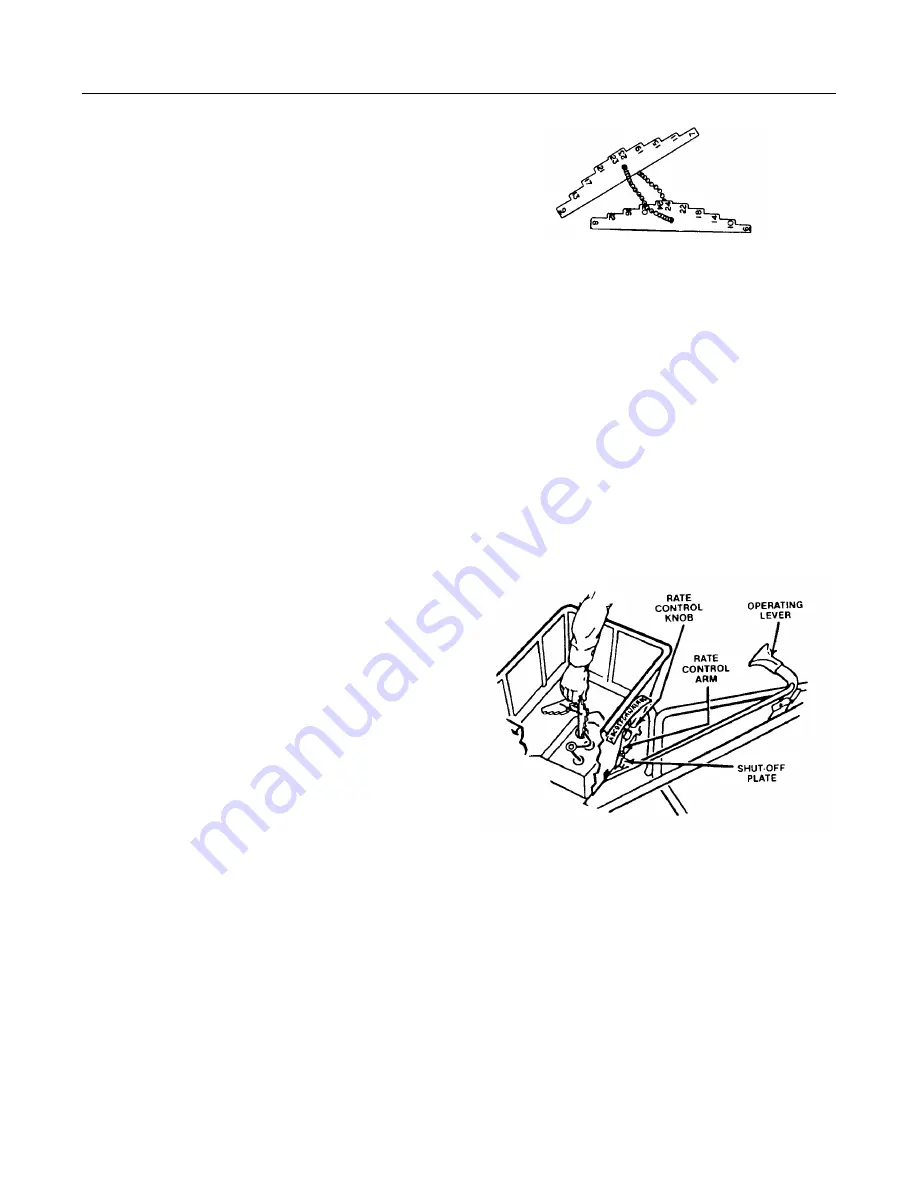
7
Spreader Calibration
Two items must be considered when calibrating a spreader. The first
is the distribution pattern of the spreader. That is, the pattern the prod-
uct makes as it strikes the ground after being thrown out by the
spreader's impeller. There are many factors which affect the distribu-
tion pattern of a rotary spreader and some of them relate directly to
the product. For this reason, we recommend that the spreader be cal-
ibrated separately for every product to be applied. Spreader calibra-
tion should be checked at least once a month, or more often when the
spreader is used frequently.
The second item is the product application rate, that is the amount of
product applied per thousand square feet. This is important because
over-application can be costly and may cause plant injury, while un-
der-application will reduce the effectiveness of the product.
