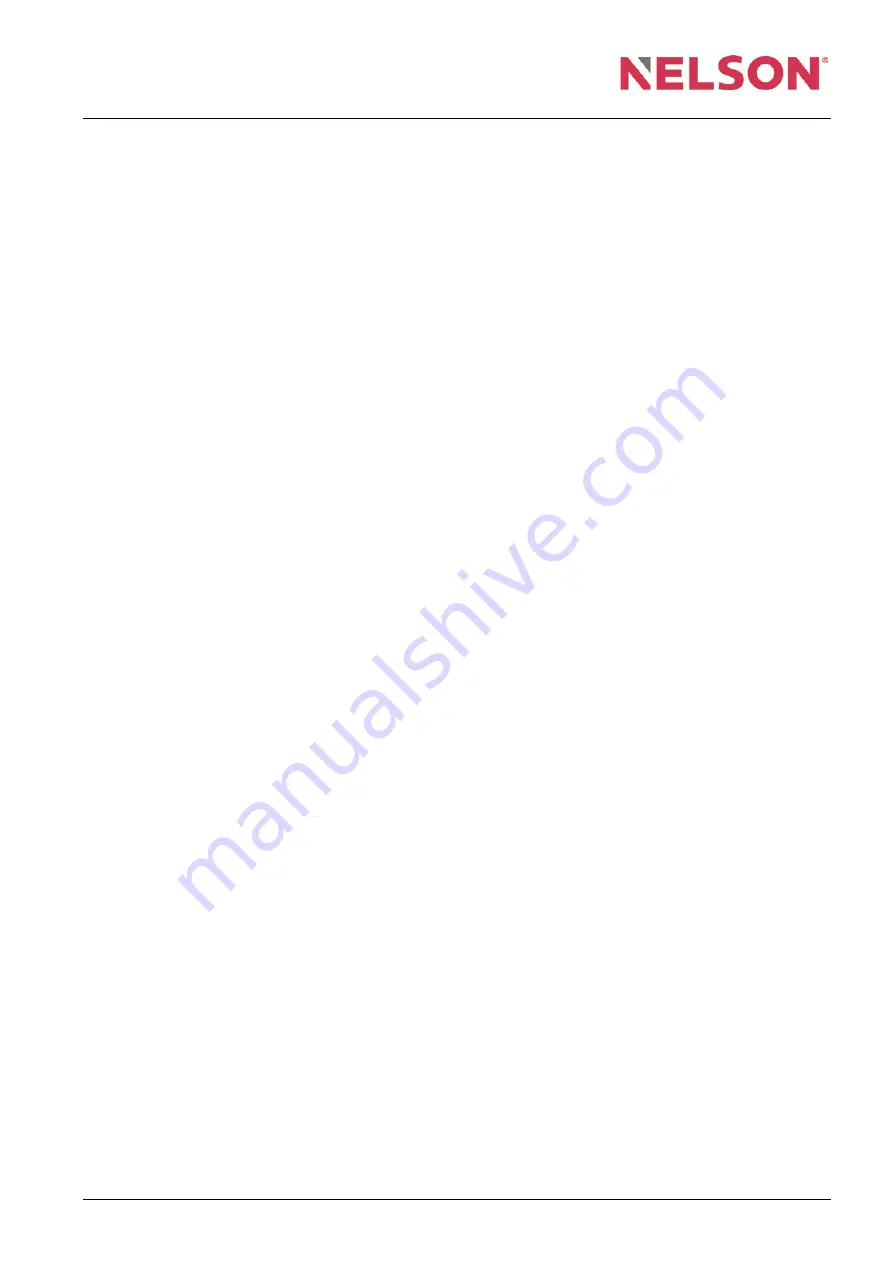
6
Start-up and weld quality check
Page 48
Stud welding units
Operating manual
Date:
July 2021
INTRA 2100/1400
07.2021 / EN
Rev.:
A
6.5.3
Mechanical inspection (general)
If visual inspection has shown some welds to be inadequate, a mechanical inspection
is necessary.
We also recommend this test if you perform a series of test welds to determine the
best settings.
Suitable mechanical testing procedures for work samples (for suitability test, also see
EN ISO 15614-1, 2
*)
) include:
−
Tube bending test,
−
Impact bending test,
−
Tensile test,
−
Folding test,
−
Impact bending test,
−
Notch bending test,
−
Macrosection,
−
Hardness test.
The most commonly used test procedure, even for series work (for simplified work
inspection, also see EN ISO 15614-1, 2
*)
) is the pipe or impact bending test.
A detailed description of these mechanical and technological tests would go beyond
the scope of this operating manual.
Detailed information on this can be found in EN ISO 15614-1, 2.
*)
*)
EN ISO 15614-1, 2: Specification and qualification of welding procedures for metallic materials –
Welding procedure test