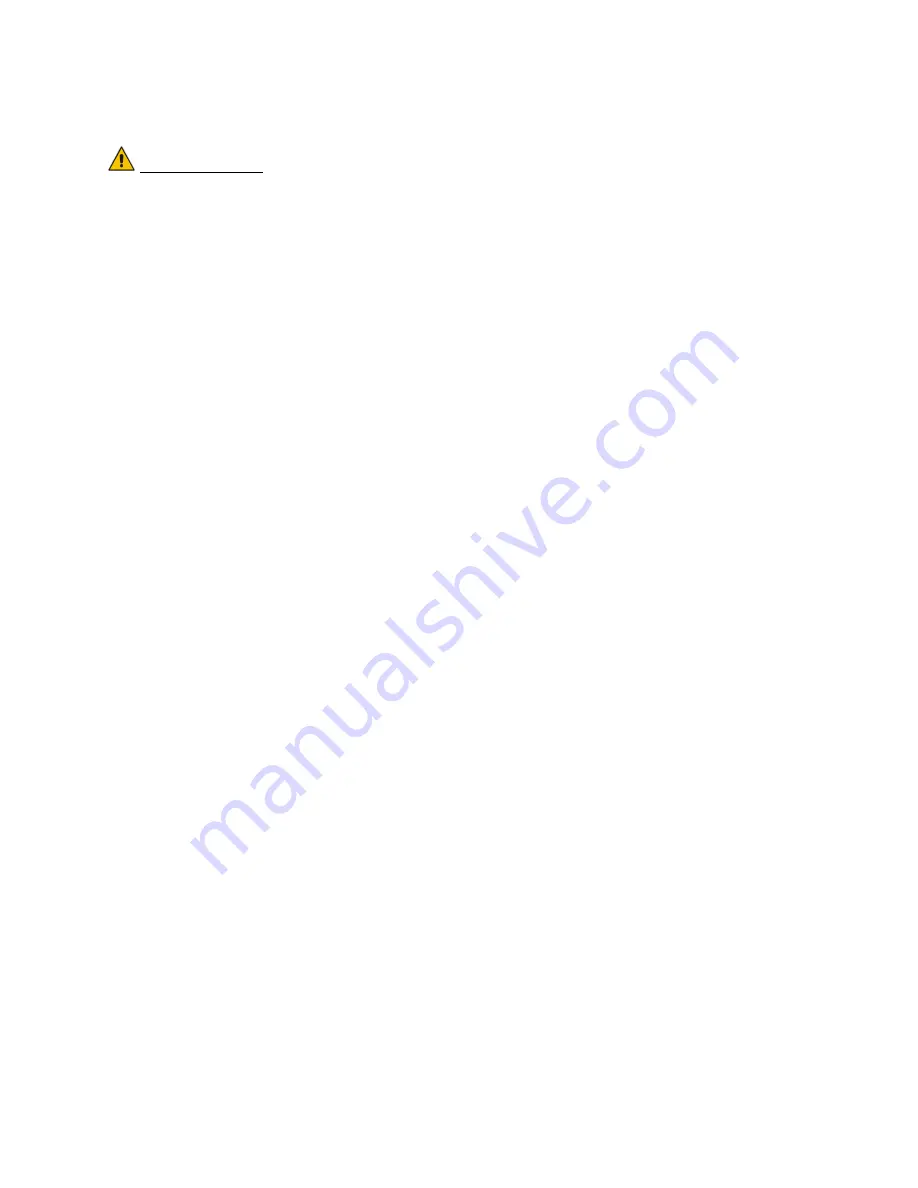
11
4.2 Boom Speed Test
IMPORTANT:
Let the sprayer run for several minutes to heat up the hydraulic oil.
Raise/lower the left and right booms, main and hydraulic roll sections
several times to help get the system (hydraulic oil, valve solenoids)
warmed up. This will simulate field conditions and makes QUITE a
difference in some cases. Grease all moving parts for consistent results.
1.
Lower each boom and main section as close to the ground as possible.
2.
Set your sprayer at field working RPM on the throttle and mark this value in
Table 6
.
NOTE: You will need a stopwatch or a watch that displays “seconds” for
the next step.
3.
Individually raise the LEFT boom from its extreme LOW position to the very
TOP of its travel. Note the length of time it takes for this and record this in
Table 6
,
“Trial #1” for “Left UP”.
4.
Individually lower the LEFT boom from its extreme HIGH position to the
BOTTOM of its travel. Note the length of time it takes for this and record this
in
Table 6
,
Trial #1, for “Left DOWN”.
NOTE:
You will need to be careful when lowering the booms at full speed
to the bottom of their travel so that they don’t hit the ground. You
may want to mark positions on the cylinder pistons at which to
stop the test while using another person as a spotter. Raising your
main section will give you more working height to do this test.
Please use common sense to avoid damage!
5.
Similarly, record two more time trials (Trial #2 & #3) for the LEFT boom and
record in
Table 6
.
6.
Repeat
Steps 3
through
5
for the RIGHT boom and the MAIN section.
7.
Repeat a similar procedure for the hydraulic (active) roll feature (if your sprayer
supports this) for the clockwise (CW) and counter-clockwise (CCW) rotations.
8.
Average the times of the three trials recorded for each boom movement function
(e.g. LEFT, RIGHT, etc.) and record this calculation in the appropriate “Average
Time” slot in
Table 6
.
9.
These “Average Times” now represent how quickly your system can react to
Содержание UC4 Total Control
Страница 23: ...21 Figure 15 Installation Details ...
Страница 30: ...28 Figure 24 General Valve Block Mounting Location Figure 25 Installed NORAC Valve Block ...
Страница 41: ...39 5 3 Item C3 44656 Valve Cable Variable Rate 5 4 Item C4 44651 Valve Extension Cable ...
Страница 42: ...40 5 5 Item C10 44650 39 Power Cable Generic Self proplelled ...
Страница 43: ...41 5 6 Item C11 44651 03 Extension Cable Valve Generic ...
Страница 44: ...42 5 7 Item C12 44658 32 Interface Cable ...
Страница 45: ...43 5 8 Item C14 44658 28 Interface Cable Power Pigtail ...
Страница 46: ...44 5 9 Item C15B 44658 41 Interface Cable Hand Control RG4 5 10 Item C16 44658 33 Interface Cable Bypass ...