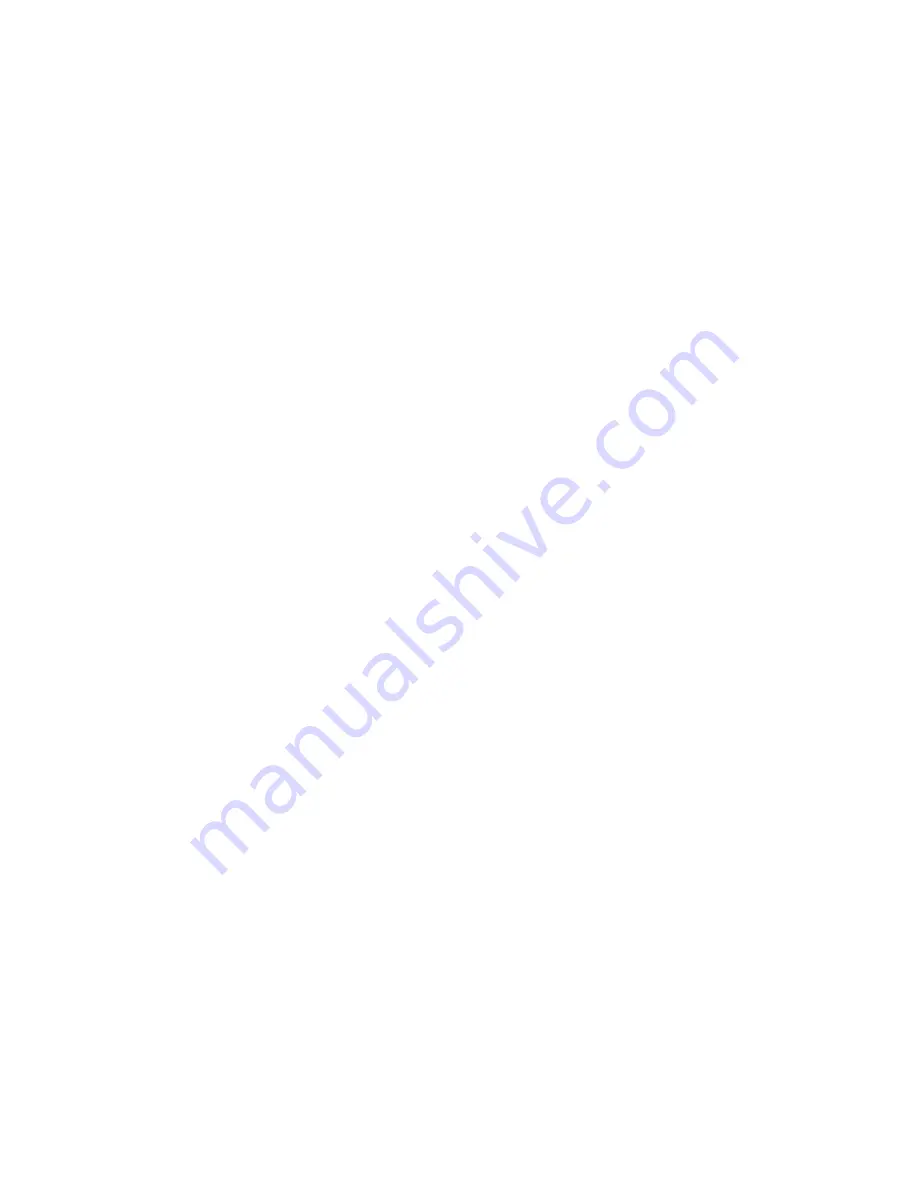
26850A003
12
4. Any piston pump, when operated at high pressure
will not operate satisfactorily or quietly if a mixture
of air and water is allowed to enter the pump
suction. For this reason, a small air leak in the
suction line will cause the pump to knock and
vibrate excessively. This holds true only for a small
air leak which allows the pump to draw a certain
amount of water mixed with air on each stroke of
the piston. A large air leak will cause the pump to
lose prime after which it cannot be reprimed until the
air leak is stopped. Air leaks may occur at the
joints of the suction line piping, at the gate valve in
the suction line, at the gasket sealing the cap on
the sediment chamber or by a crack in the suction
wall of the cylinder body, such as might be caused
by freezing if the pump is not properly drained in
freezing weather. There is also a definite possibility
of air drawing past the packing on the suction stroke
if the packing is badly worn.
