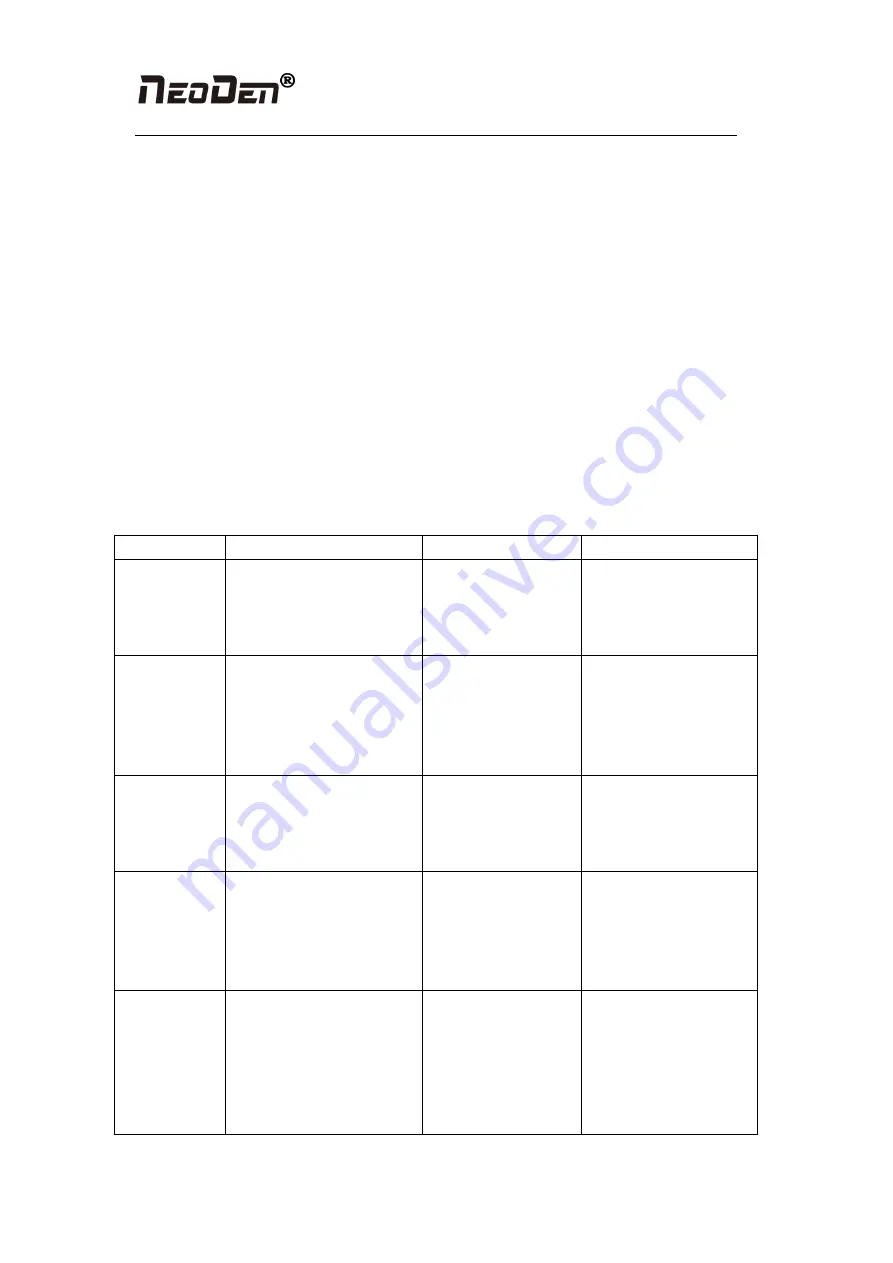
Hangzhou NeoDen Technology Co.,Ltd.
38
graphics and solder graphics should be consistent.
(2) In general, keep unit area amount of solder paste about 0.8 mg/mm². For fine pitch
components, should be 0.5 mg/mm² (using stencil thickness and hole size to control in the
actual operation).
(3) Printed on the substrate of solder paste compared with required value, a certain deviation is
permissible, the covering area of the solder paste on each solder pad should be more than 75%.
(4) Should be no seriously collapsing problem and edges neatly after solder paste had been
printed, the dislocation shouldn’t be larger than 0.2 mm, for solder pad of fine pitch
components, dislocation shouldn’t be larger than 0.1MM, pollution by solder paste is not
permitted to the PCB.
Inspection by 2~5 times magnifier or 3~20 times microscope.
3.5.3.3 The defects of solder paste printing, reasons andsolutions
Excellent printing graphics should be uniform in both vertical and horizontal direction, full,
clean all round, solder paste fill solder pad. Using above such printing graphics device, after
reflow soldering, will get good welding effect then.
Problem
Reason
Issue
Solution
Solder paste
graphics
dislocation
Holes on the stencil not
good match with solder pad;
No enough precision of the
Printing machine
easily cause bridge
connection
Adjust the stencil
position;
Adjust the printing
machine
Solder paste
graphics have
icicles and
dents
Scraper pressure is too
large; Rubber scraper
hardness is not enough;
Holes are too big in the
stencil
Solder paste required
volume is not enough,
easy to appear faulty
soldering; solder joint
strength not enough.
Adjust the printing
pressure; Use metal
scraper; Improved holes
designing in the stencil.
Too much
solder paste
Holes are too big in the
stencil; The gap is too big
between stencil and PCB
easily cause bridge
connection
Check stencil holes size;
Adjust the parameters of
printing, the gap
between PCB and stencil
Graphic
uneven (have
breakpoints)
Holes’ wall is not
smoothness enough; not
wipe residual solder paste in
using for many times;Solder
paste’s thixotropy is bad
Easy cause no enough
solder paste, lead to
the problem such as
faulty soldering.
Wipe the stencil
Contamination
of the graphics
Not wipe residual solder
paste in stencil after using
for many times; Poor
quality of solder paste;
Shake problem when
getting the stencil way
easily cause bridge
connection
Wipe and clean stencil;
replace solder paste;
adjust the machine
Содержание 7
Страница 4: ......