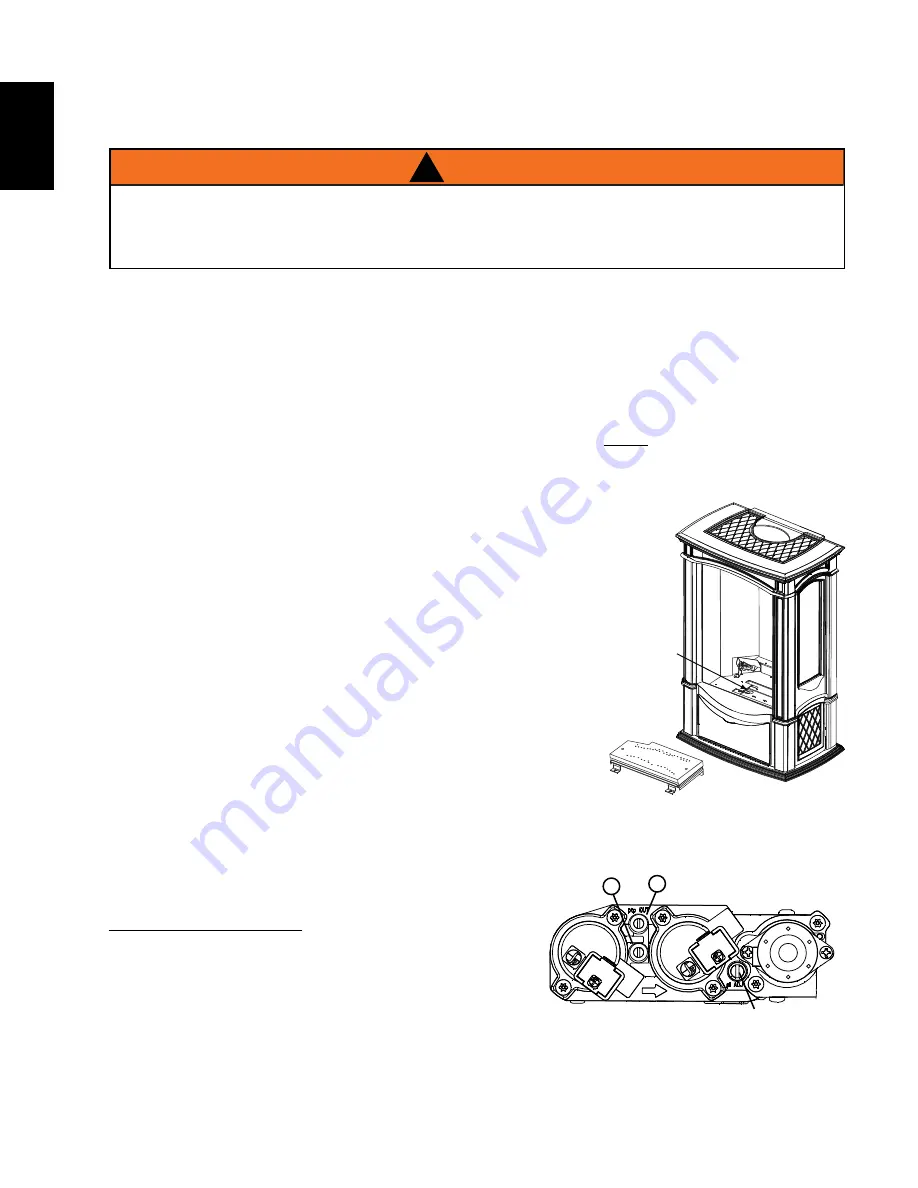
W415-2183 / B / 02.10.17
40
EN
9.0 ADJUSTMENTS
9.1 PILOT INJECTOR AND ORIFICE REPLACEMENT
BURNER
ASSEMBLY
ORIFICE
LOCATION
A.
Turn off the electrical and gas supply to the appliance.
B.
Remove the cast front, glass viewing door and log set.
