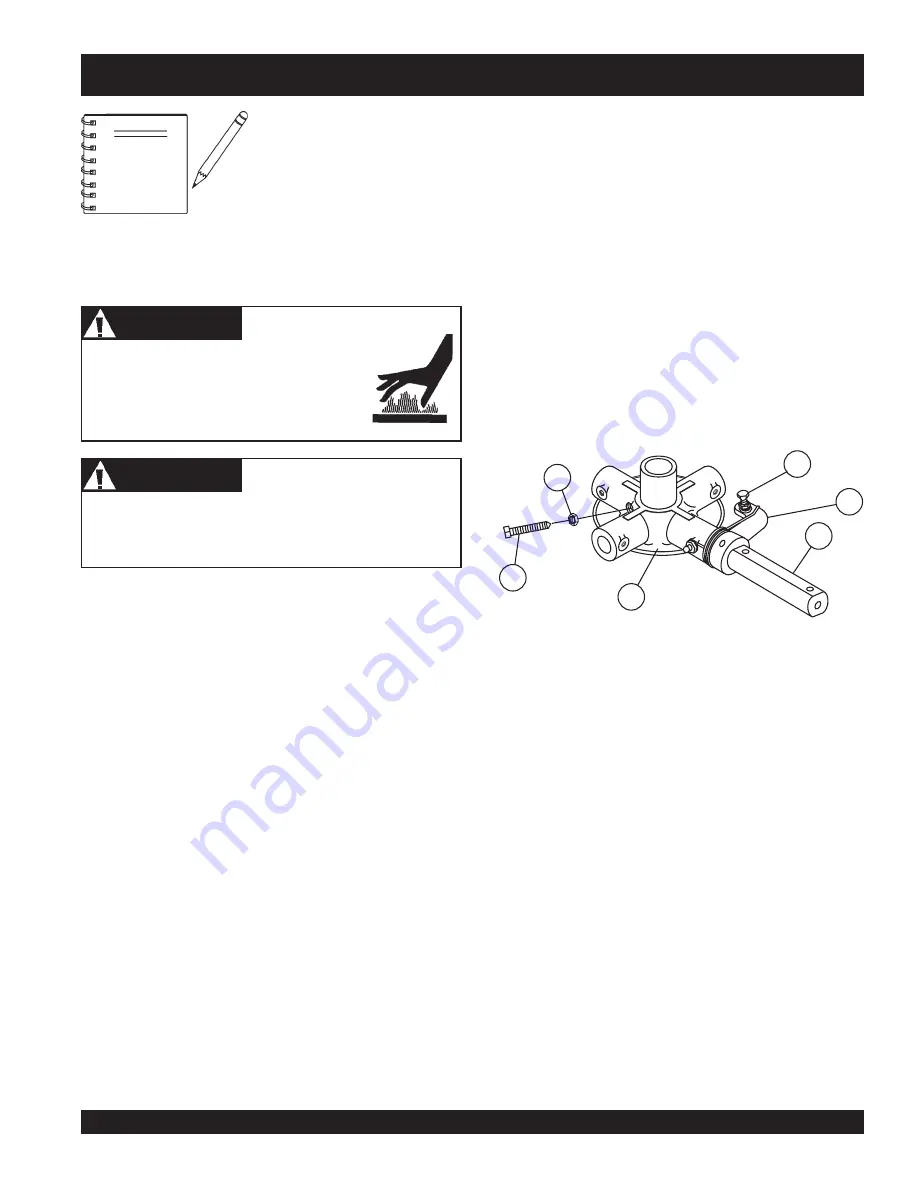
J-36/M-30 WALK-BEHIND TROWEL — OPERATION AND PARTS MANUAL — REV. #0 (12/29/06) — PAGE 31
2
3
4
1
5
6
MAINTENANCE SCHEDULE
Daily (8-10 Hours)
1.
Check the oil level in the engine crankcase and gear box,
fill as necessary.
2.
Check V-belt.
Weekly (50-60 Hours)
1.
Relube arms, thrust collar and clutch.
2.
Replace blades if necessary.
3.
Check and clean or replace the engine air filter as
necessary.
4.
Replace engine oil and filter as necessary, see engine
manual.
Monthly (200-300 Hours)
1.
Remove, clean, reinstall and relube the arms and thrust
collar. Adjust the blade arms.
2.
Remove, clean, reinstall clutch.
Yearly (2000-2500 Hours)
1.
Check and replace if necessary the arm bushings, thrust
collar bushings and shaft seals.
2.
Check pitch control cables for wear.
3.
Adjust blade speed.
J-36/M-30 TROWEL — MAINTENANCE
See the engine manual supplied
with your machine for appropriate
engine maintenance schedule
and troubleshooting guide for
problems.
ALWAYS
allow the engine to cool before
servicing.
NEVER
attempt any maintenance
work on a
hot!
engine.
NOTE
At the front of the book (Page 9) there is a “
Daily Pre-Operation
Checklist
”. Make copies of this checklist and use it on a daily
basis.
CAUTION
CAUTION
CAUTION
CAUTION
CAUTION
CAUTION
CAUTION
CAUTION
CAUTION
CAUTION
Disconnect the spark plug wire from the spark plug and
secure away from the engine before performing
maintenance or adjustments on the machine.
Figure 38. Blade Pitch Adjustment Bolt
The easiest and most consistent way to make adjustments on
the trowel arm fingers is to use the Trowel Arm Adjustment Fixture
(P/N 9177) . It comes with all the hardware necessary to properly
accomplish this maintenance and instructions on how to utilize
this tool.
If a trowel arm adjustment fixture is not available and immediate
adjustment is necessary, temporary field adjustment can be made
if you can see or feel which blade is pulling harder by adjusting
the bolt that corresponds to that blade.
A better way to determine which blades need adjustment is to
place the machine on a known
FLAT
surface (steel metal plate)
and pitch the blades as flat as possible. Look at the adjustment
bolts. They should all barely make contact with the lower wear
plate on the spider. If you can see that one of them is not making
contact, some adjustment will be necessary.
■
If one blade is completely worn out while the others look
new?
■
Does the machine have a perceptible rolling or bouncing
motion when in use?
■
Look at the machine while it is running, do the guard rings
“rock up and down” relative to the ground?
■
Do the pitch control towers rock back and forth?
Look for the following indications if blades are wearing unevenly.
If so, adjustment may be necessary.
Maintenance adjustment of blade pitch is made by adjusting a
bolt (Figure 38) on the arm of the trowel blade finger. This bolt is
the contact point of the trowel arm to the lower wear plate on the
thrust collar. The goal of adjustment is to promote consistent
blade pitch and finishing quality.
Blade Pitch Adjustment Procedure
1
Spider Plate
2
Trowel Lever (Finger)
3
Trowel Arm
4
Blade Pitch Adjustment Bolt
5
Jam Nut
6
Cone head set screw