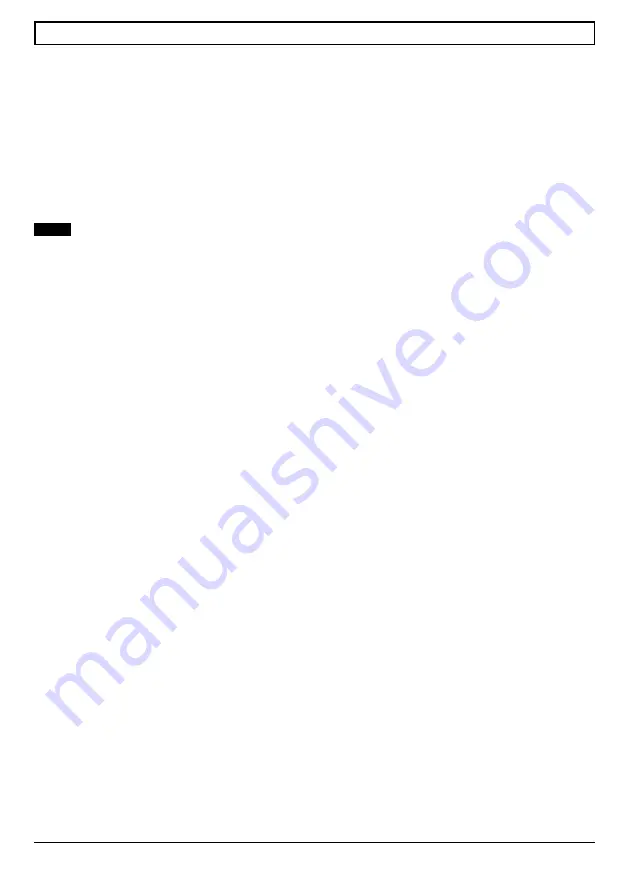
16
ASSEMBLY AND COMMISSIONING RECOMMENDATIONS
LSHRM - FLSHRM - PLSHRM - Permanent Magnet Assisted Reluctance motors
5411 en - 2019.04 / b
The "reinforced rotation mechanism protection" system
is required for B2 type applications or for supply voltages
greater than 510 V.
This type of protection includes the following devices:
- The LSHRM/FLSHRM motors in the interchangeable
range with a power ≥ 45kW at 1500 rpm and ≥ 55 kW
at 3000 rpm have an insulated non-drive end (NDE)
bearing as well as a drive-end grounding ring.
- The LSHRM motors in the compact range with frame
size ≥ 225
have an insulated non-drive end (NDE)
bearing and a drive-end grounding ring.
NOTE
• The reinforced protection solution includes the use of
an insulated speed or position sensor (absolute
encoders, resolvers, etc.) when equipped with bearings
in contact with the motor shaft. For more information,
refer to the technical guide on speed and position
sensors; ref. 5664.
3.5 - Connections
3.5.1 - Good wiring practices
3.5.1.1 - General
The user and/or the installer are responsible for con-
necting the motor and drive system in accordance with
current legislation and regulations in the country of use.
This is particularly important as concerns cable size and
the connection of earthing and grounding components.
The following information should never be used as a
substitute for current standards, nor does it relieve the
installation company of their liabilities.
3.5.1.2 - Equipotential bonding and earthing
The primary reason for grounding components and
equipment in an industrial installation is to protect
people and minimize the risk of damage in the event of
a major fault on the power supply or following a lightning
strike.
The second objective of earthing is to create an equipo-
tential voltage reference with low impedance, common
to all equipments that reduces:
- the risk of interference between equipment in instal-
lations which include sensitive interconnected elec-
tronic and electrical systems
- the risk of breaking equipment in the event of fault
currents
- the risk of current flowing in the bearings of electrical
machines supplied by frequency inverters
- the level of conducted or radiated electromagnetic
emissions
It is essential that the earth network is designed and
implemented by the installation supervisor so that its
impedance is as low as possible, so as to distribute the
fault currents and high-frequency currents without them
passing through electrical equipment. The underlying
philosophy of any earthing installation is to maximize
mesh bonding of ground connections between metal
parts (machine frame, building structures, pipework,
etc.) and connect this mesh bonding to earth at multiple
points. Metal grounds must be mechanically connected
to each other with the largest possible electrical contact
area or with grounding strips.
The motor housing must be connected to the equipment
frame with high-frequency flat braids. For more informa
-
tion, see the guide to good practices for motor drive sys-
tems ref. 5626 (www.leroy-somer.com).
Under no circumstances can earth connections
designed to protect people, by grounding metal parts via
a cable, serve as a substitute for equipotential bonding
(see IEC 61000-5-2).
In particular, the motor earth terminal (PE Protective
Earth) must be connected directly to the drive earth ter-
minal. One or more separate PE protective conductor(s)
is(are) mandatory if the conductivity of the cable shield-
ing is less than 50% of the conductivity of the phase
conductor.
3.5.1.3 - Drive power supply cables
These cables do not necessarily need shielding. Refer
to the drive documentation.
3.5.1.4 - Motor cables
Shielding the power conductors is the preferred method
to ensure that common mode currents can return to their
point of origin without dispersing into other possible
paths (equipotential conductors, piping, building struc-
ture, etc.). This approach significantly reduces the
levels of electromagnetic emissions, both conducted
and radiated.
For this reason, shielded cables must be used between
the drive and motor to ensure compliance with EMC
emission standards (IEC 61800-3, etc.). Shielded
cables are also used to limit shaft voltage and the risk of
damage to the bearings.
• Shielded motor cables
Shielded cables must always be symmetrical multi-con-
ductor cables with low stray capacity. Cables with a
single equipotential bonding conductor can be used up
to cross-sections of around 10 mm
2
.