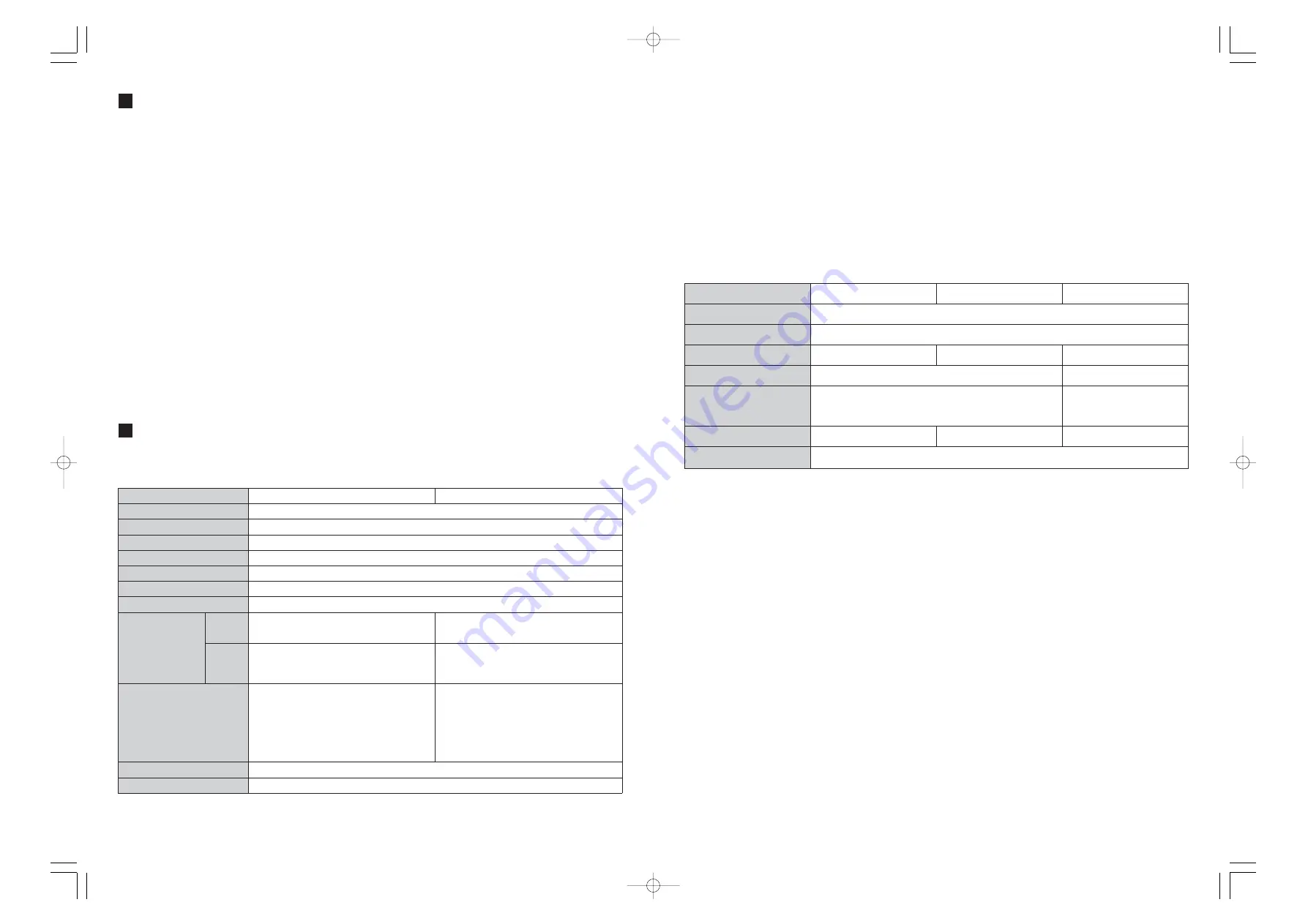
(1) Control Unit
5
6
SPECIFICATIONS
(1) The E3000 system is designed to be mounted in a CNC lathe, robot, NC lathe or special
purpose machine for drilling, milling, slitting, grinding or other similar application.
(2) A high-speed brushless motor is used to achieve a maximum speed of 60,000 min
-1
and
eliminate the nuisance of brush maintenance.
(3) Speed control and protection functions utilize a high performance microprocessor.
(4) Automatic control and monitoring of spindle functions are possible.
(5) Wide speed range, 1,000-60,000 min
-1
makes high precision machining possible.
