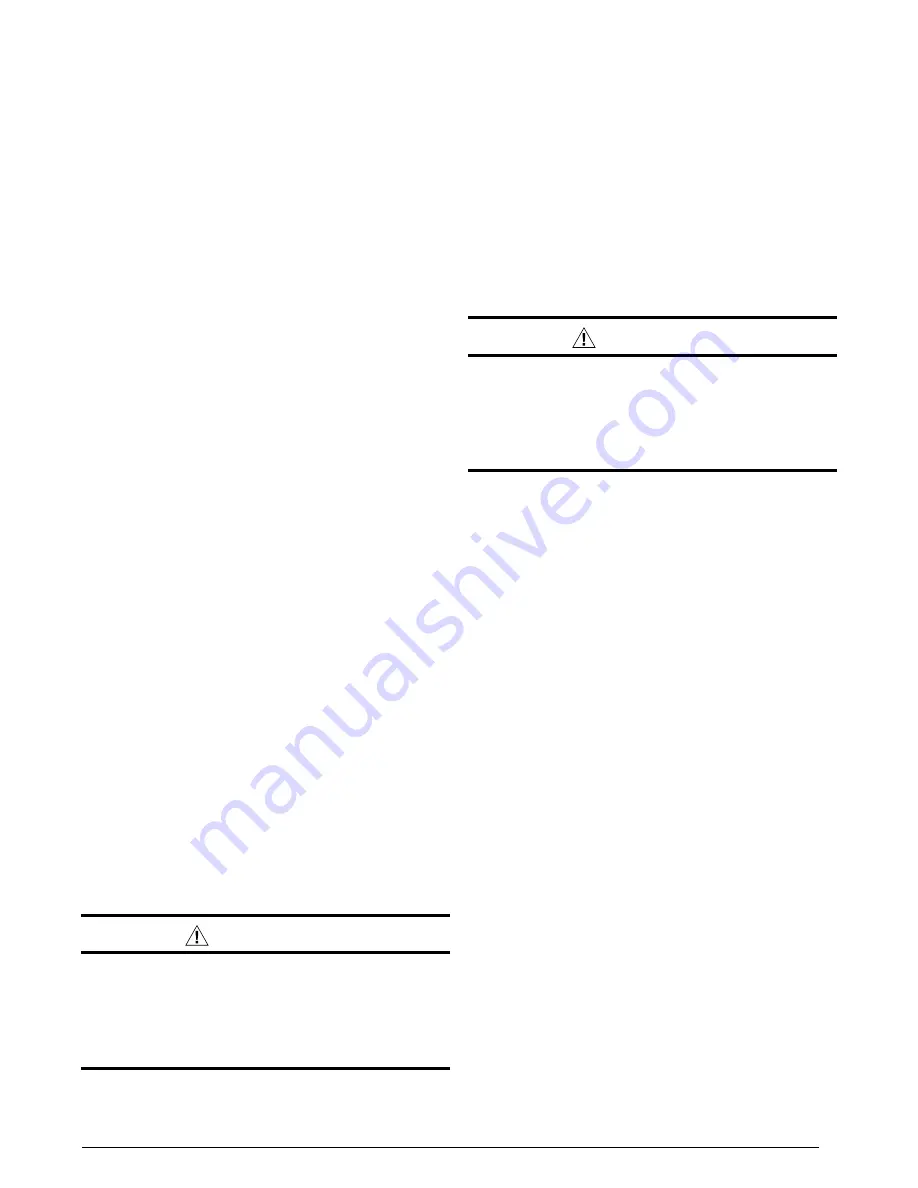
5
coupling assemblies (Figure 5).
NOte:
The amount of oil
used must cover all designated surfaces sufficiently.
6. While holding the coupling halves in proper alignment
with each other, start twisting the threads of the
female coupling nut onto the male coupling assembly.
NOte:
The coupling end faces should be parallel with each
other and visually in line; this allows the female coupling
nut (Figure 6) to be easily hand threaded for the initial 2-3
rotations. These initial rotations will bring the diaphragms
into contact and a sharp increase in torque will be felt.
impOrtANt: if the nut will not start by hand, adjust
the position of the line set to ensure proper coupling
alignement and eliminate/minimize all side load force
on the coupling during assembly.
