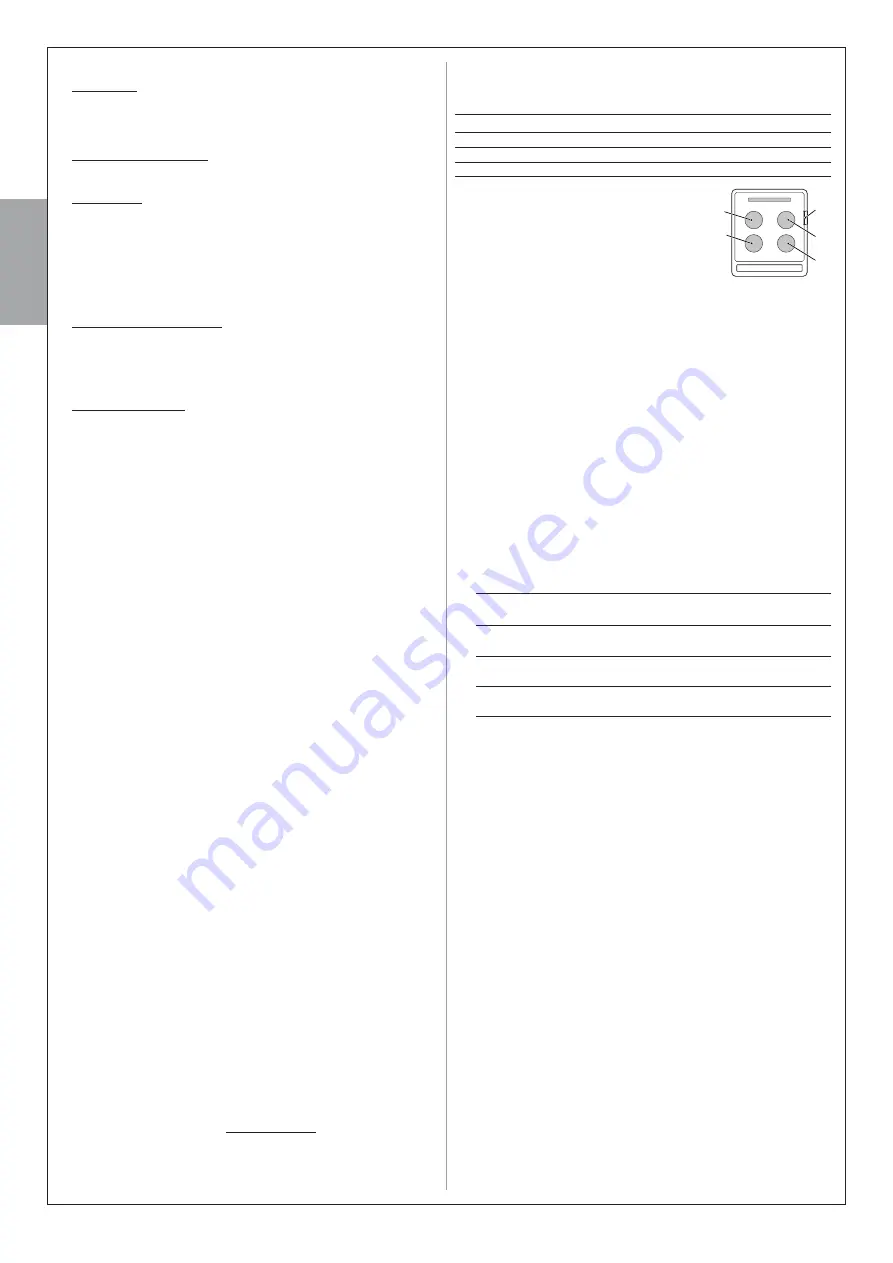
27
– English
English
% /LVWRIPRGLƄDEOHSDUDPHWHUV7DEOH
• Pause time
: this is the time implemented by the control unit after an
opening manoeuvre before automatically closing the leafs.
Warning
–
the pause will only be enabled if the “complete cycle” option is pro-
grammed (i.e. automatic re-closing of the gate) during programming as
described in paragraph 7.3.2.
• “Pedestrian” command
: comprises 4 types of command related to
the leaf “partial open”. During use of the automation the set command
is activated when the key T2 is pressed on the transmitter.
