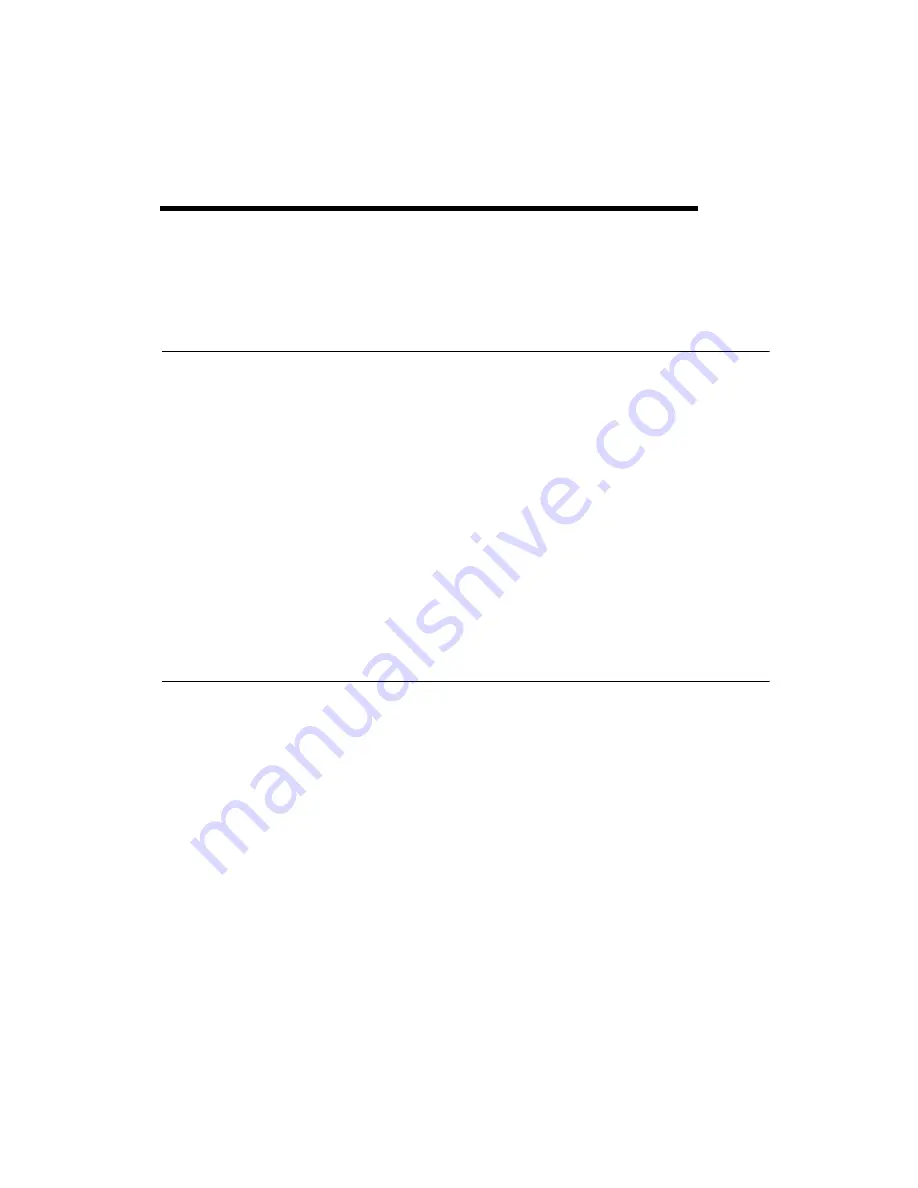
©
National Instruments Corporation
2-1
2
Hardware Overview
Digital I/O
The digital I/O on the NI 8255R is accessible through 2 TTL inputs, 10 TTL
outputs, 13 isolated inputs, and 4 isolated outputs.
You can use input signals as triggers, product selection ports, or to read
quadrature encoders. Uses for output signals include controlling camera
reset and exposure, controlling strobe lighting, outputting inspection
results, or communicating with PLCs. You can also define the functions of
digital input and output signals.
For information about how to use LabVIEW to implement specific digital
I/O functions, refer to the examples at
<LabVIEW>\examples\IMAQ\
IMAQ IO.llb,
where
<LabVIEW>
is the location in which LabView is
installed. For information about how to use C, Visual Basic, or .NET to
implement specific digital I/O functions, refer to the examples at
<National Instruments>\NI-IMAQ IO\Examples
.
RIO and the LabVIEW FPGA Module
Behind the digital I/O of the NI 8255R is an FPGA which has been
preconfigured with the functionality required for most common machine
vision tasks. However, if the factory configured functionality does not
fulfill your requirements, the FPGA is user-configurable with the
LabVIEW FPGA Module. RIO allows you to develop custom FPGA
logic to add triggering, pulse-width modulation signals, or custom
communications protocols to your machine vision application.
Using National Instruments RIO hardware and the LabVIEW FPGA
Module, you can define your hardware without in-depth knowledge of
hardware design tools or hardware description languages (HDL). When
the signal requirements change, the LabVIEW code can be modified and
downloaded to the FPGA to change the I/O mix or type. This flexibility
allows you to reuse the same hardware and software at no extra expense.