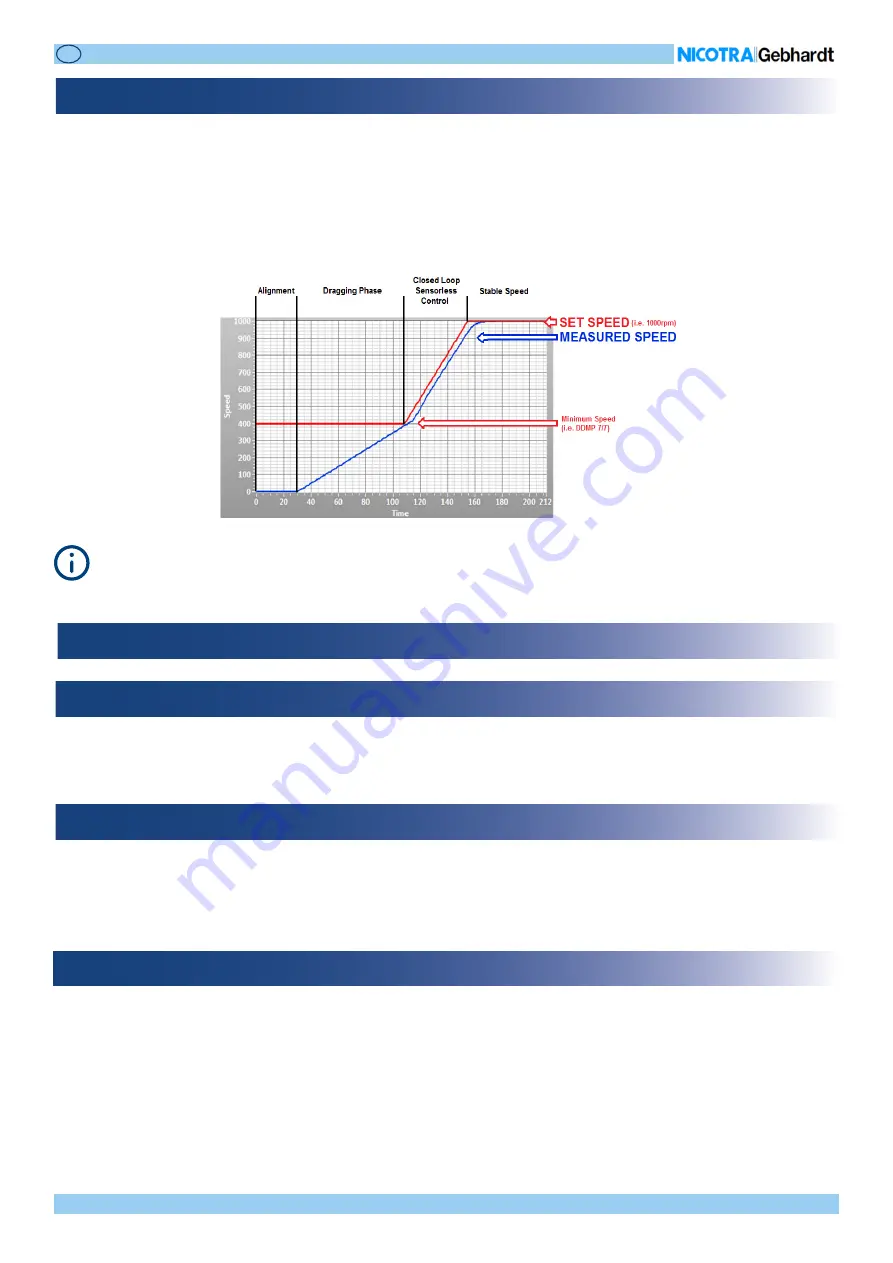
Rev. 0 - 05/11/2020
OPERATING MANUAL
OPERATING MANUAL
EN
EN
34/48
In the following paragraph the starting phase of a fan is shown.
•
The first phase when the fan receives a command to start running is the ALIGNMENT. During this phase the driver aligns the rotor.
•
The second phase is the dragging phase, where the fan gradually increases its speed to the minimum in open loop. In this phase
the current and speed values present in the Input Register can’t be taken in consideration.
•
The last phase is the closed loop where the sensorless control is active and from the minimum speed to the target speed the
fan accelerates with different ramps basing on the fan size and the wheel inertia. The acceleration and deceleration values are
different and to avoid overvoltage alarm or loss of synchronism alarm, the deceleration is always lower.
12.6 Soft start
During the ALIGNMENT and DRAGGING phases a Loss of Synchronism alarm could occur if there is a condition of wrong
rotor starting position or wrong position estimation during the open loop phase. This is not a blocking alarm; therefore
the fan stops and auto-restarts after few seconds.
13. SOA LIMITATIONS
The speed limits can be adjusted for the signal rescaling, but also to limit the noise in the final application.
The
Input Register 2
indicates the Speed Reference (minimum speed during alignment and dragging and the Set Speed in Closed
Control Loop). The
Input Register 3
indicates the Measured Speed.
13.1 Speed limitation
The driver is set by factory default to the max achievable electrical input power to the driver depending on the model. During the
functioning it is possible to monitor the power absorption by reading the
Input Register 31
. If for some application it is necessary
to keep the absorption of the fan below a defined power value, it is possible to reduce the max power out by modifying the
Holding
Register 36
.
13.2 Power limitation
The drivers are set by factory default to the max peak current out that changes depending on the motor windings characteristics.
During the functioning it is possible to read the peak current to the motor by reading the
Input Register 12
.
It is possible to reduce the motor current by modifying the
Holding Register 7
. It is suggested to keep the motor current above
3500mA.
13.3 Output current limitation