• Motor force
: normally, during a manoeuvre the motor implements a
RODBHjBENQBDSNLNUDSGDKD@ESNBNLODMR@SDENQHSRVDHFGSEQHBSHNMNM
the hinge pins and any presence of wind etc.
During a manoeuvre, if an inadvertent obstacle brakes the leaf further,
the motor increases the force applied in the attempt to overcome the
obstacle. At this point, if the force generated by the obstacle causes
the motor to exceed the set level, the control unit immediately activates
a safety manoeuvre, inverting movement of the leaf. Therefore, if the
parameter is suitably set, this guarantees increased safety.
• “Step-by-Step” command
: comprises 4 types of “step-step” com-
mand, i.e. a command in which each press of the key activates the sub-
sequent manoeuvre after the one completed or in progress, according to
the pre-set order in the set sequence. During use of the automation, the
set command is activated when the transmitter key T1 is pressed and on
the devices connected to the control unit by means of the terminal “SbS”.
• Pressure discharge
: this parameter, when suitably set, enables dis-
charge of the pressure applied on the structure when the leafs are sta-
tionary and positioned against the opening or closing travel limit stops.
All parameters can be set as required, with the exception of the param-
eters “Motor force” and “Pressure discharge” which must comply with the
following requirements:
Motor force:
• Never use excessively high force values to compensate for any abnor-
mal gate movements caused, for example, by points of increased fric-
tion. In fact, excessive force may impair correct operation of the safety
system or damage the leaf.
• If the “Motor force control” is used in support of the system for impact
force reduction, after each adjustment the force measurement proce-
dure must be performed, as envisaged by standard EN 12445.
• The local weather conditions (for example, strong gusts of wind) can
HMkTDMBDKD@ELNUDLDMSB@TRHMF@MHMBQD@RDHMSGDKN@C@OOKHDCNM
the motor. Therefore the “Motor force” parameter may require periodic
adjustments”.
Pressure discharge:
• Never use excessively low pressure discharge values as these would
have no effect; they may also cause damage to the leaf and the travel
limit stop.
• Never use excessively high pressure discharge values as these would
keep the leaf separate from the travel limit stop.
• Use a pressure discharge value that enables the leaf to remain in con-
tact with the travel limit stop, without this applying excessive pressure
on the motor.
B.3 - Checking parameter settings
The settings of a required parameter can be checked at any time accord-
ing to the procedure below.
01.
In
Table 9
select the parameter to be checked (the meanings of the
parameters are explained in paragraph B.2).
02.
On the transmitter, press and hold keys T1 and T2 or T1 and T3
simultaneously (see
Table 9
) for at least 5 seconds; then release the
keys.
03.
(within 3 seconds) On the transmitter, press and hold the key of the
O@Q@LDSDQSNADBGDBJDC@MCQDKD@RDVGDMSGDk@RGHMFKHFGSRS@QSRSN
k@RG
"NTMSSGDMTLADQNEk@RGDR@MCBNMRTKS
Table 10
(column “N.”) to
locate the same number; read the currently set value of the parameter
being checked alongside.
Example
LIWKHƅDVKLQJOLJKWHPLWVƅDVK
-
HVWKLVPHDQVWKDWWKHqSDXVHWLPHrLVSURJUDPPHGDWVHFRQGV
C - MEMORISING OR DELETING RADIO
TRANSMITTERS
C.1 - Memorising the FIRST transmitter
The transmitters supplied are not memorised; therefore, at the beginning,
it is necessary to memorise the FIRST transmitter (Mode 1), with the pro-
cedure C.2.
C.2 - “Mode I” memorisation procedure
When this procedure is used, the system automatically associates each
transmitter key with the following commands:
key
T1
=
“Step-by-Step”
command (> Open > Stop > Close > ...)
key
T2
=
“Pedestrian”
command (> Total opening of 1 leaf > ...)
key
T3
= command
> Open > Stop > ...
key
7
= command
> Close > Stop > ...
