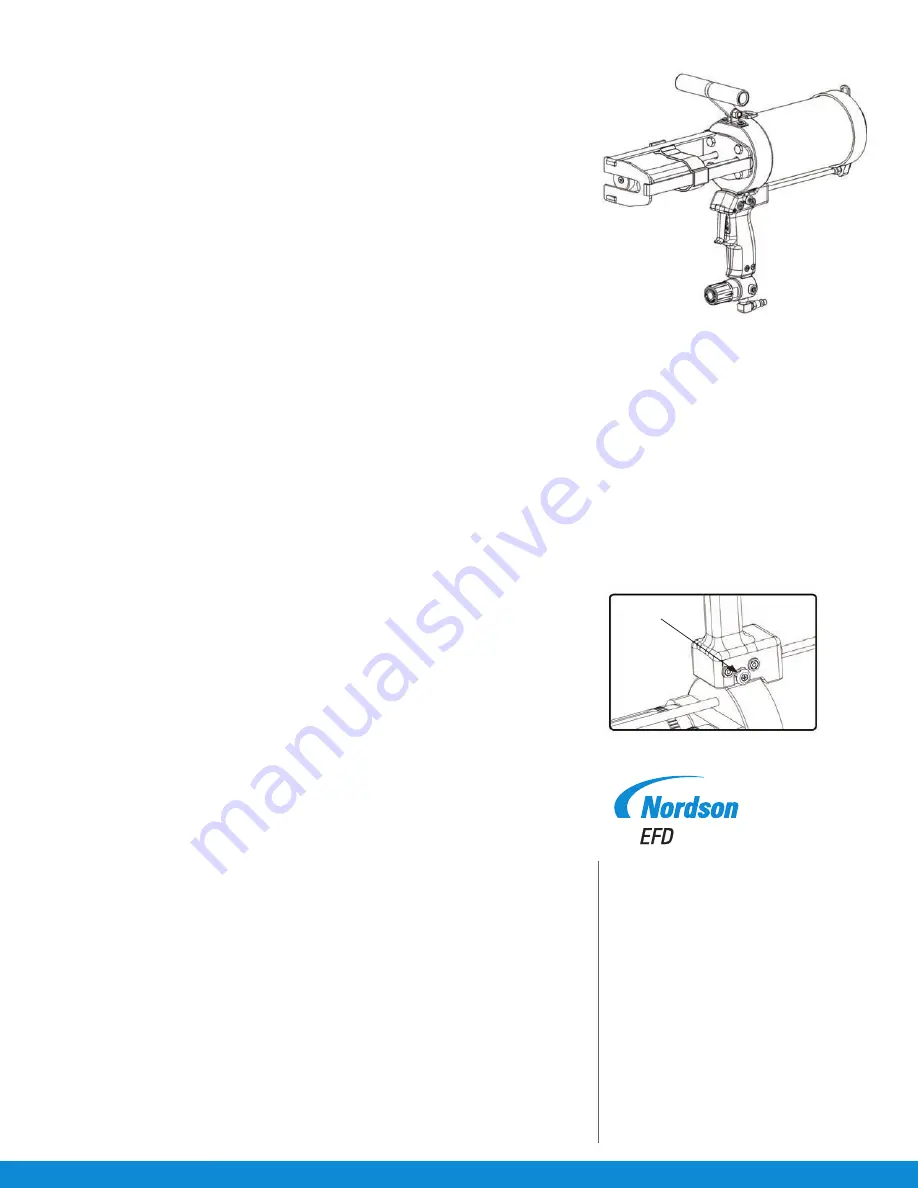
Safety
• 120 psi maximum operating pressure.
• Do not drop or let anything drop on the applicator.
• Do not damage or polish the piston rods.
• Store in a clean dry environment.
•
Eye protection must be worn at all times when the applicator is in operation.
•
Do not point the applicator at anyone while the tool is in operation.
•
Do not place any part of your body either inside or in front of the material
chambers while the applicator is connected to an air supply.
• Read the material safety data sheets (MSDS) on the material being used.
Cleaning
Keeping the applicator clean is important for long life and trouble-free operation.
Due to the tool’s rugged construction, most solvents can be used to remove
material. It is not recommended to immerse the tool in a cleaning agent, as this
may adversely affect the internal seals of the applicator. Special care should be
taken to ensure no material residue is left on the piston rods.
General dispensing instructions
Note: It is highly recommended that you advance and retract the pistons in an
empty applicator until you are comfortable with its operation.
The dispensing rate of the applicator is determined by the air pressure used.
It is advised to begin at the lowest pressure setting and adjust the pressure
to your desired speed. Upper handle can be adjusted by loosening main nut.
To load twin cartridges
1. Dispenser is designed to dispense 1500mL cartridges in 1:1 ratio without
the need to change ejectors.
2. Retract the piston rods by switching the forward/reverse button and then
actuate the trigger to allow the rods to travel back into the barrel.
3. Ensure that the front of the cartridge is seated against the applicator’s front
plate before dispensing.
To dispense twin cartridges
1. Remove caps and/or plugs from the cartridge and install a new static mixer
on the end of the cartridge. Some static mixers require a plastic nut to
secure it to the cartridge; specify p/n 7702598.
2. With the regulator at low pressure, switch the forward/reverse button to the
forward position and then actuate the trigger to allow the rods to travel
forward to ensure the piston ejectors are properly seated against the
cartridge pistons.
3. Do not apply adhesive to the work area until the proper mixture is exiting
the static mixer.
4. To adjust the material flow, actuate the trigger and adjust the air pressure
with the regulator until your desired dispensing rate is achieved.
5. To stop dispensing, release the trigger to exhaust the air pressure within
the tool.
6. Note: Mixed compounds will harden in the static mixer if left unused for a few
minutes. To prevent rupturing of the cartridge, replace the static mixer.
Forward/Reverse
Button
For Nordson EFD LLC sales and service in over 40 countries,
contact Nordson EFD or go to www.nordsonefd.com
Global
East Providence, RI USA
800-556-3484; +1-401-431-7000
[email protected]
Europe
Dunstable, Bedfordshire, UK
0800 585733; +44 (0) 1582 666334
[email protected]
Asia
[email protected]
China: +86 (21) 3866 9006; [email protected]
India: +91 80 4021 3600; [email protected]
Japan: +81 03 5762 2760; [email protected]
Korea: +82-31-736-8321; [email protected]
SEAsia: +65 6796 9522; [email protected]
©2015 Nordson Corporation 7363801 v020915