7. Using appropriately sized wrenches (see Table 2, page
6) for both components, tighten the female coupling nut
while preventing rotation of the female body with respect
to the male coupling.
impOrtANt: the nut should be tightened until a definite
increase in resistance is felt. At this point, the nut will
have covered most of the threads on the male body. it
is important to ensure the male and female coupling
bodies DO NOt rotate during any portion of the wrench
installation.
8. Using a permanent marker or scribe, mark a line lengthwise
from the female coupling nut to the female coupling body.
9. Tighten an additional wrench flat (60°). Refer to the marking
on the coupling nut to confirm the one wrench flat has
occurred.
NOte:
This final wrench flat is necessary to
ensure the formation of the metal to metal leak-proof seal,
between the male and female couplings.
10. Proceed to
Completing the Installation
section.
Quick Connect 2
This procedure can be used if there is enough room and
lineset length to connect the lineset directly to the coil and
eliminate the need for the quick connects.
1. Verify that there is sufficient length of lineset to reach the
coil. Allow for appropriate and adequate bend radius.
2. Verify that there is sufficient room for the tubing when
appropriate radii are added to the lineset.
3. Cut the existing quick connect ends from the lineset.
4. If TXV kit and new liquid line are being installed, skip to
step 7.
5. If original liquid line is being used, relieve all pressure from
the coil by depressing the valve on the liquid line. Remove
the valve core.
6. Using all appropriate cautions, unbraze and remove the
valve holder on the liquid line.
7. Connect the suction and liquid lineset tubes.
CAUtiON:
it is recommended that a wet rag be wrapped
around the suction line in front of the close
off plate before applying heat. Failure to keep
components cool during brazing may result
in structural damage, premature equipment
failure, or possible personal injury.
8. Braze the individual connections with dry nitrogen flowing
through the joints.
impOrtANt: to prevent internal oxidation and scaling
from occuring, braze all connections with dry nitrogen
flowing through the joints.
9. Wrap the refrigerant lines with pressure sensitive neoprene
or other suitable material especially where the lines enter
the opening in the sheet metal.
10. Proceed to
Completing the Installation
section.
Downturn
1. Determine the appropriate connection kit by referring to
Table 1 (page 6).
2. Cut off 2.5 inches off the coil suction and liquid line tubes.
DO NOt swage the cut ends.
3. Connect kit parts to coil.
CAUtiON:
it is recommended that a wet rag be wrapped
around the suction line in front of the close
off plate before applying heat. Failure to keep
components cool during brazing may result
in structural damage, premature equipment
failure, or possible personal injury.
4. Braze the individual connections with dry nitrogen flowing
through the joints.
impOrtANt: to prevent internal oxidation and scaling
from occuring, braze all connections with dry nitrogen
flowing through the joints.
5. Connect the suction and liquid lineset tubes.
6. Braze the individual connections with dry nitrogen flowing
through the joints.
7. Proceed to
Completing the Installation
section.
Completing the installation
1. Check the system for leaks, including the lineset and the
brazed joints.
NOteS
•
Apply a soap and water solution on each joint or union
with a small paintbrush. If bubbling is observed, the
connection is not adequately sealed.
•
When installed in the horizontal right position, it is
necessary to apply insulation to the suction tube. Without
the insulation, water management issues may arise.
2. Evacuate the system of moisture and non-condensables
to prevent low efficiency operation or damage to the unit.
The suggested range of evacuation is 250 - 500 microns.
3. Charge the system with refrigerant.
impOrtANt: the amount of refrigerant necessary with
a microchannel evaporator will typically be different
than the amount designated on the condenser’s rating
label. Use either the superheat or subcooling method
(depending on the metering device used) to properly
charge the system. refer to the condenser unit’s
documentation to determine the amount of superheat
(typically a minimum of 5° F) or subcooling (typically
between 8° F & 12° F).
4. Install the coil access door (if removed).
5. Properly dispose of all removed parts.
6. Apply power to the unit.