5. If the pressure regulator internal bypass valve is
badly worn it will allow too much of the pump
capacity to be bypassed and recirculated back to
the tank. By examining the flow from this valve with
the discharge turned on, it can be determined
whether or not the valve is worn. If a heavy flow
continues when the discharge is turned on, it is
usually a good indication that the valve is badly
worn and should be replaced or that something is
lodged under the valve holding it open.
6. A broken pump valve or spring will often prevent
one cylinder from functioning properly. Very rough
pulsing discharge, a knocking sound, and a loss of
capacity will result. If not repaired promptly, the
rough running pump can cause mechanical damage
to itself or other system components.
7. Badly worn piston cups or valves and valve seats
will cause a serious drop in pump capacity. This will
be indicated by a drop in pressure when guns are
turned on. Worn piston cups are very easy to detect
because of the water leakage. The piston cup
should be replaced just as soon as this leakage is
noticed. If it is allowed to continue some of the
water may work past the piston rod seals into the
pump crankcase. Water in the pump crankcase will
cause severe corrosion of the bearings causing
rapid wear. Worn valves can only be detected by
visual examination of each valve assembly. The
most prevalent cause of valve wear is the use of
highly abrasive liquids which will cause the valve
and valve seat to wire cut. The cut starts as a very
small groove but increases very rapidly once the
valve starts to leak through this groove. If the
valves are replaced as soon as they start to show
this cutting action it will prevent the valve seat from
becoming cut in a similar manner and keep the cost
of replacement parts to a minimum.
8. If a portion of the pump delivery is allowed to
bypass because the #1 control valve is not com-
pletely closed there may not be adequate flow to
develop full pressure. This also will cause rapid
wear in the control valve; any excess flow should be
bypassed only by the pressure regulator.
9. Pump cylinder bodies must withstand an extreme
amount of shock and pulsation while the pump is in
operation. If the pump is allowed to freeze, due to
not being drained, the freezing may crack the
cylinder body walls in almost any location. If the
crack should occur on the suction valve or cylinder
portion of the body it may allow a small amount of
air to enter on the suction stroke and cause noisy
operation or a decrease in pumping capacity. If the
crack develops in the walls between the cylinder
cavities or discharge valve cavity it may allow the
water to flow from one cavity to the adjacent cavity
and rob the pump of its effective displacement.
This will not cause noisy operation but will reduce
the pump capacity and may show up as a drop in
pressure when the discharge is open.
10. Water may accumulate in the pump crankcase from
two sources; the most prevalent being leakage of
the cups as explained in paragraph 7. The other
means of accumulation being a condensation of
moisture inside the crankcase due to changes in
weather or the repeated heating and cooling of the
pump due to its normal usage. Pumps that are
used rather consistently and run for a considerable
period of time to heat the oil and other working parts
will not normally accumulate water by condensation.
If the cups are replaced as soon as it starts to leak
it will be impossible for water to enter the crankcase
from this cause.
11. Worn connecting link bearings will only develop
because of unusual or adverse operating conditions.
They will, however, be seriously affected by corro-
sion if water is present in the crankcase and they
will wear out from overheating if the oil is not clean
and of good quality. For this reason we recommend
thorough draining, cleaning and refilling with new oil
at the specified interval and prior to any storage
period. Replace link inserts as soon as any wear is
noticed to avoid damage to crankshaft journals.
Also see paragraph 17 and lubrication instructions.
CALL 1-800-577-8111 FOR SALES AND SUPPORT
Содержание E110-14
Страница 14: ...26850A003 14 Pre June 1 2008 E70 23 E80 20 CALL 1 800 577 8111 FOR SALES AND SUPPORT ...
Страница 15: ...26850A003 15 Post June 1 2008 CALL 1 800 577 8111 FOR SALES AND SUPPORT ...
Страница 18: ...NOTES CALL 1 800 577 8111 FOR SALES AND SUPPORT ...
Страница 19: ...NOTES CALL 1 800 577 8111 FOR SALES AND SUPPORT ...