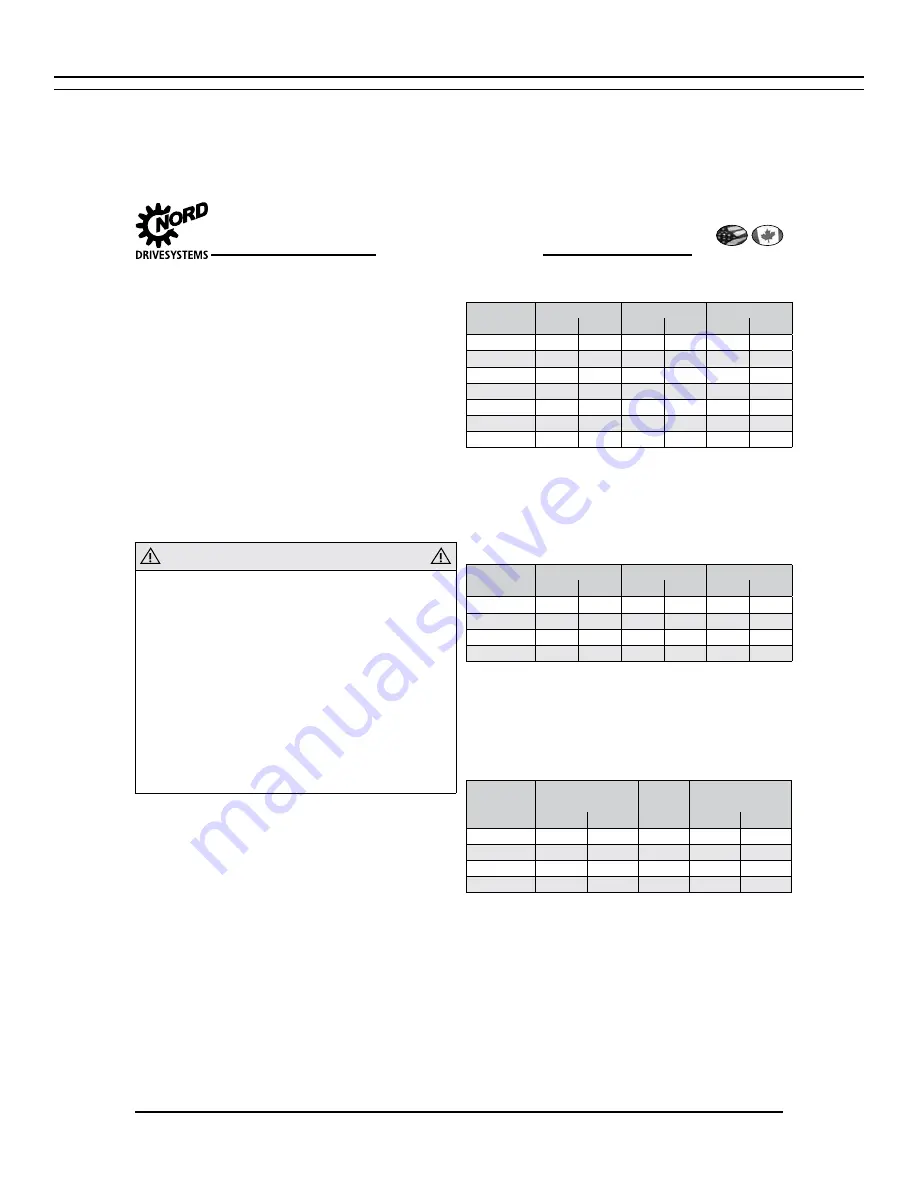
57
NABRICO DF-1 N ELECTRIC WINCH Owner’s Manual
OM-DF1-021-A
MOTOR BRAKES
INSTALLATION & MAINTENANCE
RETAIN FOR FUTURE USE
U35000 - 2 of 19
www.nord.com/docs
06.13.16
NORD Gear Corporation
Toll Free in the United States: 888.314.6673
NORD Gear Limited
Toll Free in Canada: 800.668.4378
General Selection Considerations
As indicated in the NORD catalog, each NORD motor can be
supplied with a number of brake torque sizes.
NORD relies on the equipment builder to specify appropriate
brake sizing for their application, while giving consideration
to the following:
• For most applications, we advise sizing the brake to 1.5 - 2
times the motor rated torque.
• For vertical applications, it may be advisable to size the
brake size up to 3 times the motor rated torque.
• For some applications, it may be necessary to specify a
reduced brake torque setting to prevent excessive peak
load conditions developed at the reducer output.
• On travel drive applications, excessive brake torque may
lead to wheel skid; in addition on crane applications excess
hoist-cable swing can result.
CAUTIONS
• Brake torque - The brake torque is measured with a
mean friction radius of the brake pad surface with a
circumferential speed of 1m/sec (197 fpm).
• Brake torque tolerance - For different applications and
operating conditions, brake torque can vary from
+40/-20% compared to the rated brake torque.
• Hoisting (lifting/lowering) applications - must have the
brake wired for fast response (DC-switching)
• Initial operation & wear-in period - In new condition,
the brake will have a reduced torque of up to 30%.
In order to achieve full rated brake torque, a short run-
in period is required. The run in time will vary
depending on system loads.
• The brake rotor or brake pad - must be protected against
foreign matter, oil and grease. Contaminants of this type
can greatly influence wear and reduce breaking torque.
Brake Torque Adjustment
Brake torque adjustments are possible by changing the brake
spring combinations or by removing springs (Table 1).