TO CALIBRATE A SPREADER, FOLLOW THESE
STEPS:
Check the spreader discharge holes with the operating lever in the
closed position. If the discharge holes are not fully closed, thread the
upper jam nut on the operating lever rod further up the rod. Tighten
the lower locknut and recheck. Repeat this procedure until the holes
are fully closed.
TO ACHIEVE A UNIFORM DISTRIBUTION PATTERN:
The accurate method for checking pattern uniformity is to lay out shal-
low boxes or pans in a row on a line perpendicular to the direction of
spreader travel. Eleven boxes or pans, two inches high placed on
one-foot centers will provide accurate calibration. To conduct the test,
begin with the pattern slide completely open and set the rate control
arm at the suggested approximate setting. Make three passes over
the boxes, pushing the spreader in the same direction each time. The
product caught in each box is then evaluated to determine the distri-
bution pattern. Weighing the product in each box is the most accurate,
but a simpler method is to pour the contents of each box into a sepa-
rate small vial or bottle. Then set the eleven vials or bottles side-by-
side in order. This makes the pattern variation quite visible.
To reduce the amount of discharge to the right side (operator's right)
the pattern slide should be partially closed and the test repeated until
the distribution pattern is uniform.
TO ACHIEVE THE CORRECT PRODUCT APPLICATION RATE:
The approximate spreader settings printed on any product label
should only be used as the initial setting for calibration. Set the rate
control arm at this approximate setting. Using the collection boxes or
pans, make a single pass over them to determine the effective pattern
width. The effective pattern width is twice (2x) the distance to the point
where the rate drops to one-half the average rate at the center. Ex-
ample: If the product in the vials from the center boxes averages two
inches in depth, count out to the vial which has one inch of product. If
this is the fifth vial from the center and the boxes were on one-foot
centers, the effective pattern width is ten feet (2 x 5 ft.).
Knowing the effective pattern width (ten feet), measure out a lineal
distance to equal 1,000 sq. ft. (10 ft. x 100 ft. = 1,000 sq. ft.). Weigh
20 lbs. of product and place it in the spreader hopper and spread it
over the distance necessary to equal 1,000 sq. ft. (100 ft.). Then
weigh the product left in the hopper and subtract this amount from the
amount with which you started. The result is the application rate for
this product in pounds per 1,000 sq. ft. that your spreader is currently
adjusted to disperse. Adjust the rate control arm up or down as need-
ed and repeat this procedure until the correct application rate is
achieved.
TO USE THE CALIBRATION GAUGES:
The calibration gauges provide a series of "steps", numbered in 1/32-
inch increments, that will allow you to "fine-tune" the spreader. Once
you have calibrated your rotary spreader for the product chosen, open
the operating lever and insert the calibration gauges until you deter-
mine which step fits tightly into one of the open holes in the hopper
bottom. Record that step number for future reference when using that
product. You may choose to set other rotary spreaders for application
of the same product by adjusting the shutoff plate to that calibration
gauge step. This will provide consistent settings for all of your spread-
ers. To recalibrate your rotary spreader after a period of use, adjust
the rate control arm to the "S" position. Open the operating lever and
insert the even-numbered calibration gauge into one of the open
holes in the hopper bottom. Close the operating lever and let the shut-
off plate on the underside of the hopper make contact with the number
ten step on the calibration gauge. Move the rate control arm back to-
ward the "A" position until the bottom of the arm makes contact with
the shutoff plate. If your spreader is properly adjusted, the top of the
rate control arm should be at setting "D". To correct variances, re-
move the rate control arm, place the bottom of the arm (up to the bolt
hole) in a vise, and bend either to the right or the left.
SPREADER TIPS:
1. Always push the spreader; do not pull.
2. Push the spreader at a consistent speed (approximately 3 m.p.h. is
recommended).
3. Always close the operating lever before filling the hopper.
4. Be sure the screen is in place to prevent lumps or paper scraps from
plugging the holes in the hopper bottom.
5. Always start walking forward before opening the operating lever;
close the operating lever before forward motion is stopped.
6. Hold the handle at a height that will keep the impeller level.
7. Empty the spreader after each use. Wash the spreader thoroughly
and allow it to dry. Keep the impeller clean.
8. Lubricate all moving parts. Apply grease to the five grease fittings;
two in the axle supports, two in the gear support and one in the idler
wheel (if the idler wheel has a steel hub).