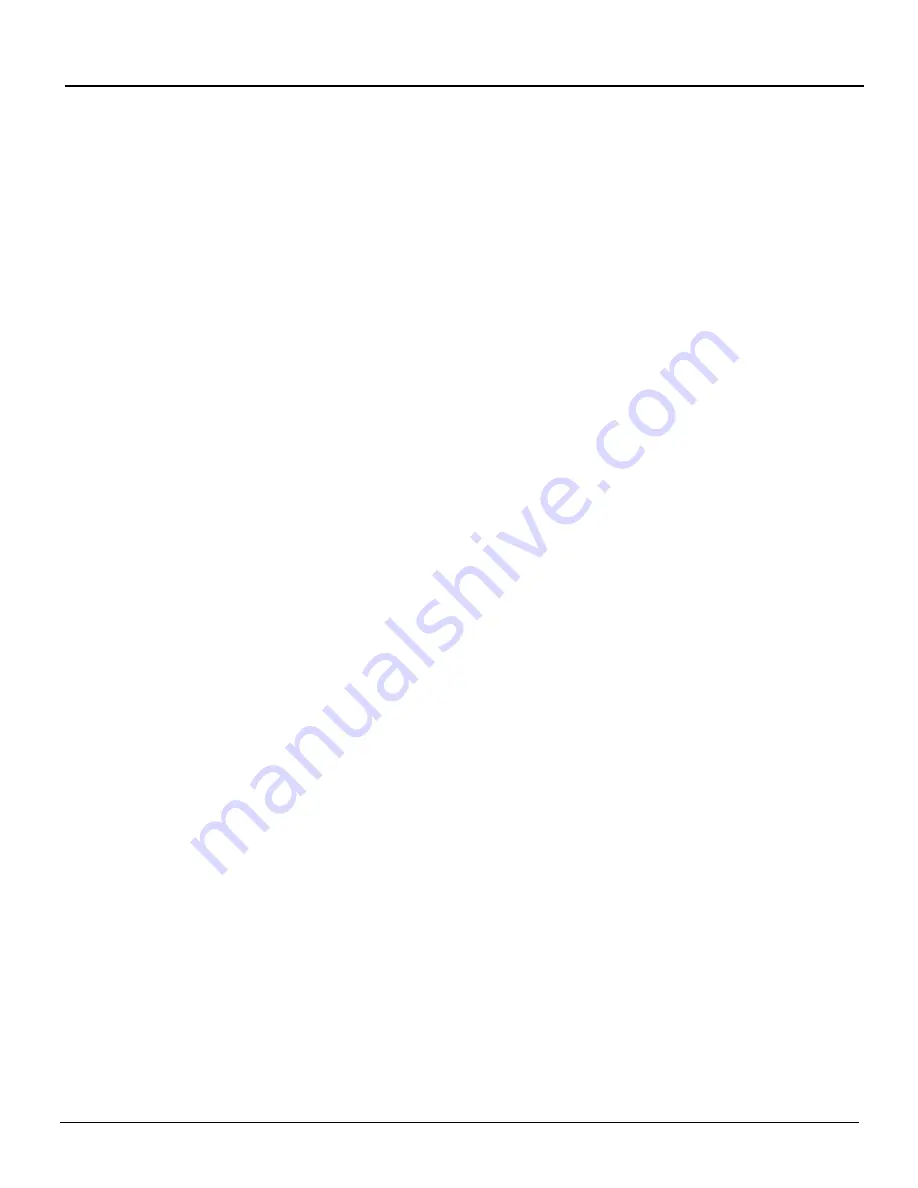
HYDRAULIC
Anchor Applicator Model BAAM
Section H-16
MAR/2005 (49454100)
While machine is running, and before working, inspect for leaks. If the machine has not been run for
some time, oil may thicken causing a variety of malfunctions. If this is true, make certain that the oil
tank has been properly drained, cleaned and refilled.
If your visual inspection does not indicate the possible malfunction, refer to the troubleshooting guide
that follows.
FLUID CONTAMINATION
Contamination comes in many forms. It may be air, water and cutting oils, rust, chips and grit. It is
usually easier to keep contaminants
out
of a system rather than remove them after they are
in
the
system.
Bulk handling and the re-use of oil containers almost guarantees you that "new" oil will be dirty. Make it
a practice to filter all "new" oil before adding it to your system. Make it another practice to change
filters on a regular basis
before
they become clogged.
LOCATING LEAK SOURCES
Petroleum oils are used in most hydraulic application to lubricate parts as well as transmit power. As
oil temperature increases, however, the lubricating film thins out. The result is rubbing parts supported
by the oil film move closer together; friction and wear increase; seal materials age more quickly,
become stiff and hard, and may readily permit leakage.
The first step in locating leaks is to eliminate the possibility that an over-filled reservoir or spill created
the "suspected" leak. The next step would be to clean the suspected area and watch. Leaks usually
occur in fittings, hoses, O-rings, and other seals.
Most leaks occur at fittings, but too often, finding the fitting that is leaking is difficult because the fluid
runs along the hose and drips off at some other point. Leaks in high pressure lines sometimes are
difficult to pin-point because the fluid comes out as a mist.
Once you find the location of a leak, the specific cause has to tbe determined before it can be
corrected. A scratch in a fitting seat or a cut in a seal lip that is big enough to leak excessively can still
be too small to find with the naked eye. The use of a magnifying glass would assist you.
HOSE LIFE
Hose leakage or failure many times occurs where the end fitting grips the hose. Check the system for
pressure spikes or surge. If bulges or bubbles occur on a flexible hose, a leak is taking place within the
layers. The hose should be replaced.
High oil temperatures (over 200 degrees Fahrenheit, 93 degrees Celcius) quickly harden or stiffen a
rubber hose. When pressure pulses flex a hardened hose, it fails by cracking. Every increase of 25
°
F
(14
°
C) cuts hose life in half. Use a replacement hose rated for actual fluid temperatures. Keep a log of
hose use so replacement can be made before failure occurs.
If a hose is installed with a twist in it, high operating pressures tend to force it straight. This can loosen
the fitting or even burst the hose at the point of the strain.