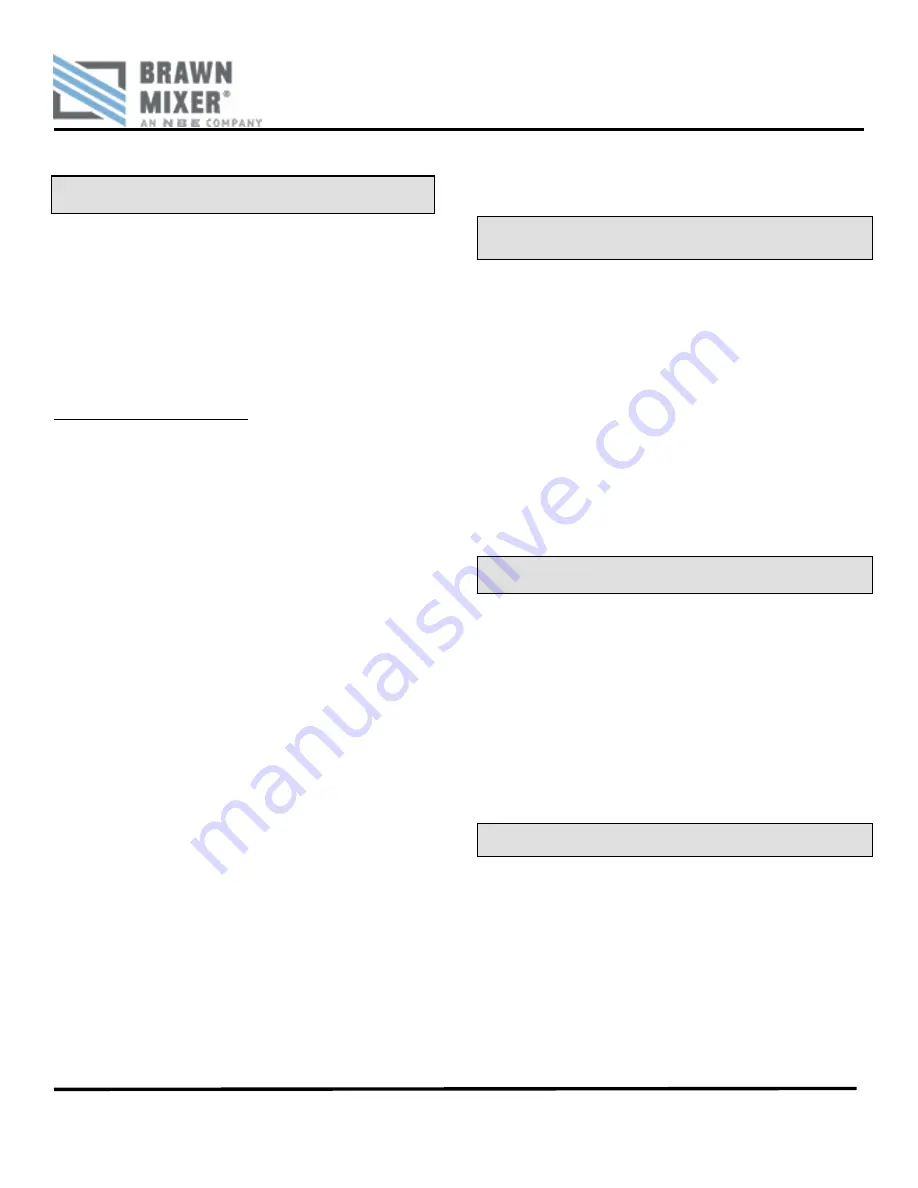
BTR-S
ERIES
O
PERATION
& M
AINTENANCE
M
ANUAL
12838 Stainless Drive, Holland, MI 49424
Phone: 616/399-5600 Fax 616/399-3084
Copyright 2018 BRAWN Mixer
www.BRAWNMIXER.com
Page 9 of 9
11/27/2018
WARRANTY
WARRANTY
: All equipment or parts covered by this
manual are guaranteed free from defective material and
workmanship for a period of twelve (12) months from
date of shipment, under normal use and service. This
warranty does not cover failure of normal wear parts
unless the failure of such part has resulted from
defective material and workmanship. BRAWN Mixer will
repair or replace, at its option, any equipment which has
been found to be defective and is within the warranty
period, provided that the equipment is shipped, with
previous factory authorization, freight prepaid, to
BRAWN's plant in Holland, Michigan, USA. All return
shipments are made FOB BRAWN's factory. BRAWN is
not responsible for removal, installation, or any other
incidental expenses incurred in shipping the equipment
to or from BRAWN. In the case of components
purchased by BRAWN Mixer and incorporated in the
equipment, the component manufacturer's guarantee
shall apply. NOTE: Any modifications or corrective work
done to the equipment which were not specifically
authorized in writing by BRAWN Mixer shall void this
limited warranty, and BRAWN Mixer shall accept no
liability for any of the corrective work or expenditures
which were conducted without their prior, written
authorization. BRAWN Mixer shall not be held liable for
any further cost, expense, or labor to replace equipment
or replaceable parts, or indirect or consequential
damages.
With the exceptions of the limited warranty set out
above, there are no other understandings, agreements,
representatives, or warranties implied (including any
regarding the merchant-ability or fitness for a particular
purpose), not specified herein, respecting this agreement
or equipment, hereunder. This contract states the entire
obligation of BRAWN Mixer in connection with this
transaction.
SHOULD WE MAKE A MISTAKE...
BRAWN Mixer's
Direct Returns Policy
To ensure proper handling of your return, please take a
moment to read the following:
ALL
returns require a
RETURN GOODS
AUTHORIZATION (RGA) NUMBER
. We are unable
to process your return or issue proper credit without
an approved
RGA
number.
ALL
returns must be
COMPLETE
, including all
original warranties, manuals, documentation and
packaging.
ALL
product must be received within 14 days of
issuing an
RGA
number.
How to Return Product
You must have a
RETURN GOODS AUTHORIZATION
(RGA)
number before you return any product to BRAWN
Mixer. To obtain this number, call
616/399-5600
and ask
for Customer Service. Be sure to have available the
following information:
your order number
the BRAWN product serial number
the part number and description of the product
the reason for the return
♦
I M P O R T A N T
♦
The Return Goods Authorization number must be written
clearly on all boxes being returned. C.O.D. shipments will
not be accepted.
Содержание BRAWN MIXER BTR 1 Series
Страница 2: ... THIS PAGE IS INTENTIONALLY LEFT BLANK ...
Страница 3: ......
Страница 4: ......
Страница 30: ... THIS PAGE IS INTENTIONALLY LEFT BLANK ...
Страница 31: ... THIS PAGE IS INTENTIONALLY LEFT BLANK ...
Страница 32: ......