(6) Compact control unit design allows easy installation in space restricted machines.
Connectors and control panel are front mounted for easy access.
(7) Control Unit is capable of being connected to AC100V to 240V power sources.
(8) Two types of control units are available. Standard type NE211 and NE211-OP1 which
conforms to European standards for safe, automatic machine operation.
(9) Gear Mode Select Switch installed. Set Gear Mode to display the rotating speed at the
cutting tool when using an angle spindle or speed reducer.
(10) The motor/spindle housing is made of Stainless Steel (SUS-416), precision ground to 20,
25 or 30mm making the motor/spindle very versatile and easy to mount on NC or special
purpose machines.
(11) Installation and motor replacement for the E3000 system is very simple because the
connector is placed at the rear of the motor.
*
Note2 <NE211-OP1 Features>
•
The installed Safety Relay is designed to comply with EN standards, ‘a’ contacts switch the Motor Power Line
and ‘b’ contacts switch the external outputs to the machining center’s controller.
•
The Safety Relay utilizes Normally Open contacts. The Emergency Stop Signal lines must be supplied with
power to hold the Safety Relay contacts closed and allow the control unit to supply power to the motor. Any
system errors, trouble with the machining center or the connections between the E3000 control unit and the
machining center’s controller will cause the relay contacts to open and the E3000 motor to stop.
•
The Emergency Stop Signal Input can be connected to any and all portions of the machine’s safety systems to
stop the E3000 motor any time that stoppage of the spindle and motor is required.
•
The ‘b’ contact outputs can be used to detect an open circuit on the motor line and integrated with the
machines safety systems to stop the machine in case of trouble. If the ‘a’ contacts of the Safety Relay are
welded together by an over load or short circuit the ‘b’ contacts’ separation is maintained at more than 0.5mm
spacing by the relay’s spring release mechanism.
3-1 Specifications
*
Note1 :
Protectively Separated
FEATURES
(2) Motor Spindle
*
Note :
Collet Chucks are sold separately. Please specify the desired Collet Chuck size when ordering.
CHA-[][] : ø0.5mm-ø4.0mm in 0.1mm increments and ø2.35mm, ø3.175mm
CHK-[][] : ø0.5mm-ø6.0mm in 0.1mm increments and ø2.35mm, ø3.175mm, ø6.35mm
*
Caution! :
Control Limitation of Motor Speed
The fllowing motor is automatically controlled the speed.
So,please check the specification of the Motor Spindle prior to use.
For EM25N-5000,EM25-5000 : 1,000-50,000min
-1
For EM-3030J
: 1,000-32,000min
-1
2
3
Model
NE211
NE211-OP1
*
Note2
Input
AC100V-240V, 50/60Hz, 1PHASE, 1.8A
Output
AC33V, 0-1KHz, 3PHASE, 2.4A
Operating Temperature
0-40°C
Ambient Humidity
MAX. 85%
Over Voltage Category
Ⅱ
Pollution Degree
2
Speed Range
1,000-60,000 min
-1
Control Signal
Input
*
Note1
Transistor Activation Connections : 6
Analog Connections : 1
Transistor Activation Connections : 9
Analog Connections : 1
Output
*
Note1
Transistor Activation Connections : 9
Analog Output Connections : 3
Transistor Activation Connections : 9
Relay Contact Connections : 2
Analog Output Connections : 3
Protection Circuits
Over-Voltage, Over-Current,
Over Load, Sensor Malfunction,
Overheat, Brake Malfunction,
Spindle Lock, Low Air Pressure,
Start-Up Error, Over-Speed
Over-Voltage, Over-Current,
Over Load, Sensor Malfunction,
Overheat, Spindle Lock,
Brake Malfunction, Low Air Pressure,
Start-Up Error, Over-Speed,
Emergency Stop Circuit
Weight
2.8kg
Dimensions
W88 x D138 x H238 mm
Model
EM20-S6000
EM25-S6000
EM30-S6000
Speed Range
60,000 min
-1
Spindle Accuracy
Within 1µm
Diameter
ø20 mm
ø25 mm
ø30 mm
Max. Output
250W
350W
Collet Chuck
(Optional)
*
Note
CHA-[][]
CHK-[][]
Weight (W/O Motor Cord)
230g
375g
575g
IP Rating
IP64 (If not using cooling air rating is IP40)
E3000C̲K0446E̲e̲080108 08.1.8 6:34 PM ページ5