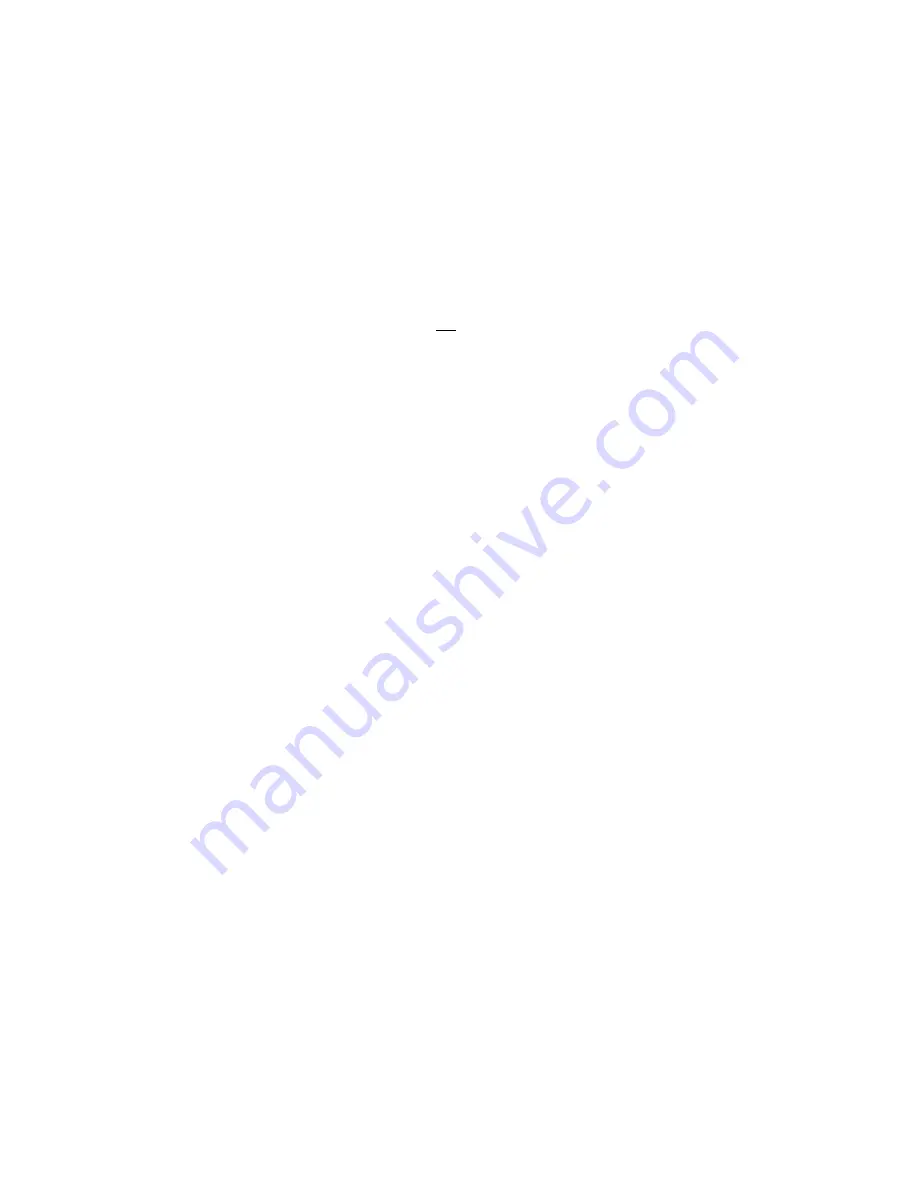
23
23
Look at each of the responses and make a mental note of the differences. These are important
differences in thickness gaging. For example, under the current test setup conditions, if FW (full-
wave rectification) is selected, the lower Amplitude negative cycle appears as the first, or
leading edge of the back echo. By manipulating the gain to cause the T-gate to terminate on the
negative component, then on the positive part, a significant difference in T-readout occurs.
Referring back to the Figure which shows the RF display, a good reason to HW over -
HW or FW is because the first positive going component of the signal has greater amplitude
than does the first negative, produces a "cleaner" display than FW and is less sensitive to
producing Thickness readout changes as a function of gain.
There are other good reasons for offering this variety of display modes. There are instances
where the more prominent half-cycle is not positive-going. In cases where the back wall is lined
with another material (e.g. some elastomers), the first negative-going half-cycle is more
prominent. This phenomenon has to do with the relative acoustical impedance characteristics of
the two materials that make up an interface. Many liquids, elastomers and polymers forming an
intimate interface with metals produce echos whose phase is reversed from that of the metal/air
interface.
The RF display can be referred to if there is any question about which waveform should be se-
lected. For thickness gaging metals much beyond one inch thick, it will be necessary to
"expand" the RF display. If, for example, for a 2 inch thick test specimen, the full-scale range of
the TG400 has been set to a long range, and the RF display is selected, there will be poor detail
in the presentation of the RF.
In order to expand the RF display of the back echo under such condition, delay can be used to
reposition the back echo very near the left side of the A-trace. Then, reducing full-scale range to
0.50 (12.7mm) reproduces the RF of the back echo similar to that of a much thinner test object.
From the MAIN Menu select PROBE and then DAMP. The default value is specific to the
transducer selected, but 50 Ohms is a usually good match for the type of transducer being used
in this example. To observe the effect of damping changes, depress the Up/Dn arrow key and
note a new, higher or Lower damping resistance value displayed. Also note that the IP echos
tend to extend farther at higher damping resistance. Damping changes likewise increase both
the amplitude and shape of the back echo. To observe the effect of damping on the back echo,
cursor up to highlight GAIN. Now, press the left arrow and keep it depressed. You are
controlling the gain (dB). With down and up arrow key adjustments as required, establish the
amplitude of the first back echo at approximately 50% FS (the precise location is unimportant).
Then, return the cursor to DAMP and use the arrow key to once again increase the damping
resistance. Observe the amplitude of the back echo increase, perhaps substantially, with
increased damping resistance. While this effect can be used to advantage under some
conditions, for precision, high resolution thickness gaging, it is usually desirable to select
relatively low damping resistance. With experience, through careful observation of the changing
shapes of the IP and back echo, it is possible to optimize the damping for the job at hand. For
now, return the damping resistance value to 50 ohms, the default value.