In addition, brake sizes from 5-40 Nm (3.7-30 lb-ft) are typi-
cally supplied with a threaded adjustment nut or spanner nut
to allow for additional fine torque adjustments of the brake.
The braking torque can be adjusted by unscrewing the span-
ner nut a number of turns or “clicks” with a spanner wrench
(Table 2).
Table 1a: Brake Torque Reduction - Spring Removal
"Brake Size"
7 Springs
5 Springs
3 Springs
[Nm]
[lb-ft]
[Nm]
[lb-ft]
[Nm]
[lb-ft]
BRE 5
5
3.7
3.5
2.6
2
1.5
BRE10
10
7.4
7
5.2
4
3.0
BRE20
20
14.8
14
10.3
8
5.9
BRE40
40
29.5
28
20.7
17
12.5
BRE60
60
44.3
43
31.7
26
19.2
BRE100
100
73.8
70
51.6
42
31.0
BRE150
150
111
107
78.9
65
47.9
On brake sizes 5-150 Nm (3.7-111 lb-ft) full brake torque is
achieved with all (7) springs. The brake springs are placed
in such a manner where there are (3) inner and (4) outer
springs. When adjusting the brake torque, start by removing
the outer springs at opposite corners to prevent uneven
brake wear.
Table 1b: Brake Torque Reduction - Spring Removal
"Brake Size"
8 Springs
6 Springs
4 Springs
[Nm]
[lb-ft]
[Nm]
[lb-ft]
[Nm]
[lb-ft]
BRE250
250
184
187
138
125
92
BRE400
400
295
300
221
200
148
BRE800
800
590
600
443
400
295
BRE1200
1200
885
900
664
600
443
On brake sizes 250-1200 Nm (184-885 lb-ft) full brake torque
is achieved with all (8) springs. The brake springs are placed
in such a manner where there are (4) inner and (4) outer
springs. When adjusting the brake torque, start by removing
the outer springs at opposite corners to prevent uneven
brake wear.
Table 2: Spanner Nut Adjustment
“Brake
Size"
Torque
Reduction
*
Max.
Turns
Minimum
Torque
[Nm]
[lb-ft]
[Nm]
[lb-ft]
BRE 5
0.2
0.15
6
0.8
0.59
BRE10
0.2
0.15
12
1.6
1.18
BRE20
0.3
0.22
12
4.4
3.25
BRE40
1
0.74
9
8.0
5.90
With the minimum number of springs and
maximum number of turns to the spanner nut.
*
Per each turn of the spanner nut
Brake sizes from 5-40 Nm (3.7-30 lb-ft) are typically supplied
with a threaded adjustment nut or spanner nut. Additional
fine torque adjustment can be made by unscrewing the span-
ner nut a number of turns or “clicks” with a spanner wrench.
Содержание DF-1 N Series
Страница 1: ...OM DF1 021 A NABRICO DF 1 N Electric Winch Owner s Manual ...
Страница 2: ...THIS PAGE IS INTENTIONALLY LEFT BLANK ...
Страница 20: ...20 NABRICO DF 1 N ELECTRIC WINCH Owner s Manual OM DF1 021 A B 1 TYPICAL CONTROL BOX INFORMATION ...
Страница 21: ...21 NABRICO DF 1 N ELECTRIC WINCH Owner s Manual OM DF1 021 A ...
Страница 22: ...22 NABRICO DF 1 N ELECTRIC WINCH Owner s Manual OM DF1 021 A ...
Страница 23: ...23 NABRICO DF 1 N ELECTRIC WINCH Owner s Manual OM DF1 021 A ...
Страница 25: ... A 25 NABRICO DF 1 N ELECTRIC WINCH Owner s Manual OM DF1 021 A ...
Страница 26: ... 72 61 26 NABRICO DF 1 N ELECTRIC WINCH Owner s Manual OM DF1 021 A ...
Страница 27: ... 1 1 2 3 Ω 27 NABRICO DF 1 N ELECTRIC WINCH Owner s Manual OM DF1 021 A ...
Страница 28: ... 63 2 M4 Attachment 28 NABRICO DF 1 N ELECTRIC WINCH Owner s Manual OM DF1 021 A ...
Страница 29: ... 1 1 1 1 1 1 2 2 2 2 29 NABRICO DF 1 N ELECTRIC WINCH Owner s Manual OM DF1 021 A ...
Страница 30: ... uto uto uto uto eset eset eset eset 30 NABRICO DF 1 N ELECTRIC WINCH Owner s Manual OM DF1 021 A ...
Страница 31: ... 31 NABRICO DF 1 N ELECTRIC WINCH Owner s Manual OM DF1 021 A ...
Страница 32: ... 1 1 1 1 2 2 2 2 3 3 3 3 32 NABRICO DF 1 N ELECTRIC WINCH Owner s Manual OM DF1 021 A ...
Страница 34: ...34 NABRICO DF 1 N ELECTRIC WINCH Owner s Manual OM DF1 021 A C 2 PARTS BREAKDOWN SHAFT MOUNTED ...
Страница 36: ...36 NABRICO DF 1 N ELECTRIC WINCH Owner s Manual OM DF1 021 A ...
Страница 69: ...69 NABRICO DF 1 N ELECTRIC WINCH Owner s Manual OM DF1 021 A ...
Страница 70: ...70 NABRICO DF 1 N ELECTRIC WINCH Owner s Manual OM DF1 021 A ...