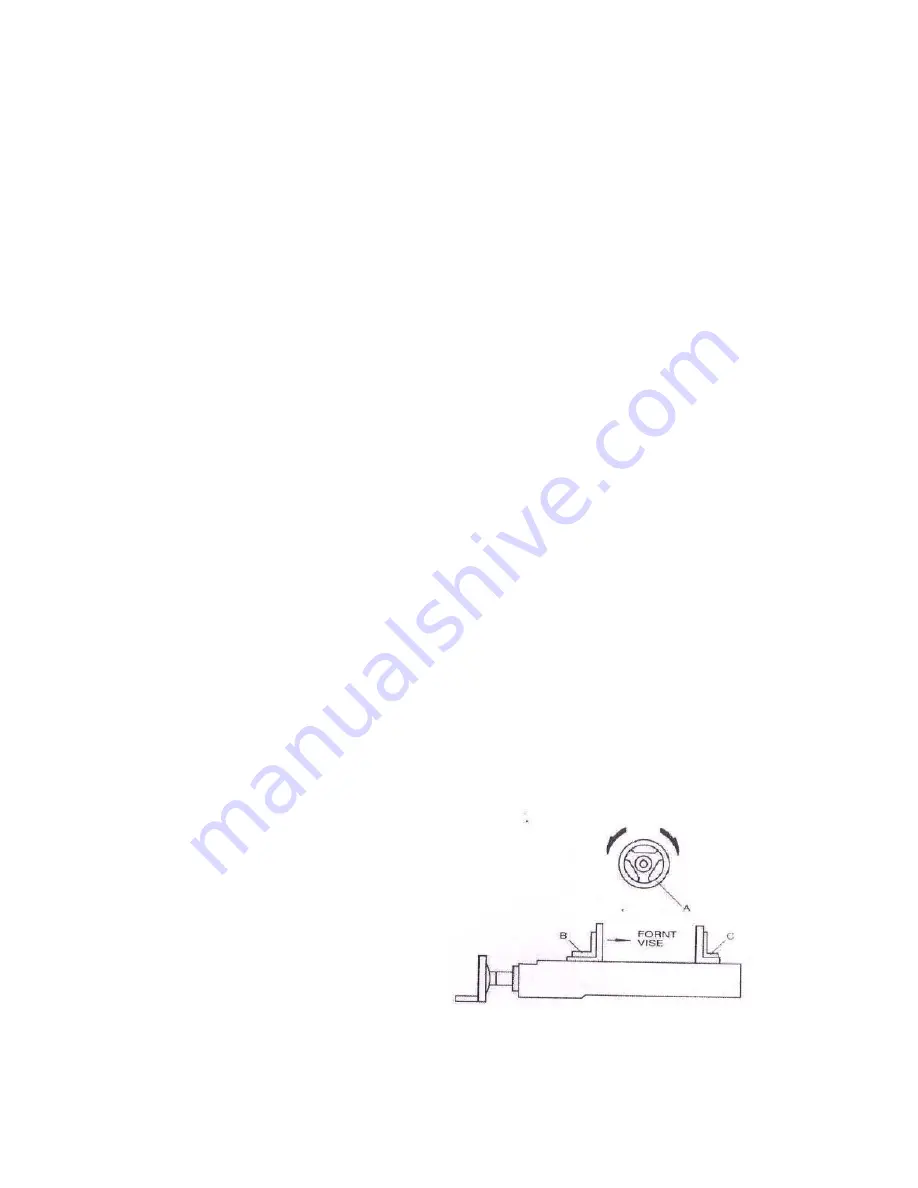
1. Bi-metal band saw blade is suitable for metal workpiece such as carbon steel, alloy steel, and
stainless steel.
ces and hard
3.
n band saw blades are suitable for wood, fiber glass and plastic.
4. Carbide grit edge band saw blades are suit
ago, carbon product and alveolate
material, etc.
vertical position and open the blade guards. Loosen tension screw knob to
he new blade with teeth slanting toward
pulley (bottom) with the left hand and hold in position.
d the pulley using the thumb, index and little finger as guides.
knob clockwise until no blade slippage occurs, Do not tighten
7. Replace the blade guards.
8. Place 2-3 drops of oil on the blade.
turn hand-wheel (A) counterclockwise 1/2 turn and move the vise
jaw (B) to the desired position. Then tighten the vise jaw (B) against the workpiece by turning hand-
wheel clockwise.
2. Hardback carbon band saw blade is suitable for low-rigidity small metal workpie
plastic.
Flexback carbo
able for plumb
CHANGING THE BLADE
Raise the saw arch to
sufficiently allow the saw blade to slip off the wheels. Install t
the motor as follows:
1. Place the blade in between each of the guide bearings.
2. Slip the blade around the motor
3. Hold the blade taut against the motor pulley by pulling the blade upward with the right hand which
is placed at the top of the blade.
4. Remove left hand from bottom pulley and place it at the top side of the blade to continue the
application on the upward pull on the blade.
5. Remove right hand from blade and adjust the position of the top pulley to permit left hand to slip
the blade aroun
6. Adjust the blade tension
excessively.
USAGE OF THE QUICK VISE
The workpiece is placed between the vise jaws with the amount to be cut off extending out past the
blade. Your machine is equipped with a “quick-action” vise jaw which allows you to instantly position
the moveable vise jaw (B). Simply
Page 7 of 15
Содержание 145765
Страница 12: ...ASSEMBLY DRAWING Page 11 of 15 Page 11 of 15...