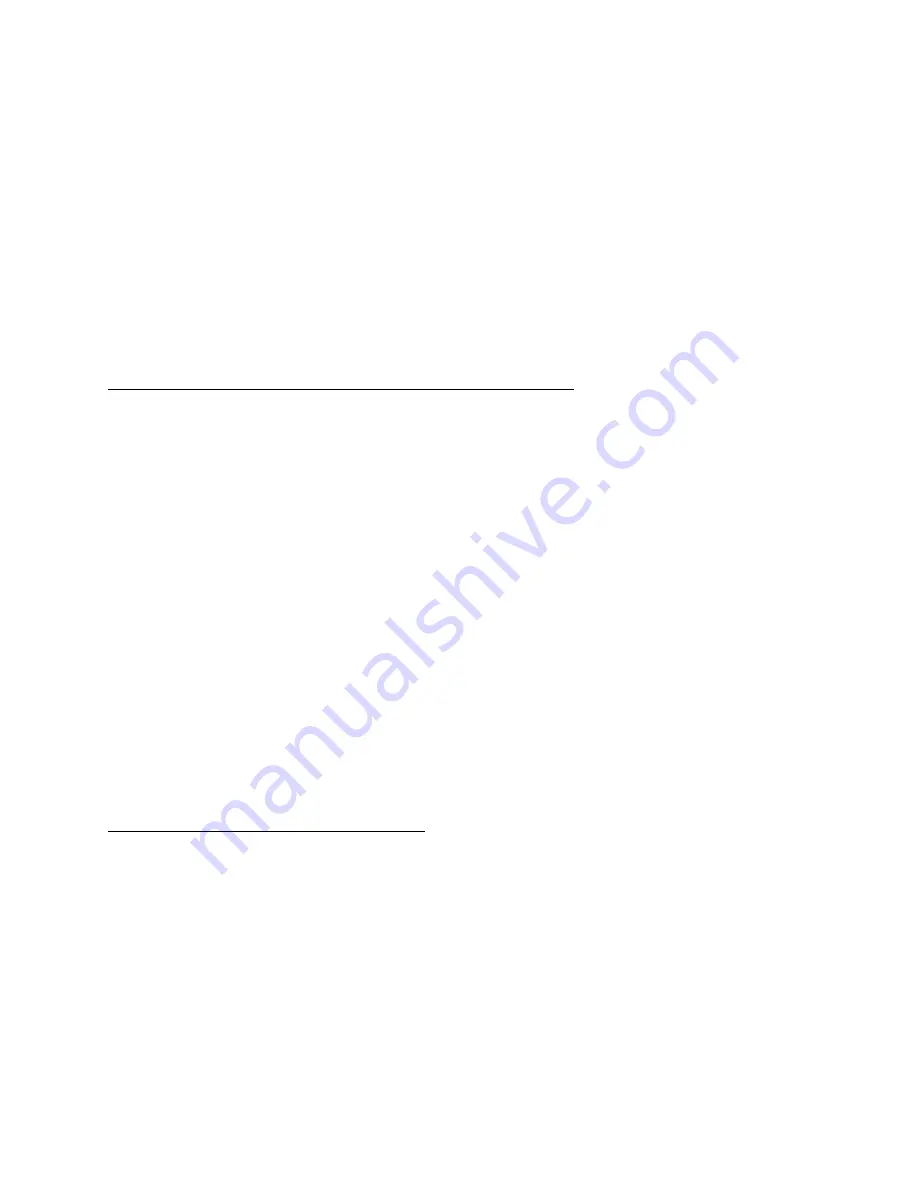
- 8 -
CHECKOUT
Do not use just a battery charger by itself to supply the power for testing your autopilot.
The voltage out of one of these has too much ripple. Connect a battery charger to the
aircraft battery and leave it on whenever using the servo. Otherwise the 1 amp drain of
the servo can pull the battery voltage below 12 volts and cause improper operation.
See Fig. 1 for a view of the AP-1 controls. Flip the Mode Switch on the AP-1 to the right
for Wing Leveler mode and turn on the aircraft master switch. The gyro should start to
wind up, and the servo should crank to a stop somewhere.
CHECK DIRECTION OF CRANK ARM ROTATION
CAUTION: The trimpots (item 5 in Fig. 1) to be adjusted in the following procedures
turn quite easily. If a pot resists rotation, do not force it—it probably is already turned as
far as it will go in that direction. The counterclockwise rotational limit is around 8 or 9
o'clock and the clockwise rotational limit is around 3 or 4 o'clock.
The GYRO NULL trimpot is factory set and should not need adjustment. But if you do
turn it by accident, just use a voltmeter to set the voltage between pins 10 and 11 on the
rear connector of the AP-1 to zero, or as close to zero as you can get it-the voltage may
wander a few millivolts. Make sure that your voltmeter—digital preferred—is set on its
most sensitive scale. Also, the cover of the AP-1 must be on (there is light sensitive
circuitry inside the instrument) and the AP-1 must be held still for this adjustment.
Set the SPAN trimpot fully clockwise. Rotate the TURN CONTROL for a right turn, and
note the direction of crank arm rotation. When the pushrod is installed, this rotation must
deflect the ailerons for a right roll.
If the aileron deflection is backwards, you must reverse the direction of servo rotation.
See Fig. 3 on the next page. Swap the motor wires at the motor. Swap end connections at
the FEEDBACK pot-these wires are white with red tracer and white with black tracer. If
necessary, reset servo null point.
RESETTING SERVO NULL POINT
When you turn the servo on after reversing the servo direction, or after changing the
orientation of the crank arm by 180 degrees, the servo may drive into its mechanical limit
and just keep grinding, slipping the clutch. This happens because the null point to which
the servo is trying to go has been moved to a position outside the range of servo travel.
To fix this, do the following:
Содержание AP-1
Страница 2: ......
Страница 9: ...7 WIRING DIAGRAM FOR HAND HELD GPS AND AP 1 WITH GPS COUPLER WIRING DIAGRAM Fig 3...
Страница 27: ...A 3...