Notes:
•
7KH7NH\LVQRWXVHGLQWKLVDSSOL
-
cation.
s7KHFRPPDQGVRIWKH7DQG7NH\V
FDQEHPRGLƄHGE\WKHXVHUVHHSDUDJUDSK%
DQG7DEOHs7KHV\PEROq!rPHDQVqSUHVV
the key once”.
Therefore to memorise these commands simul-
taneously on the 4 keys of a transmitter, pro-
ceed as follows.
01.
On the control unit, press and hold P1 on the receiver until the green
Led P1 illuminates, and then release.
02.
(within 10 s) press any key on the transmitter for at least 2 s to memo-
rise it.
If the memorisation procedure is successful, the LED P1 will emit 3
k@RGDR
03.
If there are other transmitters to be memorised, repeat phase 02
within the next 10 seconds; otherwise the memorisation procedure
terminates automatically.
A transmitter memorised in Mode I can control 1 automation only, using
the 4 commands.
C.3 - “Mode II” memorisation procedure
When this procedure is used, it is the installer’s task to associate the
transmitter key with the required command, from those available. There-
fore, to memorise a command on a key, proceed as follows. Therefore, to
memorise a command on a key, proceed as follows.
01.
Refer to the table below; choose the command to be memorised
and note the number of times the transmitter needs to be pressed (in
phase 03) to memorise it.
•
“Step-by-Step” command (
> Open > Stop > Close > ...
)
press once
•
“Pedestrian” command (
> Total opening of 1 leaf > ...
)
press twice
•
command
> Open > Stop > ...
press three times
•
command
> Close > Stop > ...
press four times
Notes:
s7KHFRPPDQGVq6WHSE\6WHSrDQGq3HGHVWULDQrFDQEH
PRGLƄHGE\WKHXVHUVHHSDUDJUDSK%s7KHV\PEROq!rPHDQV
“press the key once”.
02.
On the control unit, press P1 for the same number of times as the
command to be memorised and ensure that Led P1 emits a number
NEPTHBJk@RGDRBNQQDRONMCHMFSNSGDMTLADQNESGDRDKDBSDCBNL
-
mand.
03.
(within 10 seconds) press the required key of the transmitter to be
memorised for at least 3 seconds. If memorisation is successful, Led
/NMSGDBNMSQNKTMHSVHKKDLHSRKNVk@RGDR
If there are other transmitters to be memorised for the same type of
command, repeat step 03 within the next 10 s otherwise the memori-
sation phase will end automatically.
To
memorise another key, repeat the procedure from the beginning.
C.4 - Duplicating an existing and previously memo-
rised transmitter
This procedure enables memorisation on the control unit of a new trans-
mitter, by duplicating the characteristics of another existing and previously
memorised transmitter. During this procedure, take care to observe the
following warnings:
– if the transmitter to be duplicated is memorised in Mode I, when the
request to press a button is made, any key on the two transmitters can
be pressed;
– otherwise, if the transmitter to be duplicated in memorised in Mode II,
when the request to press a button is made, the key with the command
to be duplicated must be pressed on the “old” transmitter, followed by the
key to be associated with this command on the “new” transmitter.
01.
Ensure that the two transmitters are located within the reception
range of the automation and press the key on the “new” radio trans-
mitter for at least 5 seconds, then release.
02.
Press the key on the OLD radio transmitter slowly 3 times.
03.
Press the key on the NEW radio transmitter slowly once.
T4
T2
T5
T3
T1
Содержание ALTO100C
Страница 1: ...GATE AUTOMATION ALTO Instructions and warnings for installation and use ...
Страница 10: ...9 English English 1 2 3 45 3 1 2 a c b OK b a a b c d b a 5 6 7 8 9 10 11 12 13 13 ...
Страница 13: ...English 12 English OK b a 1 2 17 1 2 16 3 AA ok BB no OK 18 2 1 ...
Страница 14: ...13 English English b a 1 2 3 5 6 20 a b 1 2 3 19 ...
Страница 17: ...English 16 English a b a b 1 2 3 5 6 7 8 9 10 11 23 ALTO100M gearmotor connection ref paragraph 5 1 ...
Страница 35: ...IS0488A00MM_12 01 2017 Nice S p A Via Pezza Alta 13 CDQYN 35 S KX HMEN MHBDENQXNT BNL ...