C.
Remove the 2 securing screws. Slide the burner assembly to the right and lift out.
D.
Using a deep socket wrench, remove the main burner orifice. A back-up wrench must be used
on the manifold, located below the housing to ensure that the aluminum tubing does not twist
or kink. Replace the correct burner orifice using pipe thread compound.
E.
Loosen nut and replace with appropriate injector
F.
Reinstall the burner ensuring that the Venturi tube fits over the orifice. NOTE: Check and
adjust, if necessary, the primary air to 3/8” (10mm) for propane and 3/16” (5mm) for
natural gas. Replace the screws.
G.
Turn on the gas supply and check for gas leaks by brushing on a soap and
water solution.
DO NOT USE OPEN FLAME.
H.
Replace the log set. Then light the pilot and main burner to ensure that the gas
lines have been purged.
I.
Replace the glass viewing door and cast front. Turn on the electrical supply to
the appliance.
Purge all gas lines with the glass door removed. Assure that a continuous
flow is at the burner before re-installing the door.
!
WARNING
THIS INSTALLATION SHOULD BE DONE BY A QUALIFIED INSTALLER AND SHALL BE IN COMPLIANCE
WITH LOCAL CODES. IN THE ABSENCE OF LOCAL CODES, USE THE CURRENT CAN1-B149
INSTALLATION CODE IN CANADA, OR THE CURRENT NATIONAL FUEL GAS CODE ANSI Z223.1 IN
THE UNITED STATES.
Adjust the pilot screw to provide properly sized fl ame. Turn in a
clockwise direction to reduce the gas fl ow.
Check Pressure Readings:
Inlet pressure can be checked by turning screw (A) counter-
clockwise 2 or 3 turns and then placing pressure gauge tubing
over the test point. Gauge should read as described on the chart
below. Check pressure with main burner operating on “HI”.
Outlet pressure can be checked the same as above using
screw (B). Gauge should read as described on the chart
below. Check pressure with main burner operating on “HI”.
AFTER TAKING PRESSURE READINGS, BE SURE TO
TURN SCREWS CLOCKWISE FIRMLY TO RESEAL. DO
NOT OVERTORQUE.
Leak test with a soap and water solution.
Prior to pilot adjustment, ensure that the pilot assembly
has not been painted. If overspray or painting of the pilot
assembly has occurred remove the paint from the pilot
assembly, or replace. Fine emery
cloth or a synthetic scrub pad (such as
Scotch-Brite™) can be used to remove
the paint from the pilot hood, electrode
and fl ame sensor.
*Maximum inlet pressure not to exceed 13”.
39.1E
A
B
PILOT SCREW
3/8” - 1/2”
(9,5mm - 12,7mm)
FLAME MUST ENVELOP
UPPER 3/8” (9.5mm) TO 1/2”
(12.7mm) OF FLAME SENSOR
PILOT
BURNER
ELECTRODE
FLAME
SENSOR
LA FLAMME DOIT
ENVELOPPER LA PARTIE
SUPÉRIEURE DE LA SONDE
DE FLAMME DE 3/8” (9,5mm)
À 1/2” (12,7mm)
ÉLECTRODE
LA SONDE
DE FLAMME
VEILLEUSE
3/8” - 1/2”
(9.5mm - 12.7mm)
Pressure
Inlet
Outlet
Natural Gas
(inches)
Natural Gas
(millibars)
Propane
(inches)
Propane
(millibars)
*7"
(MIN. 4.5”)
3.5"
13"
(MIN. 11")
10"
17.4mb
(MIN. 11.2mb)
8.7mb
32.4mb
(MIN. 27.4mb)
24.9mb
9.2 PILOT BURNER ADJUSTMENT
Содержание GDS26P-1
Страница 51: ...W415 2183 B 02 10 17 51 EN 15 0 SERVICE HISTORY 43 1...
Страница 105: ...16 0 NOTES 44 1 FR W415 2183 B 02 10 17 105...