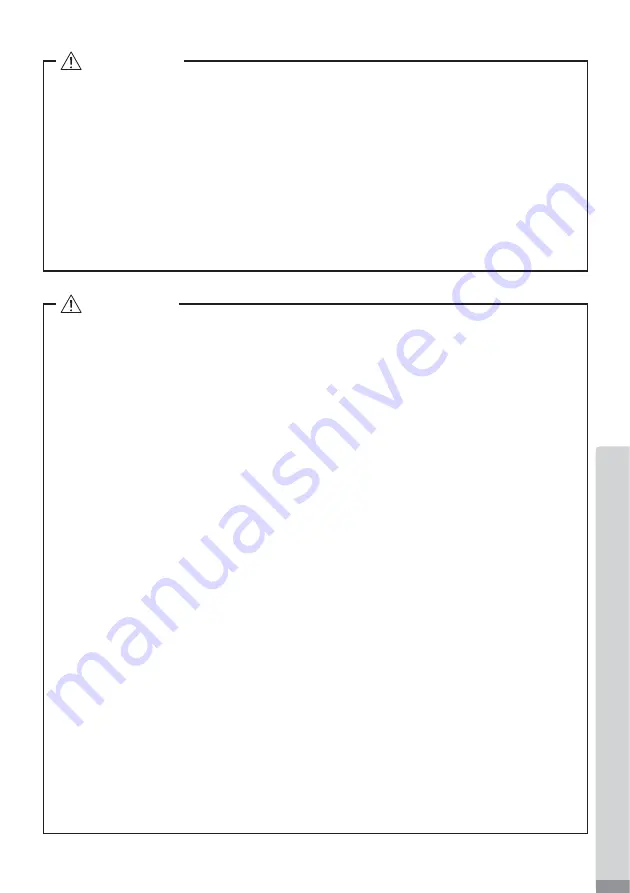
19
ENGLISH
⑩
Ensure that of the collet holder is correctly mounted in the Spindle before
rotating the Spindle.
⑪
Do not use bent, broken, chipped, out of round or sub-standard tools, as
this may cause them to shatter or explode. Tools with fractures or a bent
shank will cause injury to the operator. When using a new tool, rotate it in
a low speed and increase speed gradually for safety.
⑫
Do not exceed the maximum recommended allowable tool speed. For your
safety, use speeds below the maximum allowable speed.
⑬
Do not apply excessive force. This may cause tool slippage, tool damage,
injury to the operator or loss of concentricity and precision.
WARNING
①
Do not drop or hit this Spindle, as shock can damage to the internal
components.
②
Protect the collet holder taper from the ground particles, dust, metal chips
or coolant spray when using the automatic tool change in the machine.
Should ground particles, dust, metal chips or coolant spray adhere to
the taper, remove them with an air blow before they are inserted into the
spindle.
③
Make sure the inner face of the Spindle and the taper surface of the collet
holder are clean (Clean them if debris is found) before replacing the collet
holder.
Ground particles or metal chips stuck to the surface will cause run-out or
damage to the collet and spindle. Loss of concentricity will cause spindle
damage due to the lack of precision.
④
When cleaning a Spindle, stop the brushless motor and remove debris with
a soft brush or a cloth. Do not blow air into the dust proof cover area (refer
to contents of page number P23 " 6 - 2 Outside View " ) with compressed
air as foreign particles or cutting debris may get into the ball bearing.
⑤
When replacing the tool, make sure the tool shank, collet, collet nut, and
inner face of the collet holder are clean. If ground particles or metal chips
stick to the inside of the collet, damage to the collet holder or spindle can
occur due to the loss of precision.
⑥
Always clean the tool shank before installing the tool in the Spindle.
⑦
When sizing the correct collet size to the tool shank diameter, a tolerance
of +0
〜
- 0.01mm is strongly recommended. A tool shank within the +0
〜
- 0.1mm range is mountable, however, this may cause poor concentricity
and or insuf
¿
cient tool shank gripping force.
⑧
Select suitable products or tools for all applications. Do not exceed the
capabilities of the Spindle or tools.
CAUTION