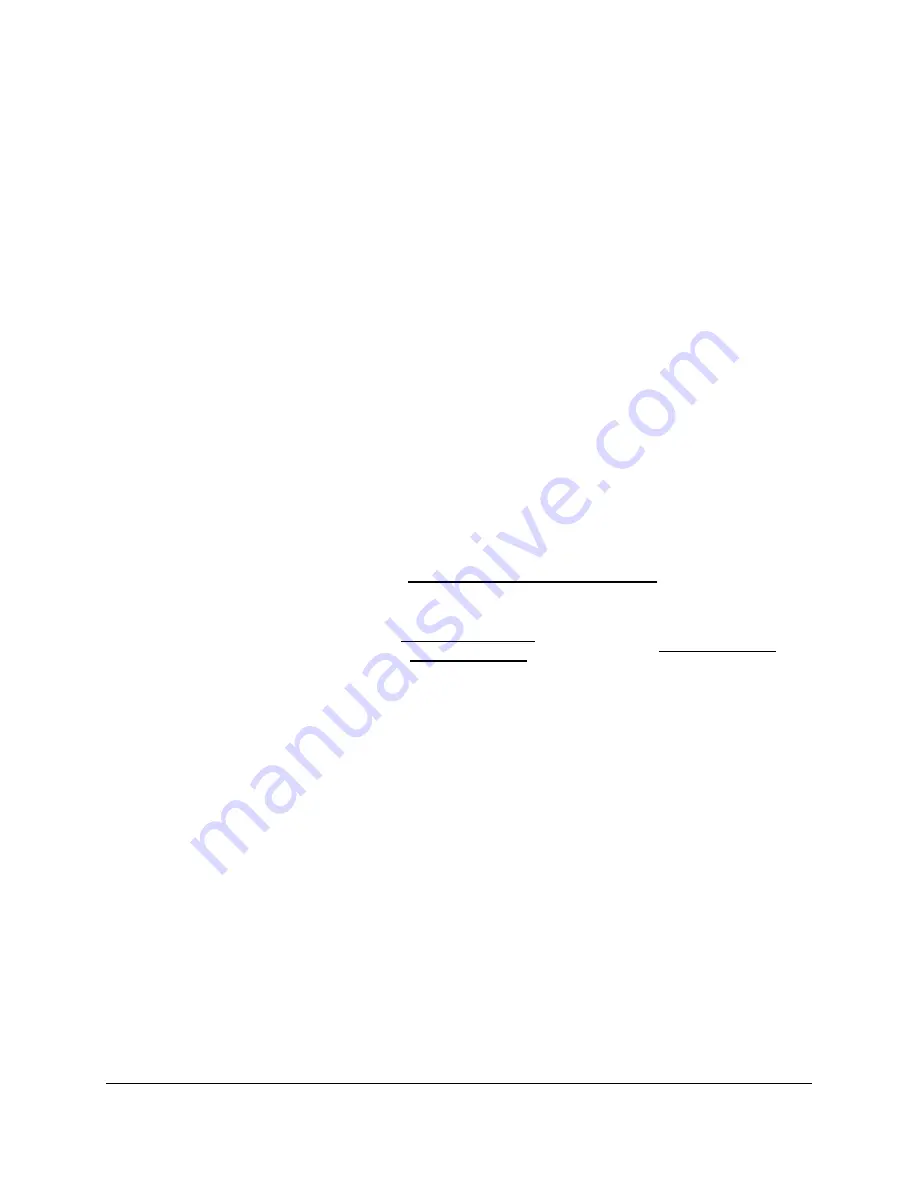
December 2019
112
LDC-3706 Series Laser Controller
temperature setpoint will fall below the setpoint temperature, and the current will be set to the
minimum current value, which causes the maximum possible rate of heating. This is seen on the
graph at point 3 and point 4. When the temperature falls below the setpoint temperature at point 3,
the current immediately switches to the minimum value, as seen at point 4. This cycling of current
from heating to cooling occurs 10 times during an auto-tune procedure. This is why there are 10
cycles shown between point 1 and point 9 on the graph.
After the first three cycles have been completed (point 5 on the graph), the auto-tune procedure
begins to record the information needed to determine the PID values. The information needed is the
time it takes for a heating and cooling cycle to complete, the maximum temperature reached during a
cycle, and the minimum temperature reached during a cycle. For the fourth cycle in the graph above,
shown between point 5 and point 8, the time from point 5 to point 8 will be recorded to get a cycle
period measurement. The maximum temperature (point 6 on the graph) and minimum temperature
(point 7 on the graph) will also be recorded. These three values will be recorded for the last 7 cycles
of the procedure. After 10 total cycles are completed (point 9 on the graph), the output is disabled
and the PID values are calculated.
To calculate the PID values, first the measured amplitude of the cycle is calculated by taking the
maximum measured temperature minus the minimum measured temperature for each cycle. Then,
the average of the seven measured amplitudes and the seven measured cycle periods will be
calculated. Using these averages and the maximum and minimum TEC current settings, the PID
values are calculated as follows:
=
−
=
4
∗
∗
= 0.6
∗
=
1
2
=
32
The PID values are then saved into the manual PID values and the instrument is ready to control to
the given setpoint. The PID tuning process typically takes 5 to 10 minutes. The PID values will be
appropriate to control to set points near the setpoint used during the procedure under similar
conditions to those that occurred during the auto-tune procedure. These values can be altered
through the manual PID setting section of the front panel or through remote commands to fine tune
performance or to adjust for different set points and operating conditions.
Содержание LDC-3706 Series
Страница 2: ......
Страница 12: ...December 2019 x LDC 3706 Series Laser Controller...
Страница 15: ...December 2019 3 LDC 3706 Series Laser Controller Figure 1 3 LDC 3736 Front Panel Figure 1 4 LDC 3736 Rear Panel...
Страница 18: ...December 2019 6 LDC 3706 Series Laser Controller LDC 3706 Specifications...
Страница 19: ...December 2019 7 LDC 3706 Series Laser Controller...
Страница 20: ...December 2019 8 LDC 3706 Series Laser Controller...
Страница 21: ...December 2019 9 LDC 3706 Series Laser Controller...
Страница 22: ...December 2019 10 LDC 3706 Series Laser Controller...
Страница 52: ...December 2019 40 LDC 3706 Series Laser Controller...
Страница 64: ...December 2019 52 LDC 3706 Series Laser Controller...
Страница 101: ...December 2019 89 LDC 3706 Series Laser Controller...
Страница 118: ...December 2019 106 LDC 3706 Series Laser Controller...