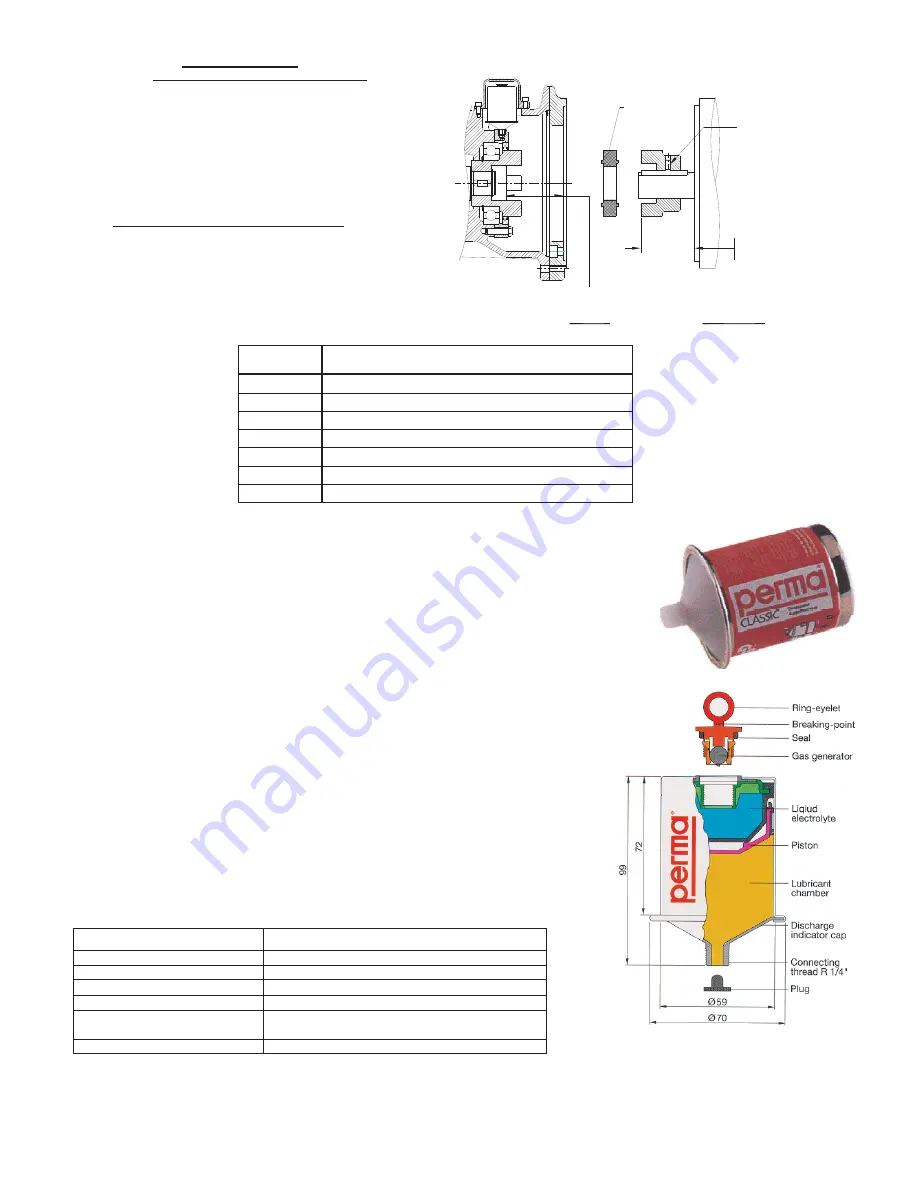
BIM 1009/2007/09
Page 3 of 8
www.nord.com
Jaw” Style Coupling
NEMA C-face Installation Instructions
1.
Measure the distance from the face of the input adapter to the
face of the coupling as shown and record that measurement.
2. Subtract the “X” dimension from the measured distance.
This needs to be done so that the coupling will not be
preloaded after installation!
3.
Use that measurement to locate the coupling from the face of
the motor onto the shaft.
4.
