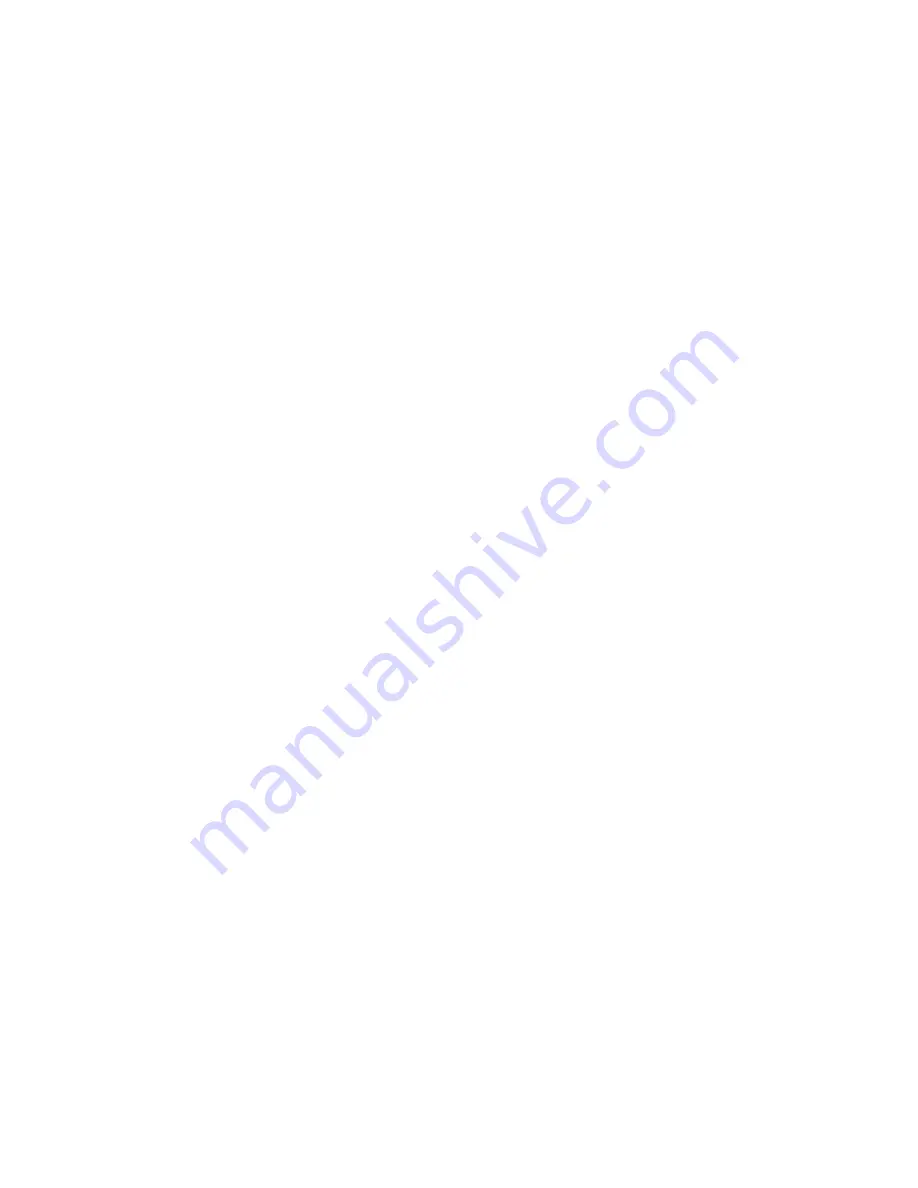
NIBCO Technical Services • Phone: 1.888.446.4226 • Fax: 1.888.336.4226
5
IV. VALVE INSTALLATION PROCEDURE
– FLANGE, LUG & WAFER STYLE ONLY
Always position the connecting pipe flanges accurately in the line, allowing sufficient space between
the flanges for the valve. Make sure the pipe flange faces are clean of any foreign material such as
scale, metal shavings or welding slag. Valves should be installed with the disc in the closed position
to prevent damage to sealing surfaces.
NOTE: Fully open and fully shut any butterfly valve before attempting to install it into a system, to
ensure and confirm the valve is operational across its travel range and seating properly in the opened
and shut positions.
1. Carefully insert the valve between the pipe flanges. Do not apply any lubricants to the seat faces
as this may damage them.
2. Line up, center and secure the valve between flanges using desired bolts or studs as listed in Table
4. Do not tighten bolts at this time.
3. Carefully open the valve to assure free unobstructed disc movement. Disc interference may result
when valves are installed in pipelines having smaller than normal inside diameters, such as heavy
wall pipe, plastic-lined pipe, as-cast flanges, or reducing flanges. Interference can also occur when
connecting directly to a swing check or silent check. Suitable corrective measures must be taken
to remove these obstructions, such as taper boring the pipe or installing a spacer or spool piece.
4. After proper operation is verified, tighten the bolts to the minimum recommended bolt torques listed
in Table 3, below, using a cross-over pattern as shown in Figure 3.
NOTE:
When installing any
cartridge liner butterfly valve, i.e. N200 valves or LD 1000/2000
valves NPS 14” and larger,
between two flanges, it is critical that the cartridge liner be evenly compressed from both
sides of the mating flanges (REFER to NIBCO Technical Bulletin NTB-1012-03
for more
details
). NIBCO recommends a multi-stepped process utilizing the cross-over pattern be used to
draw the flanges against the liner from both side of the valve at the same rate, ensuring the liner
is compressed evenly. This method differs from the practice used on smaller valves, wherein one
flange side is completely tightened before moving to the opposite side.
5. Pressurize piping to valve and inspect for leakage. If leakage is observed, tighten bolts using
cross-over pattern, increasing torque until leak stops.
DO NOT EXCEED MAXIMUM TORQUES LISTED IN TABLE 3 BELOW.
6. Recommended torques are made without warranty. Installer must verify proper strength bolts for
application. Bolts shall be clean and un-lubricated.
NOTES:
LUG STYLE VALVES
– Extra care should be used when installing with raised faced flanges.
Over tightening of bolts can result in broken valve lugs.
Class 250 cast iron and Class 300 steel flanges
cannot
be used on these valves.
Rubber faced or mechanical flanges are
not
recommended.
These valves are
not
recommended for steam service.
Valves should
not
be assembled to the flanges & then welded into the piping system.
Lever-lock handles are
not
recommended for use on 8” and larger valves.
Do
not
install valves with EPDM liner in compressed air lines.