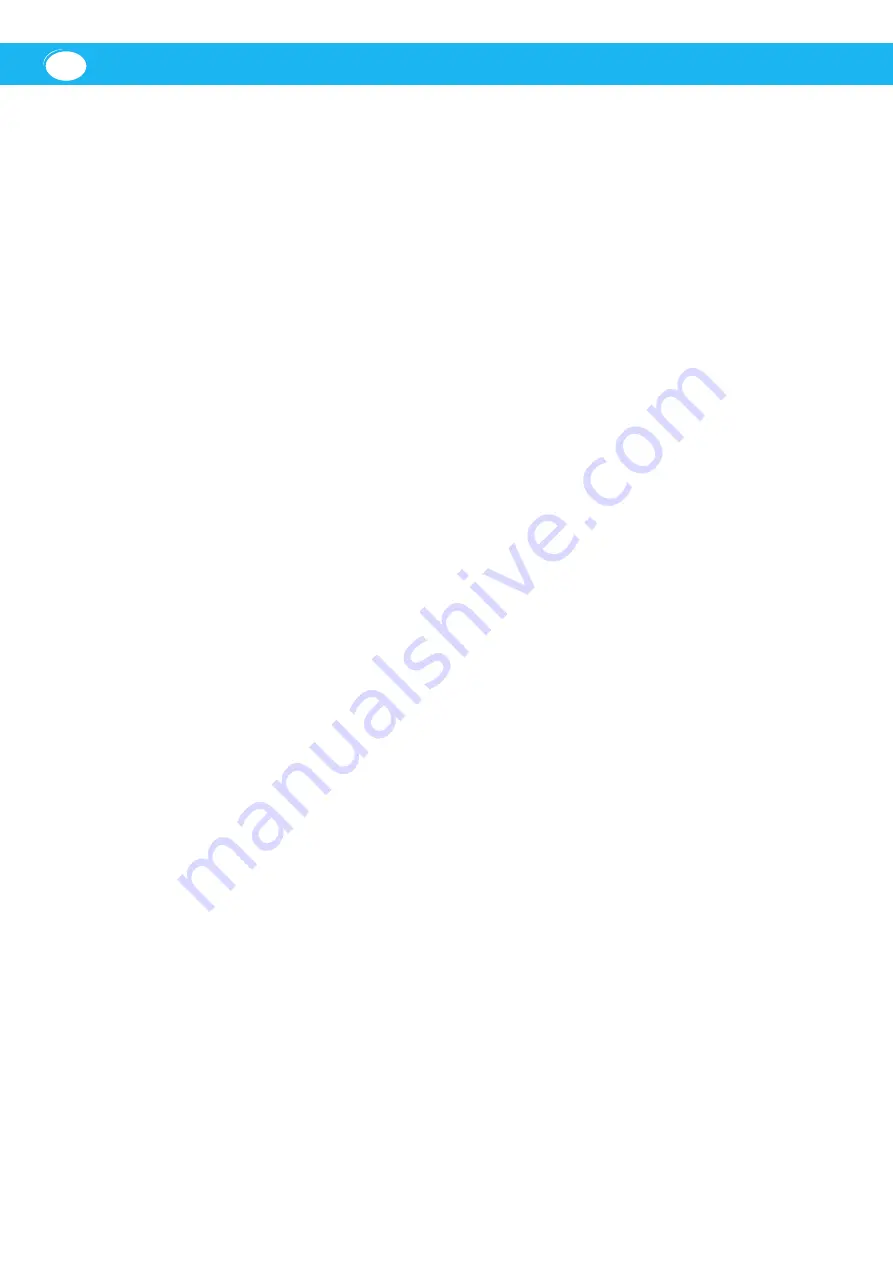
HD100
EN
14
QMM033(02)
phase the material moves outwards along the drum until it comes into contact
with the wedge bar screen (3) or remaining layer of previously accelerated
material. By building up an additional layer of material over the previous layer
the old material is forced to glide over the screen and out from the centrifuge
via the outlet for dry chips (4). During the time the material is exposed to the
centrifugal force the liquid is separated from the solid particles. When the
material passes over the screen the liquid goes through this and out from the
centrifuge via the outlet for liquids (7). This outlet is located immediately
behind the outlet for dry chips.
10 Maintenance
Read Chapter ‘4 Safety’ before carrying out maintenance.
Installation, repair and maintenance work is to be carried out by qualified
personnel using only original Nederman spare parts. Contact your nearest
authorized distributor or Nederman for advice on technical service.
NOTE!
The service intervals in this chapter are based on the unit being
professionally maintained.
10.1 Maintenance instruction
NEDERMAN Swarf Centrifuge is very robust in design but should like every
other production machine be regularly checked and maintained.
Daily checks should be made at the start of operations until a permanent
maintenance schedule can be established. When this has been done only
routine checks and general observations are necessary.
All parts coming into contact with the material which passes through the
centrifuge are subject to wear. Negligent or delayed replacement of worn
parts results in high repair costs and unsatisfactory separating of liquid. A
maintenance schedule should therefore be established which also indicates
when it is time to replace worn parts. This schedule may only be drawn up by
you since wear is highly dependent upon the ingoing chip quality. A basic rule,
however, is to check the screen, drum and housing once a month in the case of
one-shift operations. Inspection takes place via the front door.
10.2 Lubrication
The Swarf Centrifuge has an automatic lubricator for the two roll bearings. The
lubricator is on delivery filled with oil, Shell OMALA EP150 or equivalent.
Check the oil level in the container regularily (once a month) and fill
additionally. Changing of oil must be done every six months during 1-shift
operation.
A grease nipple is situated between the packing rings at the housing.
On delivery Castrol N1-ENTGR-18K (NLGI 2) grease or equivalent has been
used.
The greasing intervals should be adjusted to the operating intensity, there must
always be grease between the packing rings.
EN
Содержание HD100
Страница 2: ...TL2M 2 QMM033 02 HD100 ...
Страница 3: ...TL2M 3 QMM033 02 HD100 Figures 4 English 7 ...
Страница 4: ...HD100 4 QMM033 02 Figures 1 2 ...
Страница 5: ...HD100 5 QMM033 02 3 ...
Страница 6: ...HD100 6 QMM033 02 4 ...
Страница 18: ...HD100 EN 18 QMM033 02 EN ...