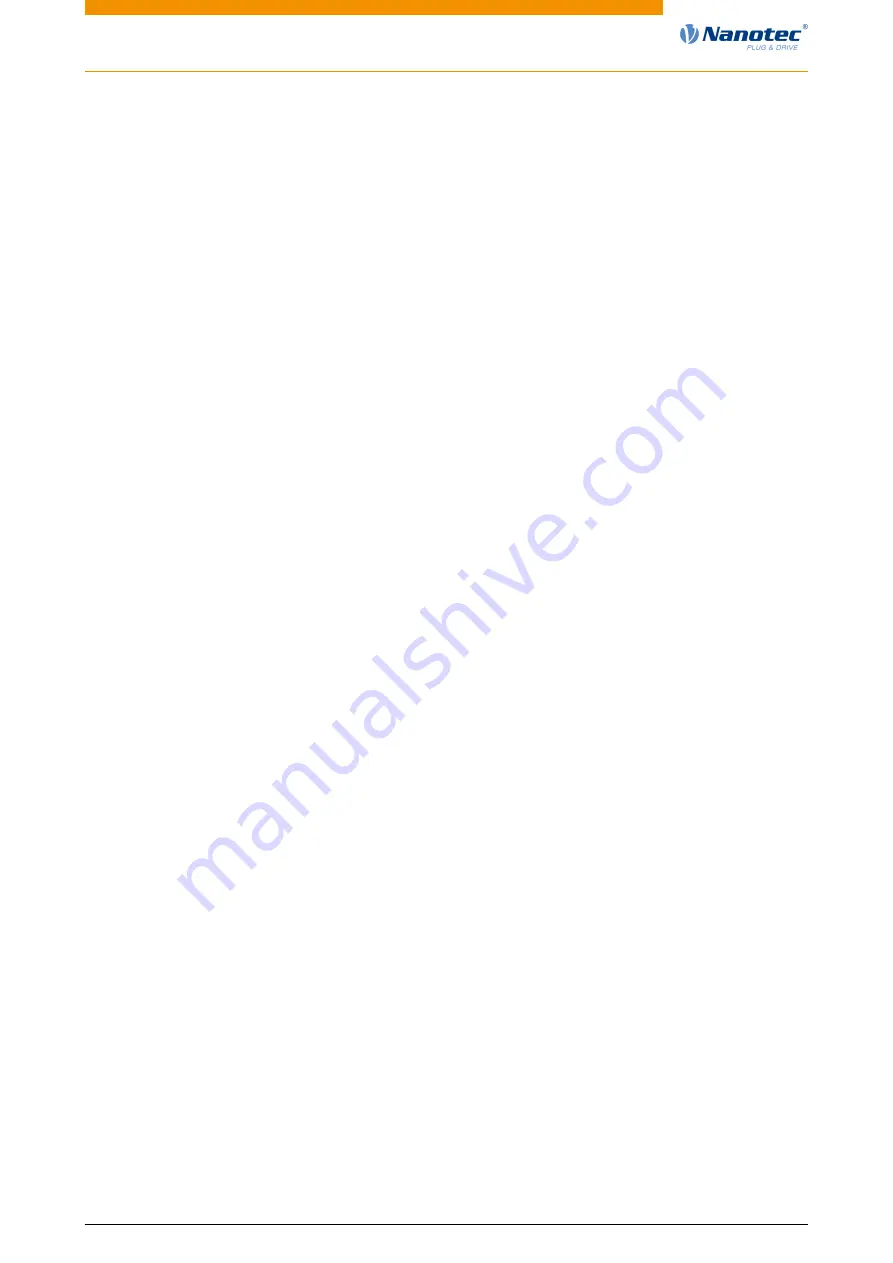
Technical Manual N5 (CANopen)
4 Commissioning
1. Connect the CANopen master to the controller via the CAN- and CAN+ cables. Check the
connection of your CAN-GND and that the necessary 120 ohm termination resistor is present
between CAN+ and CAN-.
2. Supply the controller with voltage.
3. Change the configuration values if necessary, see Configuration via CANopen.
The controller is set per default to node-ID 1, baud rate 1 Mbaud.
4. To test the interface, send bytes
40 41 60 00 00 00 00 00
to the controller.
Statusword (6041
h
) was read; you receive this response:
4B 41 60 00 XX XX 00 00
.
4.3 Setting the motor data
Prior to commissioning, the motor controller requires a number of values from the motor data sheet.
•
Number of pole pairs: Object 2030
h
:00
h
(pole pair count) The number of motor pole pairs is to be
entered here. With a stepper motor, the number of pole pairs is calculated using the step angle,
e.g., 1.8° = 50 pole pairs, 0.9° = 100 pole pairs (see step angle in motor data sheet). With BLDC
motors, the number of pole pairs is specified directly in the motor data sheet.
•
Setting the motor current / motor type:
•
Stepper motor only: Object 2031
:00
h
: Rated current (bipolar) in mA (see motor data sheet)
•
Object 2031
h
:00
h
: Rated current (bipolar) in mA (see motor data sheet)
•
Object 3202
h
:00
h
(Motor Drive Submode Select): Defines motor type stepper motor, activates
current reduction on motor standstill: 0000008h. See also chapter Commissioning open
loop.
•
BLDC motor only:
•
Object 2031
h
:00
h
Peak current in mA (see motor data sheet)
•
Object 203B
:01
h
Rated current in mA (see motor data sheet)
•
Object 203B
:02
h
Maximum duration of the peak current in ms (for initial commissioning, a
value of 100 ms is recommended; this value is to be adapted later to the specific application).
•
Object 3202
h
:00
h
(Motor Drive Submode Select): Defines motor type BLDC: 00000041h
•
Motor with encoder: Object 2059
:00
h
(Encoder Configuration): Depending on the encoder version,
one of the following values is to be entered (see motor data sheet):
•
Supply voltage 5V, differential: 00000000h
•
Supply voltage 24V, differential: 00000001h
•
Supply voltage 5V, single-ended: 00000002h
•
Supply voltage 24V, single-ended: 00000003h
•
Motor with brake: Object 3202
:00
h
(Motor Drive Submode Select): The brake control is activated
for the initial commissioning. Depending on the specific application, this configuration can be
deactivated later if necessary. One of the following values is to be entered depending on the motor
type:
•
Stepper motor, brake control (and current reduction while at standstill) activated: 0000000Ch
•
BLDC motor, brake control activated: 00000044h
4.4 Connecting the motor
After setting the motor parameters, see Setting the motor data, connect the motor and, if applicable,
the present sensors (encoders / Hall sensors) and the brake.
•
Connect the motor:
•
to connection X5, see Connector X5 – motor connection
•
Connect encoders / Hall sensors:
•
to connection X2, see Connector X2 – encoder/Hall sensor
•
Connect the brake:
Version: 2.0.1 / FIR-v1650
36