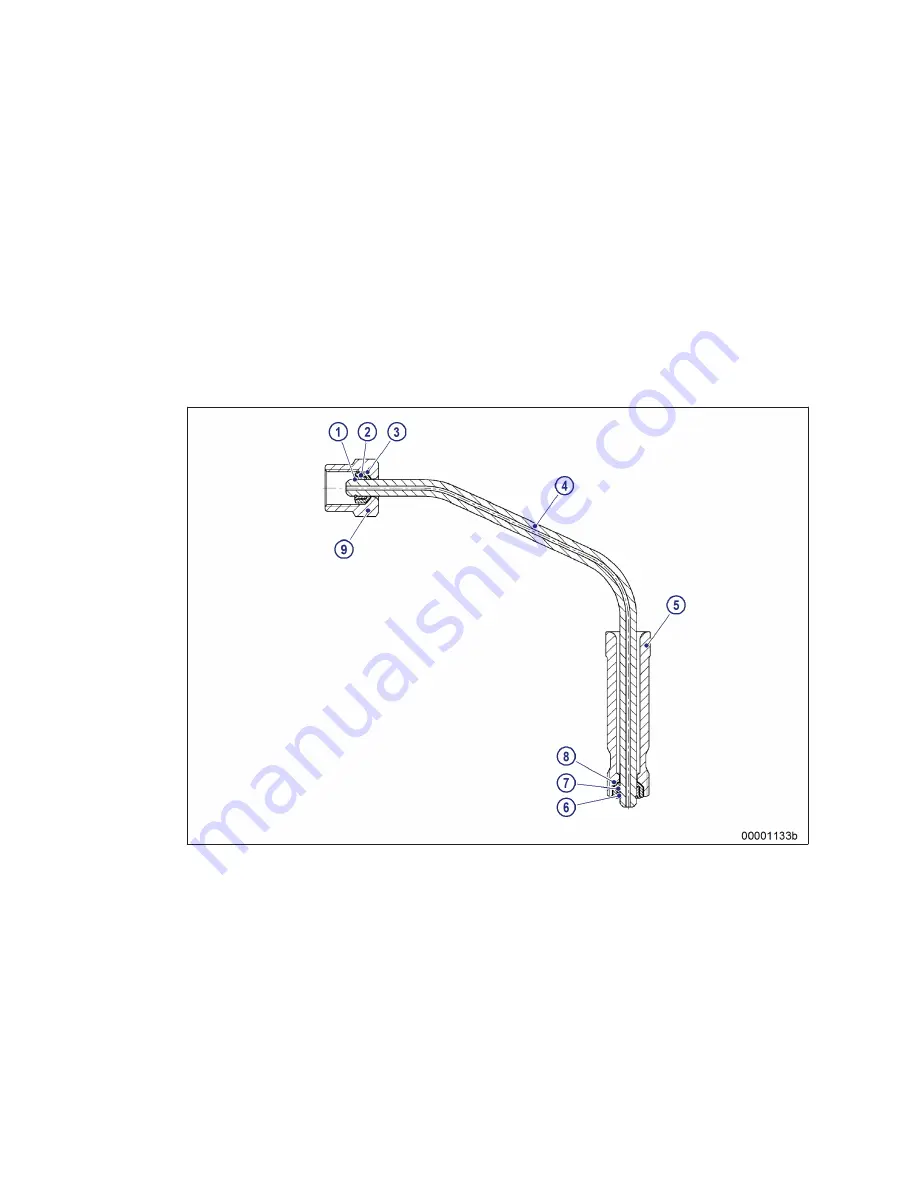
Plug-in pipe union
The sleeve (3) covers the joint to prevent lateral spray.
Only leak-off along the line is possible, the pressure decreases significantly if an O-ring (2) fault occurs.
The connection is confirmed as compliant with SOLAS by DNV and GL.
Plugs and sensors
Screw-in plugs (4) are sealed toward the outside either with a copper sealing ring (1), according to DIN,
or an O-ring (ISO).
In case of a loose thread or a faulty sealing ring (1), the liquid first has to pass the thread.
The pressure is so greatly reduced by this and the faulty sealing ring (1) that any leakage is not under
pressure.
HP line between fuel injector and HP accumulator
1 Support ring
2 V-ring
3 Thrust ring
4 HP line
5 Thrust screw
6 Support ring
7 Thrust ring
8 V-ring
9 Union nut
30 | General Information | MS150119/00E 2014-08
TIM-ID: 0000002177 - 004