The metal portion of the coupling should be heated up prior to
assembly, generally 250
q
F to 300
q
F (120
q
C to 150
q
C).
*DO NOT HEAT THE URETHANE SPIDER.
5.
Once in place, tighten the setscrew to lock coupling in place.
Let the coupling cool down before placing the spider into the
jaws. It is recommended that the key is staked or bonded
(Loctite) in place to prohibit the key from vibrating out.
6. Mount the motor onto the input adapter with customer
supplied bolts. Make sure that the coupling from the adapter
and the motor engage securely. Use lock washers or Loctite
to prohibit bolts from becoming loose from vibration.
Automatic Lubricator
NORD Gear supplies the larger C-face motor adapters with an Automatic Lubricator. This will provide
additional grease lubrication to the outboard bearing. As the pressure from the lubricator canistor pushes
the new grease into the bearing, the old grease will flow into the cavity towards the gearbox. When the
cavity is filled with the "used" grease, the pressure from the new grease pushes the used grease into the
gear box thru the input seal. The old grease mixes with the oil but will not cause harm to the gearing or
bearings. Regular oil changes with the gearbox will remove the old grease which has been pushed into
the gearbox. Refer to the PARTS LISTS for inputs equipped with the Automatic Lubricator.
Principle of Operation
After tightening the plastic activating screw, the Zinc-Molybdenum pellet drops into the Citric
Acid electrolyte. The chemical reaction builds up pressure that causes the piston to move
forward. The lubricant is continuously injected into the lubrication point. At the end of the
lubrication period, the discharge indicator cap becomes clearly visible indicating the lubricant
has been fully discharged. The lubrication period is determined and defined by the color of the
activating screw.
For the bearings used in NORD Gear products, a 12-month lubrication period is standard,
indicated by a
gray activating screw
. This applies for an average operating time of 8
hours/day. For longer operating times, the replacement interval decreases to 6 months.
Lubrication canisters are also available for cold temperature applications. Contact NORD Gear
for more information.
Assembly Instructions
1.
Remove the plug from the male connecting thread.
2.
Screw male fitting into bearing housing within Input Adapter.
3.
Insert activating screw into end of canister. Tighten until the ring-eyelet breaks off.
4.
Replace every twelve months.
Perma Classic Specifications
Standard Lubricant
Klüber Petamo GHY 133 (synthetic)
NORD Part Number
28301000
Lubricant Volume
120 mL (4 oz.)
Operating Temperature Range
º
-30
q
C to 150
q
C (-22
q
F to 302
q
F)
Discharge Time
12 months at 25
q
C (77
q
F)
Operating Position
Independent of mounting position, operates even
under water.
Male Connecting Thread
1/4” NPT
º
The temperature range shown is for the Perma Classic Lubricator only and does
not apply to other components and/or lubricants within the gear reducer.
Coupling
Size
“X”
(Subtract this value from measured distance)
R14 0.06”
(1.5mm)
R19 & R24
0.08” (2.0mm)
R28 0.10”
(2.5mm)
R38/42 0.12”
(3.0mm)
R48 0.14”
(3.5mm)
R65 0.18”
(4.5mm)
R90 0.22”
(5.5mm)
SPIDER
URETHANE
SUBTRACT
DISTANCE
COUPLING
PLACEMENT
DISTANCE
DISTANCE
COUPLING PLACEMENT
- "X" (see table) =
C-
F
ACE
M
O
T
O
R
DISTANCE
MEASURED
SET SCREW
TIGHTEN
Содержание Brawn mixer BTO Series
Страница 2: ...THIS PAGE IS INTENTIONALLY LEFT BLANK...
Страница 4: ......
Страница 6: ......
Страница 36: ...THIS PAGE IS INTENTIONALLY LEFT BLANK...
Страница 37: ...THIS PAGE IS INTENTIONALLY LEFT BLANK...
Страница 38: ...THIS PAGE IS INTENTIONALLY LEFT BLANK...
Страница 39: ...THIS PAGE IS INTENTIONALLY LEFT BLANK...
Страница 40: ......